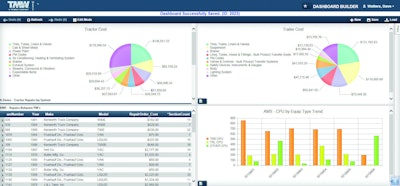
It was once common practice for motor carriers to purchase stand-alone software systems for their shops to keep track of vehicle maintenance schedules, inventory, repairs and all of the associated costs. Any communications that took place between the office and shop was done in person or by sending e-mails or files back and forth.
The current lineup of asset maintenance management systems operate much differently. They now come with ready-made integrations with the office.
An early sign of the growing demand for deeper integration was the acquisition of TMT Software by TMW Systems in 2007. TMW has since built a number of standard integrations between its TMT Fleet Maintenance product and its transportation management software (TMS) platforms which include TMW Suite, TruckMate and Innovative.
Preventive maintenance notifications now automatically appear in the load planning screens. When updating the unit and driver data in one system, the other is automatically updated. Status is also shared instantly: when a repair order is opened in TMT, the status changes in the TMS to “In Shop,” for example.
One advantage of sharing master files is that maintenance costs can be reported by the driver or operator of an asset. And when accessories such as mobile communication devices, chains, straps, tarps, binders, load locks, bulk hoses and fittings are assigned to an asset in the TMT system, these accessories are visible in the TMS to use as a possible requirement when dispatchers are making load assignments.
Another point of integration with the office is through mobile communications and telematics systems. Mileages, diagnostic trouble codes and more are being used to automatically update maintenance software and trigger work orders for assets.
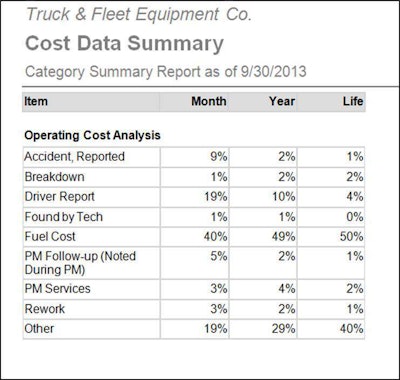
Dossier Systems has developed a close integration between its fleet maintenance software and the LoadMaster Enterprise (LME) platform by McLeod Software. Odometer readings from telematics devices flow through LME and automatically update Dossier software to schedule preventive maintenance work on time, says Bob Hausler, vice president of marketing and technology for Dossier Systems.
When Dossier determines that a PM is due it sends a notification to LME. When a unit is in the shop, Dossier pushes status updates to the dispatch and planning screens to reflect that the asset is unavailable. When maintenance is complete, LME shows the truck is ready to go back into service.
Drivers can send form messages from their in-cab devices to report issues and request repairs. The message triggers and automatic creation of a work pending order in Dossier without the need to double-enter the data, he says.
The Dossier-LME Integration also includes financial transactions for maintenance activity, inventory, and parts and services purchasing.
“The interface is designed such that each system performs the functions that are appropriate and efficient and then applicable data is transferred,” he says.
One thing that fleet maintenance software does not do is supply repair information. Rather than have technicians spend time searching online and keeping repair information up to date, Mitchell 1 has all of the repair information, labor estimates and diagnostic trouble code procedures for medium and heavy trucks in one place.
Its web-based TruckSeries suite integrates with a number of asset management systems to provide convenient access to repair information by make, model and year of vehicle, says Scott DeGiorgio, general manager.
If technicians can’t find the information they are looking for, the software allows users to ask questions or call a helpline to have an ASCE certified technician on staff provide the necessary repair information, he says.
Since the software is online, Mitchell 1 knows what technicians are searching for and can create shortcuts to common repair items based on search volume, he adds. The company has more than 20,000 users of the TruckSeries software, he says.
Besides gaining efficiencies by synchronizing the flow of information between software systems in the office and shop, companies are able to make better decisions since everyone is looking at the same data.