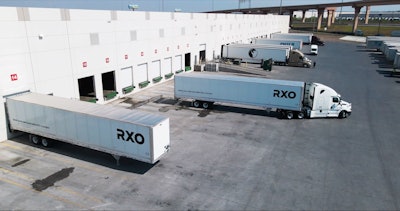
CCJ Innovators profiles carriers and fleets that have found innovative ways to overcome trucking’s challenges. If you know a carrier that has displayed innovation, contact CCJ Chief Editor Jason Cannon at [email protected] or 800-633-5953.
Much of the focus today on artificial intelligence in trucking has been on driver safety and back office efficiencies, but AI opportunities lie where many of trucking's inefficiencies begin: the check-in.
A driver pulls on to a lot, shuffles through various paperwork and hands it over to a guard, who then has to verify it, confirm the driver is on-time, and then check in with the warehouse to find out where the driver is supposed to go nest. That's a minimum of seven steps and one hiccup along the way is minutes, if not hours, of delay.
RXO has deployed AI-powered check-in system for trucks arriving at warehouses and distribution centers. The visual AI technology, which was introduced at RXO’s cross-border facility, identifies trucks via video and extracts image and video data to streamline the check-in and security process and is integrated with RXO’s Yard Management System to automate appointment matching.
"It solved two types of problems," said RXO Chief Information Officer Yoav Amiel. "One is for the carriers overall, there are bottlenecks at the gate, so the inefficiencies, that when they are at the gate and they need to wait for too long. The second thing is around internal productivity and error elimination."
The visual AI technology automates the process of recording trailer numbers and matching appointments when a truck arrives on site, processes previously handled manually, with facility employees documenting truck information and directing carriers to warehouse docks or yard locations. This led to truck backups at the gate during the check-in process due to high traffic, manual documentation and typing errors.
RXO was already using cameras to capturing videos for security purposes in the yard and at the gate. The machine learning layer takes that realtime video feed, identifies the truck information and matches it with the appointment of that driver. To record trailer numbers, the visual AI uses machine learning computer vision and text recognition to process data from a video feed at the gatehouse and extract the data almost instantly. The system then notifies facility staff that a truck has arrived and provides all relevant information.
"The system automatically knows how to identify the different components or numbers or identification of the truck," Amiel said, "matching that automatically to the appointment, and feeding to the yard management system that this truck is now coming in. That saves a lot of time and creates a lot of efficiencies."
RXO’s visual AI technology is already producing positive results at its Laredo, Texas facility, including reduced wait times at the gate, Amiel said, and has already seen a roughly 30% reduction in wait time at the gate and improved input data accuracy.
RXO's AI video-based system absorbs only publicly available information from the truck (any motorists can see the DOT number or unit number), so there's no privacy concerns on the driver's side.
"You're trying to type the name or the information of the truck (manually) and you need to type it now with a keyboard into the system, sometimes you make mistakes," Amiel said. "One of the areas where we invested a lot of energy is making sure that when you take a video, you could have a lot of information as part of the video. It's not just a truck, and we need to make sure that our extraction engine is smart enough to identify the truck itself, to eliminate any noise or any other information that is coming through the feed, and is identifying only the things that we need – and be able to extract that, match it, feed it to the yard management system, and streamline the process overall."
All the investment happens on the facility side. There is no hardware or software needed on the truck or trailer; all that's needed there are clearly visible identification markers like a DOT number and truck or trailer number.
"It's not that we now need every truck to have a specific IoT device or anything on it," Amiel said. "Now, keep in mind, sometimes these numbers could be blurry, or some characters are missing. But this is where technology comes to play. When you have enough information and you have the scheduling appointment out there, you could match with some level of certainty and decide, 'Okay. This is the truck I'm looking for, or this is not the one.'"
And that the system absorbs only publicly available information from the truck (any motorists can see the DOT number or unit number), Amiel said there's no privacy concerns on the driver's side.
"The DOT number is already there when you schedule the appointment. It is not like we're asking for something new," he said. "It's not like we are now holding some precious information or privacy issues. Totally not. It's the same information. You're not being asked to do anything else. You're not being asked to provide any additional information."
RXO plans to implement this system at its other facilities with high truck volumes and plans to offer the system as a standalone service to other companies with high-traffic locations. Even though the system and its current capabilities have yet to be unfurled network-wide, Amiel is already thinking next generation as the system continues to refine itself and its algorithms.
"Our next level is to be able to even do yard cycle counting and warehouse cycle counting," he said. "Think about leveraging drones in real time; self-operated drones. It's like your automated vacuum cleaner; these things that wake up every hour or every whatever cycle of time and scan the information and the drone can feed that video into the system, making sure that everybody's in the yard and the occupation of the slots on the yard is really according to the plan. And if there are any deviation, you could take action instead of creating sometimes chaos if somebody parked in the wrong place or went into the wrong door."
The CCJ Innovators program is brought to you by Bestpass, Chevron Delo, Comdata and Freightliner Trucks.