C.R. England
Salt Lake City
Created the TempStack refrigerated intermodal network to reduce fuel costs, carbon footprint and driver turnover.
Stacking the deck
C.R. England takes refrigerated intermodal to the next level
In the past decade, a number of truckload carriers have launched rail intermodal services. For freight that can be moved in large volumes over long distances, carriers can use intermodal to pass on savings in linehaul and fuel surcharges to customers – and reduce their carbon footprint to boot.
The difference is that with TOFC, carriers can move freight between customers and rail ramps using a standard over-the-road trailer, complete with landing gear and axles. With COFC, carriers have to move containers on a heavy trailer chassis that is designed specifically for intermodal drayage.
COFC offers the most cost-economical option. Railroads charge less for containers since they can double-stack them on flatcars. But COFC presents a challenge for carriers because containers have less cube space than trailers, and the heavy twin-beam steel chassis used for drayage subtracts from payload capacity.
TempStack allows C.R. England to offer more desirable driving positions.
In 2004, C.R. England, the nation’s largest refrigerated transporter, began offering TOFC intermodal services for refrigerated cargo. To roll out this new service, the company made some modifications to its standard 53-foot trailers, such as adding larger fuel tanks. By 2010, the intermodal fleet had grown to 320 trailers, and the company announced that last year its intermodal operations saved the equivalent emissions released from burning 3.5 million gallons of fuel.
The TempStack effect
Last fall, C.R. England launched TempStack, a new type of service that takes refrigerated intermodal to the next level – literally. This effort uses COFC technology to double-stack two high-volume reefer containers on a railroad flatcar. Last November, the Salt Lake City-based company moved its first load using this new technology.
“(TempStack) is a much more efficient way of doing things by having the railroads put two boxes in place of one trailer,” says Zach England, vice president of intermodal. Railroads pass the savings on to C.R. England, which can pass them on to customers – in part to make up for a small loss in loading capacity of a container versus a full-length trailer. “Everybody is a winner.”
While the TempStack containers – which are built to C.R. England’s specifications by Chinese company CIMC – look similar to a standard reefer trailer, one key difference is the addition of a frame around the front to protect the reefer unit. Another difference is that the containers have a 120-gallon fuel tank mounted below the reefer unit.
From end to end, the container is the same length as a 53-foot trailer. Since the TempStack containers have a metal frame around the reefer unit, they lose a couple feet of internal length and overall cube space compared to a full-length trailer.
That loss is minimal, England says. The TempStack containers were designed to preserve cargo capacity in terms of weight, which is more important than cube space to customers, he says. TempStack has an available lading capacity of up to 43,500 pounds.
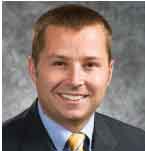
Keeping the payload capacity nearly identical to a full-length trailer was a challenge because the chassis used for intermodal drayage is heavier than the frame of a van trailer. C.R. England worked closely with its suppliers on changes and alterations to lighten equipment. The company’s drayage fleet consists of custom-designed lightweight day cabs that move loads between rail ramps and their final destinations.
The containers have to be loaded differently than standard trailers to distribute more weight at the front. To make this process seamless for customers, C.R. England works closely with customers to create customized loading patterns of freight onto its containers.
Creating a network
By the end of January, C.R. England expected to have 170 TempStack containers in operation, and by the end of the first quarter, more than 300. The additional equipment will create the nation’s largest refrigerated intermodal container fleet and will double the company’s current intermodal capacity.
As part of the effort, C.R. England developed strategic partnerships with railroad companies to open up capacity across select expedited routes of the country’s critical shipping lanes. These alliances have made it possible for C.R. England to build and deploy its intermodal container fleet rapidly.
The TempStack effort also includes technology to run reefer units only as needed to save fuel. Technology also provides quality assurance through two-way communication that allows for temperature and load-tracking management from remote locations for every single container in the company’s fleet. The tracking system allows management to do everything to a unit that they could do in person, from adjusting settings to checking fuel levels and temperature, England says.
With all of these pieces combined, C.R. England has created an extensive temperature-controlled intermodal network that offers significant cost savings, on-demand capacity and a reduced carbon footprint for customers. Every load that travels by container results in one less truck on the highway and a 60 percent carbon footprint reduction, England says. With more than 600 intermodal trailers and containers, C.R. England expects to save the equivalent emissions released from burning 7 million gallons of fuel this year.
Other elements
C.R. England has grown to become the largest refrigerated transporter in the world with services that include national, Mexico, regional and dedicated truckload. England says the TempStack effort will provide benefits that extend across all of these divisions because it addresses key industry challenges such as driver retention and driver shortages.
For driver recruiting and retention purposes, TempStack will create more desirable driving positions as C.R. England successfully converts longer-length hauls to intermodal, and the existing driver fleet also will see a reduction in haul length. C.R. England already has seen a reduction of 100 percentage points in driver turnover for its drayage fleet compared to drivers assigned to an over-the-road fleet. “Drivers are home every night,” England says. “That is clearly a better driving position.”
Longhaul loads can be converted to the TempStack network and move from origin to destination in the same amount of time as a load dispatched to a solo driver. Realistically, the only loads that cannot be converted to TempStack are expedited shipments that require team drivers and loads that don’t fall in its intermodal lanes, England says.
Innovators profiles carriers and fleets that have found innovative ways to overcome trucking’s challenges.
If you know a carrier that has displayed innovation, contact Jeff Crissey at [email protected] or 800-633-5953.