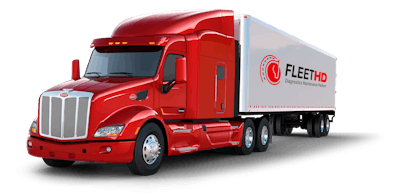
Many people ignore the check-engine light in their personal vehicle, but commercial fleets can’t afford that ignorance. A simple fix, from something like a coolant issue or low oil, could become a catastrophic breakdown, costing thousands, if not tens of thousands, of dollars because of tows, rental replacements, unscheduled downtime, parts and labor and unhappy customers.
“The death of a fleet is when there's a critical alert and it goes unchecked,” said Steve Blair, cofounder of Fleet HD, a software platform that connects fleets, dealers, service centers and parts distributors.
Blair likened the platform, which is seeking to expand following the onboarding of early adopters and fine tuning the service, to a home security system because it actively monitors the vehicle and trailer for the potential event of a breakdown (instead of a break in) and, like bubble wrap, prevents it from happening altogether by notifying the right people at the right time, stopping the small issues before they become big, costly problems.
Blair said one of the largest line items on a carrier’s balance sheet is the capital expenditure on assets.
“If you can keep that truck running longer or get more miles in between major breakdowns, you save a lot of money,” he said. “Labor is more expensive, the equipment is more expensive, maintenance is more expensive. I want to get more miles, more life out of my existing asset, and that's what Fleet HD does.”
How it works
Blair, who previously headed up the segment at Spireon that created trailer tracking for commercial carriers, said one of the common themes he heard from fleets is there was no single unifying platform to pool the data coming from the varying technologies they had invested in from telematics and ADAS to sensors, etc.
“None of those datasets could really talk to each other,” he said. “There are some platforms where you can do an integration, and you can get a wireframe of that data, but there was no unification platform that pulled all that information together and presented it … where you can see all the things that are actionable on a fleet vehicle. That was a big need.”
Fleet HD connects to a fleet’s telematics system, which is already connected to the CAN bus that provides diagnostic trouble code data. It also pulls data from other onboard systems, including cameras, as well as sensors and DVIRs.
Blair said while there are many companies that serve that data up to the fleet, Fleet HD presents it in an organized way with actionable steps to right fix, first time.
All the data runs against Fleet HD’s advanced rules engine, which is customizable by fleet, and that data shows up in the fleet’s vehicle health management dashboard on the Fleet HD app, while email alerts (or text messages) are sent to a designated person within the fleet.
Fleet HD filters those alerts based on priority, severity, fault code type and count, making it easy and efficient for maintenance operations. The platform can also unify data from all vehicles, regardless of OEM.
Fleet HD
Fleets no longer have to manage each technology on the tractor and trailer in isolation.
“Each piece of data from those disparate data systems are integrated together and inform one another,” Blair said. “We essentially wipe out all the white noise, and we just hand deliver up the most important faults to the fleet operator so they can take action and intervene while either that truck is still in the yard or while it's out and about.”
One Fleet HD customer has about 4,000 power units. Blair said they’re not concerned about every fault that’s happening on a vehicle because there are tens of thousands of faults popping off at all times.
This company’s Fleet HD account is set to specific rules so it is alerted when 40 specific fault conditions that could down a truck occur. Those faults appear on their dashboard when certain thresholds are met, and the fleet manager can click into any of those alerts to get additional details, but only the most essential information is initially displayed. Alerts can also be filtered by terminal.
“If you were to turn on the spigot of a telematics device and say, ‘Send me all the fault data,’ the mechanics would say, ‘Turn it off. This is nonsense. I can't get to it all.’ But in our rules engine, we've set it up in a way that it's got to be this fault condition, it's got to reach a count of two or three or five or six in a period of time, and it's got to be at this level of severity before you notify us,” Blair said. “So we're giving you the apples off the tree because they have enough work to do. This really gets to the most important things that you know the fleet operator needs to know about.”
Right fix, first time
The platform goes beyond simply identifying the fault. It also gives maintenance technicians the information they need to fix it.
Fleed HD provides a fault-to-fix repair guide with wiring diagram schematics and component locations – no matter the make, model or year – and step-by-step instructions on how to triage, diagnose and understand the root cause of the problem so it’s not a failed fix.
Fleet HD
“A lot of the older mechanics who have the tribal knowledge are retiring, and the younger mechanics are just inexperienced. If they don’t have the precise repair info, they’ll just MacGyver the fix and that may not be the right fix and still costs thousands of dollars,” Blair said. “Being able to do this makes it more efficient and makes it more effective, so there's better accuracy in the repair procedure, leading to better outcomes and better fleet uptime.”
The platform uses AI, which already knows the context of the vehicle, so the technician doesn’t have to login to the individual OEM diagnostic platforms or third-party repair guidance solution. AI also reaches out to private sources and finds repair information based on the context of the vehicle and fault code and returns it in real time.
Every fault has a time stamp and location. This helps the fleet determine the best course of action. If the fleet sends out a roadside repair technician, the platform helps them identify the right part, the right amount and type of oil, the right mechanic, etc. If it’s a third party, they don’t have to wait for a scan tool to become available and can provide step-by-step instructions.
“There are just tons of different unique benefits,” Blair said.
Results
The platform aims to improve key metrics, including mean time between failures, mean time to repair and maintenance cost per mile, among others, as well as lower emissions and reduce waste.
So far, it has proven to reduce maintenance costs by 23% and has increased mean time between failures by 28% with 19% faster repairs.
Oscar Kafer, director of fleet operations at Coca-Cola Consolidated, said his fleet has benefitted greatly from using Fleet HD.
“The software has reduced our fleet cost by allowing us to capture minor repairs before becoming major downstream repairs. Our road calls have decreased in count and cost. Our technicians know what is wrong with a truck before leaving the shop on a road call, allowing them to come prepared or have another asset on the way if not repairable roadside,” Kafer said.
One customer has improved its days between major failures from 15 to 32, moving the needle from 80% overall fleet uptime to 96%.
Blair said customers are seeing a significant reduction in overall maintenance expense around parts and labor and an improvement in unscheduled or unplanned downtime, saving millions of dollars.
“They have fewer roadside assistance calls because we're getting the things proactively – and soon to be predictively – and notifying the right person in the right time within the fleet that cares about that issue,” he said.
The future
Blair said the next level is prediction. Though the “wine isn’t fully ready to drink” on the predictive side, he said, Fleet HD is working on AI models to go beyond prevention.
Most fleets use an interval-based preventative maintenance approach, which is better than running to failure, Blair said. Fleet HD is trying to understand when an asset might break down based on historical data and make recommendations to the fleet so they can take action predictively.
“We can serve up these recommendations, but then the fleet has to change their operating procedures, and that's a big lift to start having fleets changing out parts and components and downing trucks based on predictive analysis,” Blair said. “But it’s absolutely coming.”