Rolling repairs
Today’s mobile service trucks, and the programs they support, are more sophisticated than ever
As long as trucks continue to break down on highway shoulders, mobile service equipment will play a vital role in roadside repairs. “We’re like the ambulance company,” says Chris Holman, chief executive officer of Advanced Maintenance, which provides mobile maintenance services in North Carolina, South Carolina and Florida.
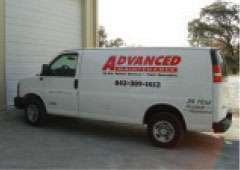
While some companies focus on roadside breakdowns alone, others deliver entire suites of services that once were confined to shop bays. Scheduled preventive maintenance programs, safety inspections and fluid changes all are perfect fits for a mobile maintenance program, says Claris Ramos-Sukkar, CEO of Texas-based On-site Fleet Services.
Some services reach even deeper into the vehicles. “Our guys will do everything up to and including clutches and transmissions,” says Paul Rygalski, president and CEO of Managed Mobile Inc. in Orange, Calif. Anything that falls outside the range of roadside offerings – whether it involves an engine rebuild, auto glass or tires – is still coordinated by the business.
Regardless of the approaches, the right combination of services can offer a perfect fit for fleets that want to reduce downtime, stop shuttling equipment to local garages or find better ways to schedule maintenance during off hours. The most effective programs adopt sophisticated business models and the equipment to support them.
Tools of the trade
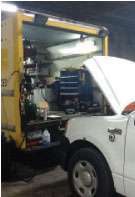
Rush Enterprises, which has commercial dealerships in 11 states, serves customers with a fleet of 150 service vehicles ranging from Class 6 Hino 268s to Peterbilt 337s, and the trucks are outfitted with everything from cranes to welders. “Basically, there’s not a job they can’t do,” says Mike Besson, vice president of service.
Managed Mobile uses two configurations of Sprinter vans. Those used by its preventive maintenance inspection teams are equipped with hose reels and reservoirs of oil, coolant, transmission fluid and hub lubricants, all delivered through digital meters. Its repair teams are equipped with vans without several of the space-hogging bulk reservoirs, but come with everything from jack stands to frame stands and the larger toolboxes needed to complete more complex jobs.
Advanced Maintenance uses 60 smaller trucks – such as ¾-ton or 1-ton vans with a variety of nameplates – since most of the company’s mobile maintenance work is conducted within a 60-mile radius of a home shop, which offers quick access to extra parts and tools that might be needed.
As important as the size of the trucks may be, the tools inside will play a large role in the ability to perform specific repairs. Air compressors are common tools, and some trucks come with parts washers or liftgates that double as working platforms.
But a close look at other equipment on these trucks quickly identifies just how extensive their maintenance capabilities can be.
A service that conducts heavy repairs literally needs to support the heavy equipment. Advanced Maintenance trucks are equipped with 20-ton pneumatic jacks, eight-to-12-ton bottle jacks and three-ton floor jacks. “Normally we’re not lifting the whole unit,” Holman says. “We’re lifting a wheel on one side at a time.”
Storage tanks also demonstrate how extensive wet service programs can be. Advanced Maintenance trucks include 55 gallons of fresh oil and a 70-gallon tank to capture waste products from oil to antifreeze. Rush Enterprises trucks come equipped with 250- to 300-gallon tanks, accounting for different grades of oil, transmission fluid, grease and waste.
Fluids potentially can spill, and that’s why Rygalski’s rolling maintenance trucks also arrive with a 100-yard roll of polyurethane absorbent mats that are pulled under trucks to catch everything from debris to the oil out of a hub. Aside from spill hazards, the mats protect customers from a yard littered with debris, grease and oil. “They don’t want their yard or loading dock to look like a service bay,” he says.
Parts smarts
Ensuring that the service vehicles have needed parts on hand beyond staple items requires close coordination between customers and shops. “The challenge goes back to when we’re doing mixed fleets,” Rygalski says.
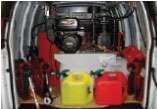
Advanced Maintenance tries to equip its trucks with enough parts to operate for two to three days without returning to the shop. Technicians supplement that through accounts with local parts suppliers.
Managed Mobile builds its maintenance programs through a detailed fleet service plan, including data about everything from a truck’s year, make, model and VIN, down to the specs for engine filters and transmissions. If someone reports that the right air bag on the third axle is leaking, the system identifies the part that needs to be ordered.
“We already know everything on the truck, so we can get the parts just-in-time and have them delivered to the jobsite,” Rygalski says. A company employee is dedicated to managing parts and procurement, looking for supplies close to the work location.
As important as these parts and tools are, mobile shops also are responsible for completing diagnostic work well beyond the reach of a home base. Luckily, many of today’s diagnostic tools are more portable thanks to ruggedized laptops. Advanced Maintenance trucks are equipped with laptops loaded with 30 different diagnostic programs from the likes of Roadranger, Allison, Detroit Diesel and brake manufacturers.
“We have the capability to read codes on every engine,” Besson says. Rush Enterprises also equips the laptops with air cards that give employees access to OEM Websites and troubleshooting trees, no matter where the service might take place.
Fleet customers often dictate how extensive the software must be. Managed Mobile trucks have Noregon Systems software loaded with Isuzu data since 10 percent of the trucks it monitors have that particular nameplate. A handful of other computers are loaded with a full suite of software covering other brands and are signed out much like a library book depending on the work that a team might face.
The human touch
As important as all the equipment, fluids and parts may be, the most important resource is a special breed of mechanics. Field service technicians typically need more diagnostic experience than their counterparts in the garage. “It’s not like the shop where there are 10 guys that can look at it and they can all help each other,” says Rick Holland, business development manager at Truck PM Plus.
Rush Enterprises puts senior Level 5 technicians on its service vehicles. “Our guys see it as a reward and a promotion to get a truck,” Besson says, noting how many have served as mentors within the traditional service bays. “This is the face of the company we’re sending out there.”
“This is the face of the company we’re sending out there.”
– Mike Besson, vice president of service, Rush enterprises
Managed Mobile starts every new employee on its preventive maintenance team. The employees then work up to an apprentice role, when they accompany another experienced mechanic for six months to a year.
As important as the ability to finish a job may be, they also need to manage any task they find and determine whether it truly can be completed in the field. “They need to know when, ‘I’m in over my head and can’t figure that out,’ ” Rygalski says.