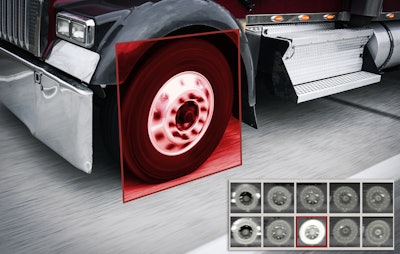
“Smart” weigh stations are using new technologies to make sure officers spend their time looking at the trucks that need to be inspected.
“These technology-filled stations feature so many new advancements, including vehicle waveform identification and advanced thermal imaging systems – it’s really something,” said Brian Mofford, vice president of Drivewyze. “Much of this technology was developed and patented by our sister company, Intelligent Imaging Systems (IIS).”
Mofford shared four technologies that are prevalent at modern weight stations:
1. Thermal imaging
Many inspection station systems now use thermal inspection technology, which can heat-sense thermal signatures associated with unsafe and defective equipment such as inoperative brakes, failed bearings and under-inflated or damaged tires.
“Advanced image processing, coupled with decision-making algorithms within screening software, searches and flags possible defects for a more thorough inspection,” explained Mofford. “It’s a huge time saver for law enforcement and lets inspectors focus more of their time on the trucks that truly need checking.”
2. Mobile scanning
Automated Readers are other tools used to collect and process information in real time before a vehicle has arrived at the inspection site. Even when a truck is moving at highway speed, high definition (strobe) cameras are able to capture and scan its DOT and license plate numbers, CVSA sticker and Hazmat Placard, and then access information from over 90 government databases to provide enforcement officers with an instant, detailed description of the vehicle and carrier.
There’s no saying, “It wasn’t me,” said Mofford. “As you approach the scales, overview cameras snap a photo of your vehicle, so that officers can match it with the information accessed by the Automated Readers, mainly the license plate and USDOT Number.”
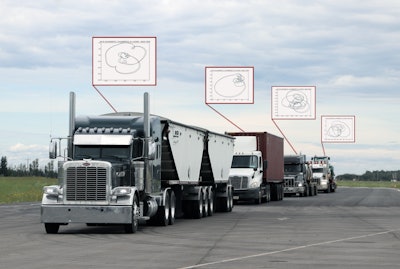
Mofford notes that a system from IIS called Mobile Van Smart Roadside combines sensing and detection technologies in to identify potential safety and security violations at sites where fixed stations are impractical or cost prohibitive.
3. Vehicle signatures
Weigh-In Motion (WIM) technology is advancing to improve the inspection process.
WIM scales are typically embedded in the roadway about a half-mile ahead of the inspection station.
When a weight is taken, electronic screening and bypass service providers like Drivewyze and PrePass associate the weight taken with the correct truck and provide the scale house the information, explained Mofford.
“If you’re not hooked up with Drivewyze or your truck isn’t equipped with a transponder, don’t think you can roll on by undetected — there are other applications out there that allow states to monitor WIM without the need for a transponder or the Drivewyze service,” he said.
An electronic screening platform can gather vehicle data via vehicle waveform identification (VWI). “This uses magnetometers mounted on overhead signs to identify vehicles by measuring the truck and trailer’s magnetic ‘signature,’” said Mofford. “Each truck and trailer, even those spec’d identically, generate a unique magnetic footprint. While the signature changes over time, VWI can still recognize the readings and assign them to the corresponding trucks and trailers with a high degree of accuracy.”
4. Officer discretion
Pull-in rates and guidelines vary since they are generally set up by the individual states and jurisdictions.
“Some jurisdictions need probable cause to pull drivers in and some can stop a truck ‘just because,’” he said. “Officers are generally given of a lot of discretion, and some have their own system for selecting trucks for inspection — it could be as simple as picking every fifth or tenth truck.”
Meeting inspection quotas is another factor.
“In almost every jurisdiction, each inspector is required to perform a specific number of inspections,” said Mofford. “By regulation, each officer is required to do a certain number of level I inspections to maintain proficiency. In some states, full-time officers are mandated to conduct as many as 600 inspections a year.”
Training drivers for inspections
Inviting law enforcement to perform mock inspections and training for drivers and managers at fleet headquarters or maintenance facilities can be extremely beneficial, says Lee Sarratt, J.B. Hunt Transport, Inc., senior director of safety.
“Our drivers and managers learn a lot from the training sessions and mock inspections we host,” said Sarratt. “After meeting with law enforcement, our drivers have a better understanding of what law enforcement are looking for during inspections and how to properly interact with them. These officers are just trying to make the roads safer for everyone, and our drivers know it’s important to cooperate.”
What’s in it for the driver to sit in on these training and mock inspection sessions?
“At J.B. Hunt, we reward our drivers for 100 percent clean inspections,” said Sarratt. “For us, it shows that they are putting in the effort to be safe out on the roads and improve our image as a safe fleet. We also reward our drivers who consistently receive clean inspections as well. It shows us that the information they’re learning through the training and inspections makes a difference.”