Changes loom for truck, engine designs
Variety of technologies needed to curtail emissions further
President Obama, the U.S. Department of Transportation and the U.S. Environmental Protection Agency, with considerable cooperation from the trucking industry, have set ambitious fuel economy requirements for heavy trucks to achieve by 2017 – model year 2018 – in order to control greenhouse gas (CO2) emissions.
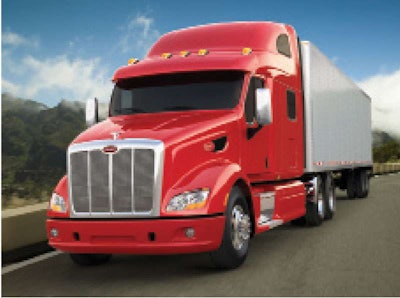
The standard is based on gallons per 1,000 ton miles of cargo hauled, a bit arcane and difficult to understand at first versus the traditional miles per gallon. With a 45,000-pound cargo, a tractor-trailer will produce that 1,000 ton-mile measure of productivity every 44.44 miles.
A low-roof sleeper that consumes 6.5 gallons per 1,000 ton-miles would need to achieve 6.837 mpg to meet the standard. Because the standard is based on total fuel consumed – even while idling – it actually involves an improvement in the range of 20 percent.
Landon Sproull, Peterbilt chief engineer, says EPA spent a lot of time with the industry to develop the standard. “They were not totally unreasonable in determining what the standard would be,” Sproull says. Determining the final details for each of the many vehicle categories is complicated, as the final rules are based on the 20 percent improvement criteria. Sproull says work still is being done to determine the starting point for each vehicle category.
Aero add-ons
By comparison, meeting the initial less-stringent 2014 standard won’t be a technical challenge. “It will be manageable with the content we have,” says Rick Mihelic, manager of greenhouse gas standards for Peterbilt. Areas where the truck will be modified likely will include aerodynamics and vehicle weight, and possibly controls such as idle shutdown and vehicle speed limiting.
No one knows exactly what we’ll see in 2017.
Peterbilt also is conducting a careful study of tractor-trailer integration. “We’ve compared standard trailers with aerodynamic trailers in our in-house work with customers, accumulating experience and data on how much difference the aerodynamics make,” says Sproull, who believes more aerodynamic improvements will be needed on both tractors and trailers to meet the standard.
Some EPA-certified tractor-trailer combinations include heavy aerodynamic treatment of both units, Mihelic says. “That kind of redesign will represent an important first step in the design process,” he says.
The next step will involve innovations developed through the SuperTruck program in which each OEM is participating with a variety of suppliers. The program already has yielded more advanced aerodynamic devices, idling solutions and even an “energy recovery” technology that involves capturing the energy present in the engine’s exhaust.
Powertrain specs also may have to change. Smaller engines may be sufficient for trucks that run in applications where maximum horsepower is not always needed. “Smaller engines today offer good horsepower and torque, and may not only save fuel but provide a weight and payload advantage,” Sproull says.
Mihelic believes the industry may use more aluminum for weight savings, as well as other means to help fleets run trucks more efficiently such as additional driver training and in-cab technology that provides more information than currently available and “ensures that the driver and truck are more effectively integrated.”
The new standard, while likely to increase truck prices, could end up being a big benefit to fleets. “We’ll take the best improvements and combine them in such a way as to deliver the best value to the customer,” Sproull says.
Engine options
Volvo Trucks is confident it can meet the initial 2014 target through strategic deployment of existing technologies, but “achieving the 2017 standard will likely require new engine-related technologies outside our current product offerings,” says Brandon Borgna, manager of media relations.
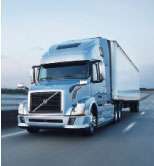
So where could engines be heading? Cummins’ lineup of North American on-highway engines will be certified to meet new onboard diagnostic requirements by January 2013. To provide a single product launch and multiyear stability for customers, these products also will comply with the initial GHG and fuel-efficiency targets.
“The emissions technologies in use today provide the foundation for meeting the 2014 standards,” says Steve Charlton, vice president and chief technical officer of the company’s engine business. “Certifying our engines early will deliver additional fuel economy benefits to end-user customers and provide installation stability to our OEM customers.”
