Alternative fuel vehicles are all the rage these days, and interest in their possibilities for commercial vehicles has not diminished even as prices for traditional fuels continue to fall. Regardless of whether the cost at the pump rises or falls, the demand for fossil fuels continues to escalate. Today’s alternative fuel strategies are all about diverting resources away from the most globally popular fuels – diesel and gasoline – to avoid future price spikes and shortages.
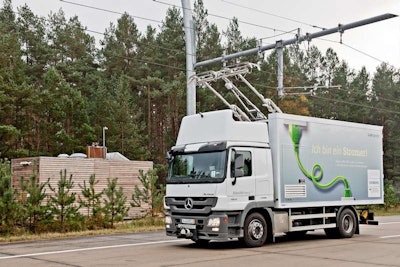
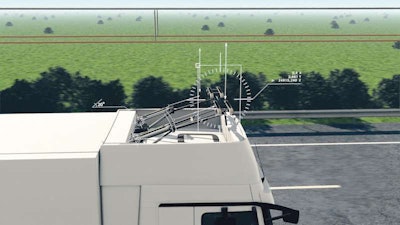
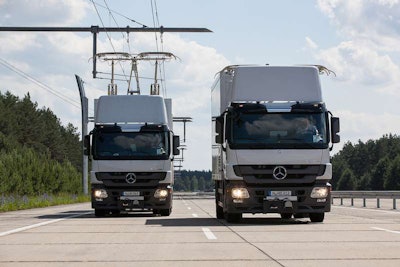
At the moment, the abundant supply of domestic natural gas in the United States is driving growth for alternative fuel trucks running proven engines and technology, with the limiting factors on more growth being the lack of fueling infrastructure and high acquisition costs.
All-electric vehicles also show some promise in limited applications. Fleets such as FedEx and UPS are experimenting with all-electric delivery vans in urban applications, and these vans already are being used with success in European cities. The main concern in the United States is the relatively short range of the vehicles and the resultant “range anxiety” experienced by both fleets and drivers. On the other hand, all-electric vans use no fossil fuels and don’t produce any emissions – particularly attractive benefits in smog-plagued cities such as Los Angeles or Houston.
Experiments in Germany and California with another type of electric truck soon could have fleets considering another way to move freight. The Siemens company, based in Munich, Germany, has long been a leader in railroad technology, and today the company is taking many of its proven rail components and concepts and rethinking them with a goal toward creating an all-new type of highly-efficient low-emissions commercial vehicle.
A highly flexible system
Siemens calls its concept the eHighway Project – an elegant and sophisticated solution that the company hopes has the potential to revolutionize the way freight is hauled along dedicated eHighway corridors in the United States.
At the heart of the concept is a diesel-electric hybrid truck. Unlike hybrid trucks in the States, this vehicle uses a constant-state diesel engine to drive a high torque-output electric motor – the same principle used to drive diesel-electric locomotives around the world.
In this mode, the Siemens hybrid drive system allows the truck to behave much like a conventional diesel truck: The driver is in control of the vehicle and can change lanes and maneuver on freeways and in tight urban surroundings exactly as he would in a truck today.
The twist comes when the vehicle pulls into a dedicated “eHighway” lane that features overhead electrical lines powered by substations – a technology familiar to anyone who’s been to Europe or a major Asian city and rode the subway or trains there.
Once the truck has been maneuvered into an eHighway lane, a continuously-monitoring sensor in the truck’s nose detects the presence of the overhead power lines and automatically deploys a prong-shaped wand called a pantograph. This is the relay system that makes contact with the power lines and acts as a conduit for the electrical power now flowing from the lines and directly to the vehicle’s electric motor.
Holger Sommer, eHighway project manager for Siemens, says the company decided from the outset that its electric truck lane concept would have to be highly flexible and allow conventional truck traffic to use the eHighway lanes if it was going to be successful. It would not make sense from a funding, infrastructure or efficiency standpoint to build exclusive electric truck lanes, Sommer says.
To that end, Siemens engineers developed a completely new pantograph design with a highly intelligent control system. The pantograph not only moves up and down to make connection with the power lines, it also moves side-to-side to maintain contact and counteract normal steering input from the driver. Most importantly, the system is highly flexible: Once on the grid, trucks are not stuck in position as if they were on a slot car track.
Nor are they locked into a predetermined shared speed: Vehicle speed remains completely under the driver’s control. If the truck needs to pass a slower truck in the eHighway lane, the system automatically disconnects from the power grid as the truck pulls out of the lane. Once the slower vehicle has been passed and the driver returns to the eHighway lane, the system automatically reengages the power grid.
The driver also retains full control of all braking and steering functions in electric drive mode – just as he would with a conventional diesel truck, Sommer says. Even better, any kinetic energy generated by a truck connected to the wires is put back into the grid automatically, where it can be used by other trucks.
If the sensor in the truck’s nose is not functioning, the driver can disengage the system manually with the push of a button on the truck’s dash.
Can costs be controlled?
The system’s advantages are considerable, Sommer says. Since the vehicle essentially is an electric truck with an onboard constant-rate diesel engine, it can produce immediate high torque outputs without fuel consumption spikes. Lower-displacement diesel engines power the trucks and run continuously in their most efficient modes, drastically reducing fuel costs and dramatically cutting vehicle emissions, he says.
Siemens has been testing the system extensively in Europe with modified Mercedes-Benz Actros trucks and is confident enough in its progress that preliminary work has begun on building evaluation lanes in California to test the system for use in the United States.
The initial plan is to develop a one-mile stretch of highway near the Port of Long Beach at a cost of $14 million, with the California Air Resources Board now seeking funding. In addition to validating the eHighway concept in real-world trucking conditions, the tests also will seek to determine estimated vehicle and infrastructure costs.
Siemens stresses that the overall infrastructure impact in terms of investment and construction is relatively minimal, and that the system can be installed easily on existing highways and roads – although the Los Angeles Times has estimated a cost between $5 million and $7 million a mile to convert roadways to eHighway use.
It remains to be seen if the California tests will prove out the eHighway concept in the States – and moreover, if the technology can be scaled up for public use within a cost structure that is acceptable to both taxpayers and fleets.
Despite what would appear to be considerable investment in infrastructure and assets, the concept seems to hold promise – and will be interesting to watch as it unfolds.
.usercontent .ad {display:none; }