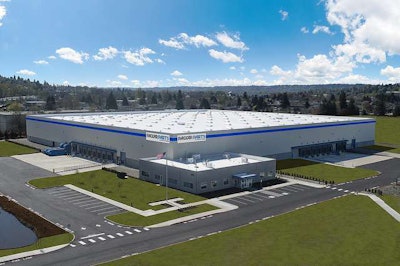
Paccar Parts has officially opened its new $32 million, state-of-the-art distribution center in Renton, Wash. Servicing dealers in the Northwestern U.S. and Western Canada, the new 160,000 sq.-ft. parts distribution center (PDC) is almost three times the capacity of its predecessor built in 1973.
David Danforth, Paccar Parts general manager, says the investment that more than doubles the square footage, demonstrates the company’s “commitment to being a world-class leader in aftermarket parts distribution.”
The Renton PDC represents the new standard for Paccar Parts distribution centers by incorporating strategic design, innovative technology and sustainability. With a 15,000 sq.-ft. small-parts mezzanine and state-of-the-art equipment such as stock-picking equipment with built-in weight scales and a custom parcel conveyor, the facility provides operational efficiency and a 125 percent increase in capacity of parts, enabling it to store over 39,000 different parts.
Energy efficient systems including LED lighting and daylight harvesting contribute to meeting the environmental goals of Paccar Parts, illustrating the company’s commitment to business sustainability and making a positive impact in the world.
“We designed every aspect of the PDC to create a logical efficient work flow. From the ‘pick path’ to the unique stocking fixtures, efficiency and accuracy measures have been taken at every point to streamline customer orders and ensure quick turnaround times,” says Laura Bloch, Paccar Parts assistant general manager – operations.
The facility also includes a 50-person training room and an interactive “Paccar Parts Experience” that demonstrates Paccar Parts world-class distribution network, and industry-leading products and services to visitors. Featuring a 3-D model of the distribution center, the Paccar Parts Experience demonstrates the efficiencies and innovative technologies that provide superior levels of customer service, the company sa