Charlton says Cummins is confident that selective catalytic reduction remains the right technology for North American on-highway truck markets. “As such, we do not feel that the standards that take effect in 2014 will lead to transformational changes,” he says. Looking forward to 2017, Cummins is investigating technologies such as hybrid powertrains and waste-heat recovery.
Detroit Diesel’s turbo-compounding system is more than halfway there, but the full system entails using a different fluid that will be converted to vapor via a heat exchanger through which the hot exhaust is passed, much like the present EGR cooler but operating at a higher temperature. This fluid will expand through a turbine and then be condensed in a heat exchanger exposed to outside air and pumped as a liquid back to the exhaust-powered heat exchanger.
In some respects, it would resemble an air conditioning system, though effectively operating in reverse, producing mechanical energy from heat rather than using mechanical energy to move heat from one location to another.
The turbine then would be used to generate power for onboard use via its own generator, or perhaps to supplement engine power via a motor generator on the flywheel, a component at the heart of hybrid technology. It even could be coupled to the crankshaft, much like Detroit Diesel has done with the turbo-compounding turbine of its DD15 and DD16.
Radical revisions
Other potential radical combustion system improvements could see the light of day by 2017, even though the engine makers haven’t mentioned such possibilities. Pre-mixed charged compression ignition (PCCI) is impractical for use at full load but might be effective under level-road cruise conditions. It requires variable intake valve timing but can use a conventional injection system.
In normal diesel practice, the fuel is not injected until just before top dead center (TDC), and even then is forced in over a number of degrees of crankshaft rotation. The injection system determines both when the fuel ignites and how fast it burns. With PCCI, the fuel is injected in a short spurt, relatively early and well before TDC.
To prevent preignition, the compression ratio is adjusted to an abnormally low level by holding the intake valve open until the piston has gotten much farther up in the bore than normal. The right lower-compression factor can be effective in precisely controlling the ignition’s timing. The end result is better fuel economy than a standard diesel under cruise conditions, as well as lower emissions because the fuel is mixed with the air more completely.
Of course, nobody knows exactly what we will see by 2017. What is clear, however, is that in spite of some inevitable costs, overall cost per mile is likely to be improved greatly because of the significant fuel savings to come.
Medium duties, heavy hitters
Medium-duty engines may pack less horsepower than their on-highway cousins, but spec’ing decisions can’t be taken lightly
By John G. Smith
A “medium-duty” label doesn’t really do justice to the engines that power everything from package delivery vans to utility trucks. True, they may lack the horsepower and torque of some of their Class 8 counterparts, but these power plants are expected to perform over a wide variety of heavy applications.
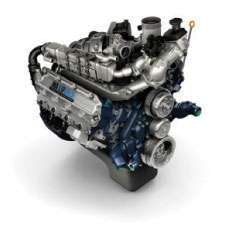
Despite a growing list of demands, however, one measure of performance seems to be gaining more attention. “For the midrange diesel folks, fuel economy has become nearly as important as it is to the heavy-duty folks,” says Steve Jenkins, Navistar’s director of MaxxForce 7-10 engine sales.
The focus hardly is limited to trucks that travel the most miles. Kris Hus, Freightliner’s commercial chassis product manager, points to vocational trucks on a construction site. “There’s a lot of PTO and idle time in that application,” Hus says. Today’s users are more likely to look for preset limits on idling or emerging hybrid technology that can offer other power sources.
Spec’ing together
Solving the increasing demand for better fuel economy – or at least part of it – likely will involve a closer relationship between dealerships and the people who use the engines.
“The consultative approach that we always used becomes expanded into understanding exactly how our customers plan to use our engines in the vehicle,” Jenkins says. Dealers need to access more information such as the number of expected PTO hours, annual mileage and gross vehicle weights to better match the application. “In the past, a lot of our customers have tried to be as versatile as possible with their equipment, and that seems to have changed,” he says.
A closer engine-transmission connection has yielded performance gains.
Some of this information will be drawn from past experience. Electronic control module data can offer an idea of the way an existing engine was run. But Tim Shick, Navistar’s vice president of North American engine sales, also stresses the value of personal insight, suggesting that sales reps join their customers for a ride and gather answers to several important questions. What do the majority of the routes actually look like? What kind of geography will be traveled? How heavy is the traffic, and how does that affect the top speed?
