Modern truck technology has evolved from a century-long quest for greater control and visibility of drivers
In 1971, a CCJ editor spent the day with private detective Ed Hegarty to report on an ongoing surveillance project. Earlier that year, the Pennsylvania Motor Truck Association had contracted with Hegarty to detect time abuses by drivers in Philadelphia.
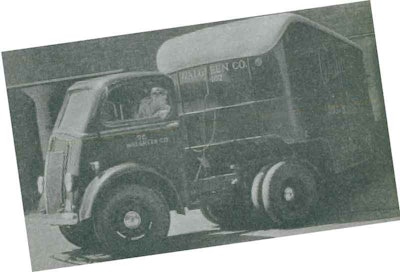
As part of the labor agreement with the Teamsters Union, fleets were paying drivers 13.7 cents per minute in overtime. After months of tracking and tracing vehicles for PMTA members, Hegarty found a regular clique of drivers moving around the city to find hideaways – usually a rundown diner or steakhouse. These drivers were “sitting” on the job for 90 minutes or more in the afternoon.
“I don’t go into the places they go, except once when curiosity got the best of me,” Hegarty said. “When I saw the big blonde behind the counter, I knew what the major attraction was. You can bet it wasn’t the food.”
After spending his days playing hide-and-seek with the Teamsters, Hegarty delivered reports to the fleets that subscribed to the service. The reports showed unit numbers, time of day, duration and the place of vehicle sightings within the Philadelphia commercial zone.

“This is the only way the companies can find out how their drivers are spending their time,” Hegarty said. For the record, Hegarty did believe that fleets using two-way radios appeared to maintain a closer check on drivers, but in any case, his reports sometimes would show drivers miles away from where they were supposed to be or what their logs indicated.
In the past 100 years of CCJ, commercial and private fleets have espoused many ideas and strategies to keep tabs on drivers. In a 1936 article, one fleet manager said drivers always knew someone could be following at any time to check for speed, road conduct and activities at stops. Other fleets contracted with private agencies to stop drivers and make on-the-spot inspections of vehicles and logbooks.
Today, onboard computers, mobile communications and other technologies can do all of this and more without any human involvement. At first glance, these modern-day technologies appear to be a quantum leap from the mechanical devices once used to track drivers. In reality, the technology is the culmination of a century-long quest to put the boss in the cab.
Gaining control
Soon after the first vehicles rolled off the production line, speed governors quickly became standard equipment. Some editors, guest writers and advertisers in early CCJ publications classified drivers as “inexperienced” and “incompetent.” Governors were seen as no-brainers for anyone interested in reducing accident liability and fuel consumption.
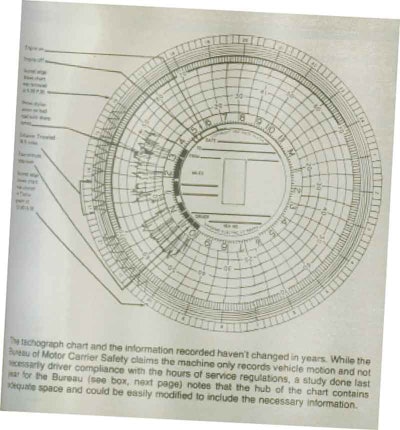
“Just as long as truck drivers are allowed to speed recklessly through the streets or race along country roads, it is useless to expect anything but inefficient and unsatisfactory motor truck service,” stated an April 1917 advertisement from Pierce Governors.
The hubometer was another early technology to check driver behavior. These devices typically were installed in the cab for drivers to see, but the main purpose was to track operating costs by vehicle and driver. Comparing drivers to established fleet standards for cost per mile was a way to “weed out the inefficient, careless or crooked (drivers),” according a 1915 advertisement by an early hubometer manufacturer.
Recording devices brought another dimension to fleet management: time. By the 1920s, fleets could limit speed with governors, monitor cost per mile with hubometers and establish “service time” standards with recorders.
Recorders were driven by the transmission or front wheel. These mechanical devices used a stylus to scratch the waxed surface of a dial chart or tape. The dial charts would show a linear progression of time, by intervals, for the duration a vehicle was in motion or idle.
The dial charts provided a record of driver activity that was “just as positive and reliable as if the boss rode on the truck himself,” stated an article in 1931. More than a check on drivers, the data could be used to balance routes so as to prevent drivers from feeling they had to overspeed to make up time between stops.
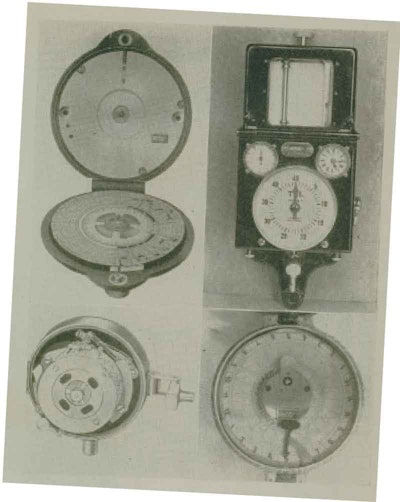
Collecting and analyzing data from recorders was no cakewalk. To uncover driver productivity issues, fleet operators had to transcribe the sketches from dial charts onto paper trip sheets and then compare drive and idle times to their route plans.
