An aerodynamic evolution
In an era dominated by slab-nosed Fords and Chevys, Chrysler’s 1934 Airflow was a daring innovation. For the first time, an automotive designer – in this case, Chrysler engineer Carl Breer – had developed a car that used streamlined, rounded surfaces to decrease wind resistance. The concept was so interesting that one Orville Wright – an aeronautical engineer of some note – contributed to wind-tunnel tests done on Airflow models compared to conventional automotive designs. Wind-tunnel testing showed that popular designs of the time were so aerodynamically inefficient that they actually performed better when they were turned around backward into the breeze.
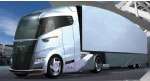
Using this data, Breer and his engineering team set out to develop an entirely new concept in automotive design. Breer’s ’34 Airflow creation, sleek and low to the ground, was a jarring departure from the bolt-upright radiators of the day. Headlamps were flush-mounted at the front of the car on either side of the grille. And because Breer understood that open areas created huge amounts of parasitic drag, the rear wheels were encased in fender skirts to keep air flowing smoothly past the car’s rear.
Alas, the Airflow was not a hit. Plagued by inadequate preparation for the requisite advanced manufacturing techniques and suffering from major quality control issues, the Airflow – as a car model – was history.
In that era, the concept of applying aerodynamics to automotive vehicles was just getting off the ground. Today in the North American trucking industry, aerodynamics is likely to become a watchword for our time. At last month’s Technology & Maintenance Council (TMC) meeting in Tampa, Fla., there was plenty of discussion about the benefits that aerodynamic trucks, tractors and trailers can deliver for fleets. The bottom line sounds promising: Manufacturers say with confidence that a 10-mpg line-haul tractor is entirely feasible with current powertrains simply by reconfiguring external vehicle designs. For example, the MAN concept tractor-trailer has an overall drag coefficient of .29, which according to the German truck manufacturer equates to an overall fuel economy boost of 25 percent – again, with a current MAN engine and transmission.
Tomorrow’s trucks probably will look radically different.
The industry is taking its first steps toward aerodynamics; one session at TMC involved establishing ROI parameters for add-on aerodynamic parts. But the real push will come from the vehicle design and manufacturing sector, and the changes – as the MAN concept proves – may be dramatic. Later this month, Navistar will display a prototype of a computer-controlled speed-sensing system that automatically will move the fifth wheel to adjust the gap between the back of the truck cab and the trailer to optimize aerodynamics. How long will it be before trailer manufacturers are adding skirts to their standard designs or streamlining the overall shapes of their trailers to improve airflow over and around them?
Of course, all of this will mean changes. Tires and wheels will be harder to reach. Radiators may have to be split in order to accommodate aerodynamic designs. Engines and transmissions may have to be moved to different parts of the tractor. On the other hand, aerodynamic vehicles are easier to handle and tend to fatigue drivers less as a result. And they tend to stay cleaner because the air – and the dirt in it – doesn’t catch many parts of the vehicle as it flows past.
The 10 mpg figure that OEMs think they can squeeze out of a tractor-trailer with an aerodynamic design alone makes an aerodynamic evolution worth pursuing. n
JACK ROBERTS is Executive Editor, Trucking of Commercial Carrier Journal. E-mail [email protected] or call (205) 248-1358.