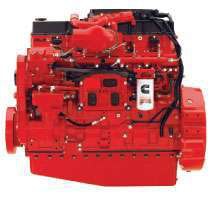
Every business will change over time; the demands on the engines in its trucks also can change. “Things have evolved and improved, and geared speeds – rpms – have been reduced, so what you were [using] five years ago probably wouldn’t be serving you the best today,” Jenkins says.
Performance gains
The advances are more dramatic compared to 20 or 30 years ago when an engine rated at 2,300 rpm likely would be spinning at that rate once it hit 55 mph in the highest gear, Shick says. Any discussions about fuel economy tended to be limited to the switch from gasoline to diesel. Advanced turbocharging and rear axle gearing now allow the engines to run slower while still delivering peak power and responsiveness.
“The idea of a medium truck holding up traffic is really a thing of the past,” Shick says. Navistar’s DT and MaxxForce 7 engines deliver peak torque at about 1,400 rpm. A generation ago, a speed of 1,600 rpm would have been more likely. “The engine would have had a rated speed as high as the high-2,000s rpm range, where today’s rated speeds are in the mid-2,000s,” he says.
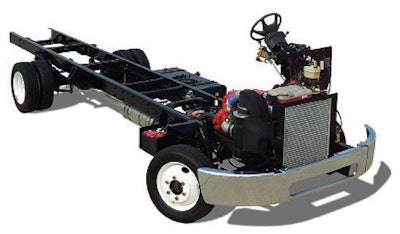
Some of the performance gains have been realized through a closer connection between the engine and the transmission, which today is more likely to be automatic. These trucks tend to be driven by people who see the vehicles as a tool for the job; as much as they may drive, they seldom would see themselves as gear-jamming truckers.
The electronic controls behind emissions-related technologies also have contributed to performance. While ultra-low-sulfur diesel holds less energy than its sulfur-loaded predecessors, common rail fuel systems deliver higher fuel pressures, and turbochargers deliver a valuable boost of air at low speeds. “A lot of that was brought about by exhaust gas recirculation,” Shick says.
The electronics that support these controls have made their impact in more ways than one. FedEx’s interest in preserving tire life led to acceleration rate management, varying the output of the engine as it operates in lower gears. This way, there is less worry about damage from a driver who would “mash the pedals and light up the rear wheels,” Hus says. A growing number of engine buyers also are interested in in-dash fuel economy gauges that traditionally were limited to hybrid products.
Combined with improved oil formulas, the cleaner engines also are putting less strain on the oil in the crankcase. Typical medium-duty engines have drain intervals set somewhere between 5,000 and 10,000 miles – similar to many of the intervals enjoyed 20 years ago before EGR – and thoughts of extending oil drains aren’t limited to linehaul trucks. “In the medium-duty, it can be done through the right monitoring of oil and understanding what the life actually is,” Hus says.
The bottom line
Of course, the technology of cleaner exhaust comes at a cost. A medium-duty diesel engine now can cost $10,000 to $15,000 more than its gasoline-fuelled counterpart, Hus says. That gap in price may lead some buyers to consider whether they really need the diesel engine’s higher torques at low rpms, or if their business plans support anything more durable than a gasoline engine.
The challenges have not been limited to prices. Some medium-duty designs struggled with the introduction of early diesel particulate filters. The engines in trucks that make about 35 deliveries in a shift simply didn’t reach the higher temperatures needed for passive regenerations, says Mike Rumsey, vice president of sales operations for Mitsubishi Fuso Truck of America. But the addition of diesel exhaust fluid has cut the number of manually activated regenerations in half, says Rumsey, referring to MitFuso’s 4P10 lineup.
DPFs and DEF tanks also need more physical space. “It’s taking up real estate on the cabover on the outside of the frame rail, aft cab on the passenger side,” says Rumsey, referring to the way components have been mounted on the body of MitFuso’s trucks.
When asked about the emerging options that will affect users the most, Rumsey points to trends in telematics, referring to one customer who uses sensors to monitor everything from engine operating conditions to tire pressures, and to schedule preventive maintenance. Freightliner is working with a customer on a sensor that will read the current drawn from the engine’s starter, predicting a failure before it happens; this could make a difference in a heavy-stop-and-start application that requires one or two new starters a year.
It’s just another way that the technology in smaller commercial engines will continue to make a big business difference.