Using recorders to monitor engine idling also proved to be a challenge, especially when drivers had to crank-start engines. Many fleets tried to limit engine idling, but these efforts may have ended up costing more than they saved. Labor unions required fleets to provide their drivers with an assistant to help with crank starts as well as loading and unloading.
Setting standards
In the first few decades in the 20th century, fleet managers subscribed to the prevailing school of thought following the Industrial Revolution. To quote from a 1915 CCJ article: “Without haste and without waste, but a time and a method for doing everything.”
The main focus at that time was the physical efficiency of drivers and adherence to standards for everything – speed, time, cost, tonnage, distance, etc. In some cases, this fetish with standards extended to what drivers ate.
In 1938, the management of Auto Transports in Detroit approached 15 eating places along its routes. All the restaurant managers agreed to give attention to the combinations and quality of food they served to the company’s drivers – for instance, serving an orange or a lemon in place of dill pickles and well-cooked hamburgers.
Sometimes, the efforts to track and standardize driver activities were met with strong opposition. Some companies installed recorders secretly, while others emphasized that recorders were used to evaluate the efficiency of the route, not the driver.
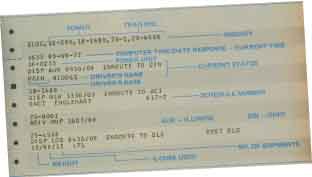
Walgreens began using recording devices in 1926 in a 39-truck operation that serviced 205 stores in the Chicago area. The average minutes per stop became the yardstick for measuring driver efficiency.
The company used recorders to compare daily trip reports to the planned stops a driver had on his docket for the day. Any additional periods of extended idle time, other than the lunch period, had to be explained by the driver, along with any excessive amount of time taken for a delivery.
“The daily charts have been valuable in impressing on our drivers the importance of promptness and the value in saving single minutes,” said a Walgreens manager. Recorders also solved the problem of drivers “spreading out” deliveries to take up a full day, helped keep down overtime and “enabled us to keep such a careful check on our drivers that they do not develop the habit of making prolonged needless stops and then speeding up to get back the time thus wasted.”
Tacking on data
Starting in the 1950s, recorders became known as tachographs. This change was subtle at first with an expanded set of data collection. RPMs now were included with time, speed and distance on dial charts.
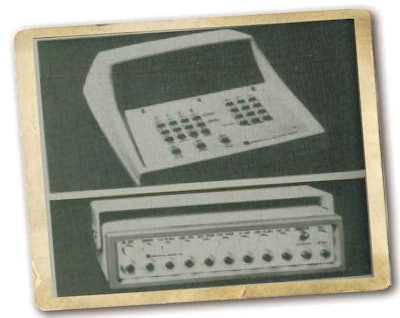
By the late 1960s, tachographs also captured water temperature, vacuum pressure and the time lights were turned on and off. Drivers also could flip a switch to mark state lines, speed zones or unloading time. The first fully electronic tachograph appeared in 1972.
But even the most advanced tachographs were not used to enforce compliance with hours-of-service regulations. In the 1970s and most of the 1980s, a driver’s paper logs were the only documents the Bureau of Motor Carrier Safety allowed carriers to use to track HOS compliance. The accuracy of paper logs was suspect at best.
“In the early ’70s, you were measured by how many miles you could put on,” says Kerry Kearl, who began driving a truck in 1972. A few years later, Kearl became a dispatcher and
fleet manager. “It was not unusual for a driver to put on 200,000 miles a year – you don’t do that legally,” he says. “In the early days, the only question a dispatcher would ask a driver is ‘Can you make it?’ You didn’t ask how many hours he had.”
“In the early days, the only question a dispatcher would ask a driver is ‘Can you make it?’ You didn’t ask how many hours he had.”
By the late 1970s, tachographs drew the attention of the Office of Management and Budget as a solution for the paperwork caused by paper logs. OMB pressured BMCS to find an alternative to paper logs that caused drivers and fleets too much time to record data. For a short period in the early 1980s, BMCS considered mandating tachographs to appease OMB.
In the late 1980s, the Federal Highway Administration — which BMCS was part of — waived the paper logbook requirement for carriers that voluntarily used tachograph-style devices to record drivers’ hours of service. Instead of dial charts, fleets were using portable storage devices to transfer driver logs between the truck and office.
In 1988, FHWA codified the use of these automatic onboard recording devices in Section 395.15 of the Federal Motor Carrier Safety Regulations. Since then, the emergence of the Global Positioning System, wireless communications and advanced onboard computers have added new capabilities to enforcing compliance. In 2010, Section 395.16 was added to codify the use of electronic onboard recorders.
