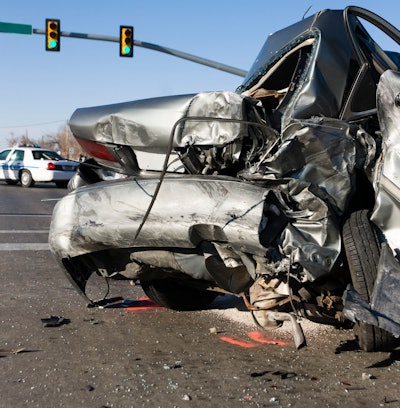
It’s been said that I am a thought leader and someone who thinks outside the box. After you read this column you will probably accuse me of not even knowing there is a box.
As I read articles and think about artificial intelligence (AI) and machine learning (ML) it occurs to me many engineers are not thinking about this new technology landscape of AI for solving very old problems in the trucking industry.
One of the most concerning problems talked about on the nightly news is when a car runs into the back of a tractor trailer at high speed and the driver of the car gets decapitated. It is a tragedy for all concerned.
Even on a busy news night, if there was a decapitation, the newscasters will ask, “Why hasn’t this problem been solved?” Even if it doesn’t make economic sense, citizens are not happy with the thought of getting decapitated.
I think today’s technology can offer a different approach to solving the problem of cars under-riding trailers. My brain has been subconsciously working on this problem since I wrote my very first article on LinkedIn. It is still on my profile dated June 13, 2014, "Connecting the Dots in Technology by a Gonzo Blogger”
Past solutions have not focused on absorbing energy. My solution is modern day, and by modern day I mean still in Auburn University labs studying AI and ML technology. The solution to the underride problem using AI and ML is to redirect and absorb the vehicle energy instead of trying to stop it all at once with an ICC bumper.
My outside-the-box solution is to use a variation of current crash avoidance technology used in the front of tractor trailers to prevent trucks from running into cars – but in reverse.
We would use the system in reverse by putting it on the back of the trailer to detect “incoming” cars. Like a missile defense system that deploys countermeasures, the trailer would have its own countermeasure to prevent a car from under-riding the trailer. Please note, the system is not going to prevent the crash, but will prevent the decapitation.
I am sure the system would need a few tweaks to detect and identify a vehicle that is going to crash into the trailer. The AI system has to determine the car is not going to stop in time before triggering the countermeasure.
The AI system gives the command to deploy a ramp that will direct the car up into the trailer. This is the possibly patentable part. The trailer doors are of a layered design. The outer layer becomes the ramp, the inner layer remains a door to keep freight secure and be the first energy absorbing barrier the car encounters.
Let’s say the inner trailer door is constructed out of the material I first wrote about in June of 2014: Syntactic foam. I am sure there have been materials advancements and development over the last five years that can absorb energy and are cheap compared to syntactic foam.
There will still be death and destruction, but hopefully no decapitation. The system will make a mess of the trailer and the load, but would be worth it to save a life.
Another engineering nuance of the system is the ramp could be designed to shred the tires, thus providing more rolling resistance to help reduce the vehicle’s energy. Think of it as a runaway truck ramp. If the car doesn’t stop at the trailer door then you have 53 feet of loaded or unloaded trailer to slow it down. The front wall of the trailer is the last resort. Maybe unloaded trailers could be filled with special airbags, already deployed, just in case. The possibilities are endless in an artificial intelligence world.
I started this article with this statement: It occurs to me many engineers are not thinking about this new world of AI for solving very old problems in the trucking industry.
Here is a real life example I based that statement on: Recently while trying to get a team of Auburn University senior class engineers started on a tractor trailer project, I reached out to my trucking contacts to support the project. The project is to use the Tangerine Innovation AI and ML system with optimal sensors. These sensors need to be selected and tested by the students to detect the start of a wheel end event by monitoring vibration, heat or some other method to be determined. The students also plan to install the system on real trucks that work at Auburn’s National Center for Asphalt Technology.
Being crushed by a 50 mph dual wheel assembly that weighs hundreds of pounds is as tragic as getting decapitated. The average citizen thinks this is a problem worth solving, even though it may not make economic sense.
Having 18,000+ LinkedIn connections I can reach out to many trucking executives. At a key company for this project, I was connected with the top marketing director. An interesting thing about connections, my connection and I had connected years ago when we both were doing different things. Here we are years later crossing paths again.
I sent him the plan for the student project. As it turned out, the marketing department had proposed some wheel end sensor product development to the engineering department, but marketing hadn’t figured out the AI and ML part and engineering did not want to venture that far into the future. So, engineering passed. That was more than a year ago.
Marketing engaged with me because now that a year had passed – and out of the blue a research university was now knocking on their door with the AI and ML solution in hand – marketing thought the engineering department would jump at the opportunity.
Without going into specifics, this is my impression of the engineering department’s response. I have no way of knowing for sure what really happened.
The engineering department is too busy with today’s issues. They don’t have time to spend on the future. Their marketing department was all for developing tomorrow’s product, but not engineering. I gave my contact in marketing this story Dr. Deming told in one of his last interviews to help engineering to see the light.
"Quality is characteristic of a product or service that helps somebody and which has a market. Without the market, we don't stay in business. Sometimes the market has to be created. But, the market itself is not enough. For example, today, where are the makers of carburetors? Gone. Every engine had a carburetor. How could it run without one? The maker of carburetors made better and better carburetors, lower and lower cost, and went out of business. What happened? Came the fuel injector, which costs more than a carburetor, but does the job of the carburetor and a lot more. The fuel injector came in, carburetors went out. Carburetor manufacturers made a good product, better and better carburetors, lower and lower cost, happy customers. But that is not a sound basis for a continuance. You must take account of possible changes. The function of the carburetor, as everybody knows, is to put a stoichiometric mixture of fuel and air into the combustion chamber. That is its function. Now what is the best way to accomplish that? Maybe by a carburetor, maybe not. Fuel injection provides a better way. Fuel injectors took over the market. Carburetors went out, no matter how good they were. In due time fuel injectors will go out with a new kind of engine. Don't ask me what it might be; I know not. But you must think of function, not particular products”.
I also told marketing that we don’t need engineering time if that is the issue. Just provide the students with engineering material they should already have on hand, and loan the students some equipment to do their bench testing. If engineering has any prototype sensors on hand, please send them down to Auburn.
I told marketing to make sure their engineering department understands what an outstanding response my column “What’s in it for me?” got from the trucking industry. Helping Bob help Auburn help the trucking industry because it is fun for Bob and the right thing to do will generate a ton of great PR. Corporations love great PR. Do it for that reason alone.
Did they say, “Yes Bob, we want to be part of the future. Here’s what we can provide.” No they did not.
They didn’t even say "no." Instead, they just hid behind voicemail and quit answering e-mails and LinkedIn conversations.
But I always have a plan B and a plan C. Please contact me if you might help me come up with a plan D for the wheel end project, just in case. We need sensors and ideas on how to deploy them at the wheel end.
The wheel end project is much tougher than the fan clutch project was. The upcoming turbocharger project should be easy, and we still have the fuel economy testing that uses Tangerine innovations AI & ML to duplicate the SAE/TMC type II, III and IV test on the horizon. If this summary left you with questions, maybe you should review my column “Trucking Fleet Innovations are about asking the right questions”.