Transparent maintenance
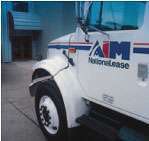
When vehicle repairs get delayed or missed altogether, drivers, dispatchers and shop supervisors start to point fingers. The driver says he wrote up the problem two weeks ago. The dispatcher says he forwarded all the paperwork to maintenance. The shop supervisor says he never saw the write-ups.
Tracking anything on paper can be a hassle, especially when multiple personnel and departments are involved. Such is the case with driver vehicle condition reports (DVCRs) and pre-trip inspections.
In late 2002, executives of Aim NationaLease asked the company’s information technology department to take the hassle out of tracking DVCRs. Aim NationaLease has 40 maintenance facilities across the nation that service two company divisions: a leasing and rental fleet of 6,000 trucks, and a 400-truck Dedicated Logistics fleet.
The IT department previously had handled much larger and more complex projects, says John Reed, vice president of IT and chief information officer. In 1997, Aim NationaLease developed a custom dispatching and freight bill auditing system for its Dedicated Logistics customers. The LogistixPro software has the flexibility to meet the needs of all types of operations, from steel hauling to refrigerated foods, Reed says.
LogistixPro can take orders from a customer, create routes and dispatch drivers. The software calculates driver payroll for fleet drivers and integrates with asset-tracking systems to enable real-time mapping. LogistixPro also has carrier selection tools for nonfleet loads and tracks carrier performance in scorecards for negotiations.
Solving the DVCR problem was a quick fix for the IT department. Drawing on this base of experience, Aim’s programmers created an electronic method for drivers, dispatchers and leasing customers to write up vehicle conditions and communicate seamlessly with shop supervisors. The system also builds historical records of each write-up from initiation to completion.
“With this tool, there is only one version of the truth.”
– John Reed, vice president of IT and CIO
“Our electronic driver vehicle condition reports were first conceived, as most good ideas are, out of necessity,” Reed says. “Using the eDVCR not only eliminates the issue of lost DVCRs, it also adds the ability to track them, alert people of their existence, age them and historically report on them.”
Drivers and dispatchers for Aim’s dedicated fleet and leasing customers fill out DVCRs online. After submitting the form, the system’s original design would send eDVCRs to shop supervisors via e-mail.
“It gives accountability across the board,” Reed says. “Maintenance is not missing anything because everything is recorded and time-stamped.”
As maintenance completes the work, the system automatically sends an e-mail notification to customers and other interested parties. All information is available online for both real-time and historical reporting. “This allows our customers to review eDVCR history when they feel that something has been written up repeatedly,” Reed says.
Programmers designed eDVCR to quickly identify systems and components on the vehicle needing repair by using the Vehicle Maintenance Reporting Standards (VMRS) established by the Technology and Maintenance Council of the American Trucking Associations. The numerical codes of VMRS are invisible to drivers when filling out a form. Drivers use pull-down menus to select from a list of predefined conditions, and they also can enter text to describe the problem in more detail.
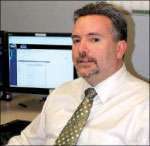
To make it easy and convenient for drivers to submit eDVCRs, Aim NationaLease has added kiosks at its maintenance facilities. Some of the company’s lease customers also have added kiosks in their offices in locations where drivers normally would submit paper DVCRs.
Some of the company’s lease customers also are using the eDVCR system for drivers to document pre-trip inspections. The system can be loaded onto various types of onboard and handheld computers so drivers can fill out reports and pre-trip inspections from anywhere, Reed says.
The latest upgrade
Aim NationaLease originally set up the eDVCR system to communicate with shop supervisors via e-mail. The drawback of this approach was that technicians were using a browser to access the eDVCR system and re-entering information into their fleet maintenance management system.
About six months ago, Aim NationaLease updated the eDVCR system so that write-ups now post directly to the fleet maintenance management system as a “Work Roster” entry.
“We make it as seamless as possible when they write it up,” Reed says. With the write-ups being posted automatically in the maintenance software, a technician converts a “Work Roster” into a work order when he starts the repair. The eDVCR system captures all details entered into the work order, such as any parts changed or notes added by a technician.
When a technician closes the work order, the system e-mails the repair details to the driver, dispatcher and other personnel included in the distribution list for the particular eDVCR.
Monitoring breakdowns
Aim NationaLease now is working on a project to bring the same type of visibility and accountability it has created through its eDVCR system to customers that use its central breakdown service called Road Rescue.
In 2003, the company created a software system called RescuePro to help manage equipment breakdowns. When a driver calls into Road Rescue, the company uses RescuePro to document the entire process. The person who takes the call asks the driver for certain information, such as his name, unit number and location of next stop, and any other requirements the customer may have.
Meanwhile, the company’s maintenance software system captures details of the work performed on the vehicle, such as the assigned vendor and estimated repair time.
Now, instead of calling Road Rescue, a dispatcher for a dedicated fleet can login and see the same information he could get if he were to call, including when and where the breakdown occurred and the estimated time of repair.
“We code it in such a way that it becomes immediately available to the end user,” Reed says.
The company currently is working on more ways to automate communications with customers when a breakdown occurs, Reed says. If a breakdown occurs, multiple people may need to be involved as time passes. If the repair time is less than one hour, only the dispatcher may need to know.
If the repair time escalates to two hours, the customer service department or even the company’s president might have to get involved. As the breakdown situation passes these different milestones, RescuePro will send automatic updates to the proper chain of command, Reed says.
In more ways than one, Aim NationaLease continues to use technology to bring full transparency to its equipment leasing and Dedicated Logistics customers, as well as accountability to its maintenance operations. “If we are not doing a good job on the repair, it will show, and our shops know it,” Reed says. “With this tool, there is only one version of the truth, and it’s available for our customers to look at whenever they like.”
Innovators profiles carriers and fleets that have found innovative ways to overcome trucking’s challenges.
If you know a carrier that has displayed innovation, contact Avery Vise at [email protected] or 800-633-5953.