Expanding control
The first real-time check on driver activity came with the appearance of two-way radio communications in the mid-1950s. The technology revolutionized the flow of information. Changes to driver routes could be made instantly as the day progressed.
The devices also could be implemented into a fleet’s safety program. Drivers could notify dispatchers about traffic jams or highway accidents so that other drivers could steer clear of the area. Fleets immediately could learn about incidents involving their own trucks.
In 1963, CCJ noted the difference that two-way communications had made for Eastern Freightways in Carlstadt, N.J. By using a 100-watt transistorized radio system in its 45-vehicle fleet, dispatchers gained the ability to communicate with one driver, a group of drivers or the entire fleet.
Drivers had to check in with the base station at every stop. As information came in from drivers, the dispatchers could update trip cards in the dispatch room, and routes could be adjusted as necessary. When a customer called by telephone, the information was passed to a line dispatcher, who then communicated with drivers.
Radio communications were not a viable option for interstate commerce. Throughout the 1970s and ’80s, dispatchers would give interstate drivers their pickup-and-delivery information by phone and send drivers on their way. “Call me if you have a problem” were the departing words, says Kearl, who today is vice president of fleets for Crete Carrier Corp.
Besides two-way communications with the cab, in the late 1960s carriers began using telecommunications devices for intraoffice messaging and delivery of documents and data. Teletype devices, computer terminals and leased phone lines added a new capability of transferring freight bills between terminals. By knowing in advance of the arrival of freight, fleets could plan dock activities and driver routes more effectively.
Push-button trucking
By the late 1960s, fleet managers began to look at efficiency through a new lens. New computing technology made it possible to look beyond what an individual or group of drivers and vehicles were accomplishing in a given day. Computers made it possible to determine the optimal use of drivers, vehicles and human resources given a set of customer orders for each day, and what changes were needed as the day progressed.
“Knowing what happened yesterday is not enough,” noted a CCJ article in 1972. “Management must have instant access to where tractors, trailers, men and freight are located right now; where they are going and when they will arrive.” Technology appeared to be able to do everything but drive the truck.
IBM developed the backbone of the earliest fleet dispatch and routing systems used to match vehicle types, customer needs and daily delivery schedules into one single operation. To save on computing costs, fleets could use phone lines to connect computer terminals in the office to a vendor’s mainframe computer at an offsite location – an early form of “cloud” computing before the Internet.
In cooperation with IBM, Consolidated Freightways developed one of the most sophisticated dispatch systems of its time in 1972. The new program was called FIRST for Fast Information Retrieval for Surface Transportation. In the year of its debut, the company was able to handle a 12 percent increase in business with 100 fewer tractors.
At the time, the company operated 8,000 linehaul tractors and 180 terminals. When a truck left a terminal, fleet operators instantly knew who was driving, where he was headed, when he would arrive, the load weight, percentage of cube used and number of individual shipments in the trailer. With this information, dock crews could be prescheduled at any terminal.
Even with a computerized office, many processes were labor-intensive: Fleets still had to record arrival and departure times through conversations with the driver, and drivers had to certify their arrival times with the shipper on paper, which then had
to be cross-checked manually with dispatch records.
A network of trucks
The technology that appeared during the 1970s and ’80s began to offer glimpses of what it might be like to have a virtual boss in the cab. Even so, putting a powerful computer in the cab probably would have seemed like science fiction to fleet managers at the time.
Some of the first onboard computers were used by owner-operators, as cellular and satellite communications had not yet linked vehicles to the office. One such device, released in 1978, connected to the vehicle through a speed and fuel-flow transducer. More than 20 readings could be displayed – such as speed, miles per gallon, cost per mile and estimated time of arrival – by programming locations into the computer.
In the late 1970s, fleets began to exchange messages with drivers. Push-button dispatch systems were designed for city delivery and service vehicles. Drivers could push a button on an in-cab device to transmit their status report and truck number. The dispatcher then could send an alert to the driver to call in if necessary. In the office, the incoming status reports were displayed on a dispatcher console.
The first automatic tracking and messaging systems used by fleets appeared in the late 1980s. Through satellite communications, trucks and drivers began to be linked with corporate and customer structures. By 1998, the number of satellite- and cellular-based communications companies had increased significantly.
In 2000, the U.S. government removed Selective Availability (SA) from the Global Positioning System, which increased the accuracy of GPS receivers to within 20 meters, allowing many new GPS applications to emerge. Installing units on vehicles to locate drivers automatically via GPS became the norm, as did saving time by communicating with drivers electronically.
The Internet’s emergence in the mid-1990s provided a fast and easy method for fleets to locate assets, monitor vehicle and driver performance, and integrate the data collected from the vehicle into their dispatch software and other fleet management systems.
Advanced vehicle electronics accompanied the development of onboard computing and communications. The performance of vehicles and drivers now can be tracked instantly and stored for future reference and analysis.
Today, the “virtual” distance between the office and the cab has been eliminated. Quite literally, the emergence of advanced computers, wireless networks and software applications to fit any need has turned the cab into an extension of the office. The boss truly is in the cab.