Staying in Charge
Attention to detail will prevent no-starts, power loss
The same electrical system symptom can signal a problem in several different areas. When doing maintenance or troubleshooting, technicians always should avoid focusing on one or two components and inspect the entire system. Many assumed alternator or battery problems actually may be problems with wiring and connections.
Battery maintenance
Some experts say that alternator maintenance is really more about maintaining the batteries than the alternator itself. A good alternator will last indefinitely if it doesn’t overheat; to keep that from happening, keep the batteries working efficiently.
The alternator’s main job is to handle the vehicle’s electrical load, with 75 percent or more of its output intended for that purpose. New batteries and good wiring reduce battery charging needs and make the alternator’s life a breeze. But as batteries age or when cables and connections develop resistance, the alternator has to work harder and longer to replace what’s used for starting or supplying overnight hotel loads.
“It makes a lot more sense to replace a $4 battery cable than an $80 battery when the cable is actually
the problem.”
– Bruce Purkey,
Purkey’s Fleet Electric
“The weak link is the ‘key off’ situation,” says Randy Walker, director of North America aftermarket sales for Phillips Industries. “You draw a lot of energy out of the batteries while the alternator is idle. If you don’t have strong cables and connections, you’ll never get all that energy replaced the next day.”
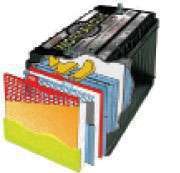
Batteries also deteriorate with wear and become inefficient, which means more power from the alternator over a longer period of time is needed to charge them. Higher loads and output mean more resistance and internal heat, so testing batteries to monitor their condition is critical.
Batteries should be load-tested at least once a year, preferably just before the weather gets cold, as a temperature drop both reduces battery output and makes the engine harder to crank. While this test will help ensure reliable starts, it’s harder to determine whether or not batteries gradually are starting to tax the alternator by losing their reserve capacity.
“Batteries that pass a load test may still have lost a significant amount of their reserve capacity,” says Bruce Purkey, president of Purkey’s Fleet Electric. To check this, establish a baseline for good batteries by testing them when new. Turn off the engine, measure battery voltage and then turn on the headlights; let the lights drain the batteries for 30 minutes, and then retest the output voltage and record the reading. After a year or two, repeat the test; if the older battery’s voltage drops more in 30 minutes than when it was new, the battery is losing reserve capacity.
While conventional batteries require regular additions of distilled water, they are easier to test. Techs should fill the cells monthly for maximum performance and life; during this service, the top surface of every battery should be wiped off to reduce the loss of charge during shutdowns. Maintenance-free batteries have an indicator that changes color when they deteriorate.
Twice a year, technicians should disconnect the battery connectors on each vehicle and use a powered brush to clean both the inside diameter of each connector and the post. Reconnect all connections securely and protect them with dielectric grease or a spray protectant. Typical soft lead connectors continually stretch; the fastening bolts should be tightened during monthly visits to the shop to ensure maximum conductivity.
In cold weather, a jumpstart may not be enough to get the truck ready for a shutdown only a few hours later. “It can take as long as two days for batteries to become fully charged in winter,” Purkey says. To bring a discharged battery to its full 12.6-volt charge, use a battery charger at a low rate for 18 to 24 hours. The alternator is not designed to power the truck under conditions that also require heavy battery charging, so an electric charger also helps lengthen alternator life.
All wired up
When truck owners believe they have a charging or battery problem, the battery cable often is the culprit. When checking batteries before cold weather, also check the cables. The Technology and Maintenance Council’s Recommended Practice 129 recommends a voltage drop of .5 volts at 500 amps of current flow.
Have a professional test each cable with a special instrument that uses electronics to measure resistance; in four seconds, a specialist using such a device can tell whether or not a cable needs to be replaced.
A technician can do this in a shop without a tester by measuring voltage at the starter positive connector while the engine is being cranked by someone else, then taking a similar measurement at the battery positive terminal; he then needs to subtract the first reading from the second.
“It makes a lot more sense to replace a $4 battery cable than an $80 battery when the cable is actually the problem,” Purkey says.
Corrosion often develops under the cable’s insulation, so it’s normally invisible. Phillips’ cables and battery jumpers have clear jackets. “This way, your technicians can see corrosion developing,” Walker says.
Current travels on the wire’s surface, and if corrosion attacks and pits the surface, the cable gets smaller rapidly. “Technicians often replace the battery when the problem is the cable,” he says. “Cables, wires and terminals are the weak links in the system.”
Technicians should check wiring quarterly or whenever they see green corrosion developing on connections. “If you can see green, there is more of it from corrosion that is still invisible,” Purkey says. Water containing road salts often wicks through the cable under the insulation, corroding the entire cable.
Starter and alternator positive and ground connections and any ground wires on the chassis need to be checked to make sure all connections are both clean and tight. Technicians also should check for cracked or frayed insulation or rubbing against other parts, repair bad wiring and protect longer runs with ties to keep them away from surrounding surfaces.