Rocha Transportation
Ceres, Calif.
By Jeff Crissey
For most large truckload carriers, spending hundreds of thousands – or even millions – of dollars on safety programs is considered a cost of doing business to reduce insurance premiums and lower the chance of accident-related expenses. As you move down in carrier size, safety efforts often are reduced due to sizable investments relative to revenues. Too often, small carriers scale back safety programs to the bare essentials, and safety quickly can take a backseat to productivity.
Don’t tell that to Rocha Transportation. Since 2004 – when safety manager Sam Cross came on board with the company – the Ceres, Calif.-based 50-truck carrier has been cultivating a safety program that would make many of the nation’s largest carriers green with envy. The company’s safety program has been so successful that Rocha has been recognized as a National Fleet Safety Award grand prize winner in 2005, 2008 and, most recently, in 2011. But, as Cross says, it’s not good enough.
“We aren’t satisfied with our safety program the way it is,” says Cross. “We are always looking at what we can add or what we can do different.” Even the little issues don’t escape management’s attention. Last year, after two incidents involving drivers slipping, Rocha purchased new boots for everyone to prevent further accidents.
“We have high expectations, but we make it clear that we will provide the tools needed, because it isn’t fair to have expectations and not give employees the means to meet those goals,” says Cross.
Working the plan
Serving wine producers and nut growers in northern and central California, Rocha’s footprint is small and routes are short, allowing its 62 company drivers to return home every night. That type of operation has allowed Rocha to be selective in the hiring process. “The first thing I tell drivers coming through the hiring process is we expect them to make a difference and do their job in a professional manner without incidents or accidents,” says Cross.
Small California carrier develops safety program that rivals some of the industry’s largest fleets.
Performance reviews and communication are the cornerstones of Rocha’s overall safety program. “We work very hard to communicate with our drivers and keep them in the loop and let them know we truly care what is going on in their lives and their jobs,” says Cross. Rocha’s operations manager, Grant Hannink, spends at least an hour every morning in the equipment yard talking to maintenance staff and drivers and listening to see if there are any issues that need to be addressed.
When issues do occur, Cross talks individually with drivers to address behaviors and how the company expects them to demonstrate a behavior change. “I don’t like ‘Teflon’ people that learn nothing because they have a ready excuse as to why something happened,” says Cross. “Then they promise it won’t happen again, but because they didn’t learn anything and the message didn’t stick, they continue the same behavior and expect a different result.”
To monitor driver safety and performance, the company recently developed an in-house driver scorecard system that measures miles, number of loads, revenues, safety issues and repairs on a monthly basis. Drivers are compared against peers in one of the company’s four divisions: container loads, tanker, truckload and intercity truckload.
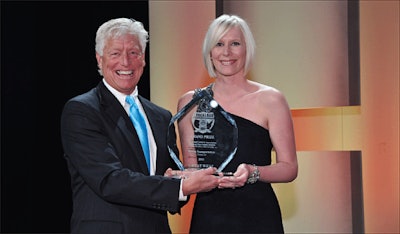
Every month, Rocha management reviews the scores and looks for positive and negative changes and notes patterns. Cross spends time educating individual drivers on their scores and developing safer practices as needed. All safety incidents and truck damage – no matter how small – receive equal attention. “Any damage caused by a driver is charged to that driver, and it sticks out like a sore thumb in that meeting,” says Cross. Management reviews repair and maintenance costs associated with accidents and explains how they adversely affect the driver’s Compliance Safety Accountability scores as well as insurance premiums. “We want to show them how every little thing can adversely impact the business, and when the business is impacted, we all suffer.”
Management also shows drivers where their performance ranks against the rest of the company and takes remedial action if a driver is falling behind his peers. “We have to coach them on changes that need to be made in order to get them where they need to be,” says Corrie Toste, corporate secretary. “Everybody is given a chance to learn, and as long as they’re willing to do that, we don’t have a problem.”
Incentives for safe operation
Rocha has developed a comprehensive incentive program to hammer home the importance of safe driving and accident prevention. Each quarter, drivers that have had zero incidents earn a monetary bonus. If at the end of a year a driver has a 100-percent clean record and has received all four quarterly bonuses, he receives an additional fifth bonus.
In addition, drivers that reach the fifth bonus are eligible for what Rocha refers to as its President’s Award. At the beginning of each year, company management sets an acceptable amount of expenses for small equipment scratches and dents and minor property damage. If at the end of the year the company’s expenses are under the set amount, the remaining money allocated is divided among all drivers with a clean safety record for the year.
Rocha management says that while it’s difficult for a small carrier to dedicate money and resources to developing a comprehensive safety plan, carriers are going to spend the money one way or the other. “You might as well invest and develop a safety program – otherwise you’re going to end up paying increased insurance premiums as a result of a couple of major accidents,” says Toste.
Maintenance matters
When it comes to maintenance, Rocha doesn’t take a wait-and-see approach like many small fleets. The company prefers to spend money upfront rather than wait for a failure on the road that could lead to out-of-service violations and reduced uptime. The company’s shop manager, Allan Freitas, takes great pride in keeping equipment in top-flight condition, and management has made sure that attitude has trickled down to drivers during pre- and post-trip inspections.
“The perspective of our mechanics isn’t that they need to fix things as fast or as cheaply as possible – rather, when they do their preventive maintenance inspections, they look for anything that may need to be fixed in the future and repair it before there’s an issue,” says Toste. “It doesn’t come down to a bottom-line situation for us.”
”We do preventive maintenance the way it should be done so we are not in the repair business,” adds Cross. “We do a great job of managing uptime so trucks go out every day and earn money.”
To help its employees recognize service issues, Rocha participates in annual training luncheons hosted by the California Trucking Association where California Highway Patrol officers spend two hours walking drivers and mechanics through Commercial Vehicle Safety Alliance out-of-service inspections.
The effects of these sessions are clearly reflected in Rocha’s CSA Safety Measurement System scorecard, where the company posts impressively low results in the Vehicle Maintenance Behavior Analysis and Safety Improvement Category (BASIC).
CCJ Innovators profiles carriers and fleets that have found innovative ways to overcome trucking’s challenges. If you know a carrier that has displayed innovation, contact Jeff Crissey at [email protected] or 800-633-5953.