Optimization systems can build capacity without adding trucks and drivers
By Aaron Huff
Judging by the latest business trends and analysis, truck capacity will continue to shrink for some time. Although freight volumes have rebounded, many fleets aren’t yet replacing their equipment, let alone expanding, given today’s profitability levels and new trucks costing north of $120,000.
Information technology cannot power loads, but it can be used to add capacity. Load planning and dispatch software systems have the basic tools to match capacity with demand – or more specifically, power to loads.
The power-to-load matching process becomes more complex with size. Truckload carriers that have fairly dense freight networks often will supplement their load planning and dispatch process with optimization tools. These advanced systems gather a wide array of data and use algorithmic equations to identify ways to increase capacity without adding trucks.
Finding balance
TMW Systems now offers various optimization products by way of its 2008 acquisition of IDSC. Hill Bros. Transportation uses several TMW products to allocate capacity more effectively on a daily basis. Within the first five minutes of each workday, the Omaha, Neb.-based company’s load planners and customer service representatives know where adjustments are needed to balance the power and loads in its freight network.
“If you don’t understand your network and balance, you are going to have problems,” says Jack Christensen, Hill Bros.’ IT director. The company uses a report from its IDSC Trip Alert software that identifies areas of load imbalance in time to make corrections. “In an industry that is reactive, this is proactive,” Christensen says.
The 350-truck company also uses IDSC Netwise to evaluate the profitability of each load within its network. The Netwise system uses a profitability measurement called yield that is based on the variables of revenue, cost, time and network flow. “We want to make sure we get the right price on the right lanes for our freight mix,” Christensen says.
Technology is a capacity multiplier.
Hill Bros. also uses IDSC Trip Alert to look for opportunities to remove slack time from its network by changing delivery windows, dropping and/or swapping loads and scheduling preventive maintenance or safety meetings for drivers.
In the past six months, the fleet has reduced its empty miles by 1.8 percent while increasing its yield by 12 points and load volume by 1.95 loads per month per truck.
TMW Systems also offers IDSC MatchAdvice, a tool used to automate the power-to-load selection process. The system also can help fleets make load assignments days in advance by projecting driver availability and hours remaining for dispatch.
Capacity multiplier
Manhattan Associates offers several optimization tools in its Carrier Suite of products. Driver&Load integrates with all major dispatch software systems and provides a recommendation engine for driver-load assignments. Manhattan also offers Drop&Swap to identify opportunities for en route swapping of drivers and loads.
Carriers traditionally have used Drop&Swap to prevent customer service failures in the event of a breakdown or a driver running out of hours. However, only using the tool to manage exceptions can lead to missed swap opportunities and possible improvements in efficiency and customer service levels, says Oren Wilcox, technical director of Carrier Suite. For example, freight might show up at the last minute that needs to be moved quickly.
This year, Manhattan added a new enhancement to Carrier Suite called Swap Finder. Rather than wait for an exception to occur, Swap Finder uses an automatic swap searching engine to identify beneficial swaps within the current state of operations.
Swap Finder recognizes slack time in drivers’ schedules when they are under dispatch en route to the next location. The tool identifies locations along these routes with freight that needs to be moved and recommends load swapping opportunities with en route drivers. The dropped loads then become inputs into the recommendation engine and assigned to someone else.
All carriers face the same capacity challenges and always are looking for ways to increase revenue before adding equipment. In the fast-moving business of trucking, optimization software can deliver the best capacity-enhancing recommendations to the right people at the right time.
IN BRIEF
* Vigillo (www.vigillo.com) announced its Vigillo PSP onverter application designed to convert FMCSA Pre-Employment Screening Program reports into Vigillo CSA Scorecards for carriers to analyze driver candidates.
*Xata (www.xata.com) is integrating and reselling ZoomSafer’s software solutions, FleetSafer Mobile and FleetSafer Vision, both of which can be customized to a fleet’s specific mobile phone policies.
*PAR Logistics Management Systems (www.parlms.com) announced new trailer management systems, the DT200 for dry van and the FT200 for flatbed/intermodal chassis.
*JSY Software (www.jsysoftware.com) announced the availability of OneTerminal TMS V2.0, a software application for trucking companies that manage operations from a single location.
*Air-Trak (www.air-trak.com) launched Xconnect, a software solution designed for managing and controlling mobile work forces and assets. Xconnect uses the latest Silverlight technology from Microsoft to leverage Air-Trak’s new G3 in-vehicle computer.
* PCS Software (www.pcssoft.com) announced that its Mobile XpressTrax for the iPhone now is available to carriers and brokers running its Express transportation management system. The mobile dispatching system is available for download at the App Store.
* ABF Freight (www.abf.com) now has a mobile logistics tool available as a free download at the iPhone App Store. The ABF Mobile for iPhone tool is designed for customers to track shipments, get rates, find locations and schedule a pickup.
McLeod adds CSA scoring to flagship products
McLeod Software, a provider of transportation management software, released LoadMaster and PowerBroker Version 10.2. The new versions of its flagship products for carriers, private fleets and freight brokers incorporate functionality to help companies collect and manage information from the Federal Motor Carrier Safety Administration’s Compliance Safety Accountability program.
With the release of PowerBroker Version 10.2, McLeod Software says freight brokers not only can monitor carrier CSA scores but also can use more analytics to help keep track of costs, margins and revenue.
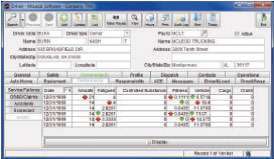
New reports that accompany the CSA compliance management enhancements to LoadMaster give carriers details about each driver’s inspection history, past violations and documented corrective actions.
Carriers running LoadMaster Enterprise can keep track of the CSA Behavior Analysis and Safety Improvement Categories (BASICs) for their drivers with downloads from the FMCSA Compass Portal. New functions in LoadMaster also allow carriers to input roadside inspection data from drivers before it shows up in FMCSA’s database. Together, McLeod says these tools will help carriers manage their BASICs and document their compliance efforts.
LoadMaster Version 10.2 also includes new features to manage driver home time, monitor trailer sensor data, streamline customer quotes and monitor customer activity levels based on historical patterns.