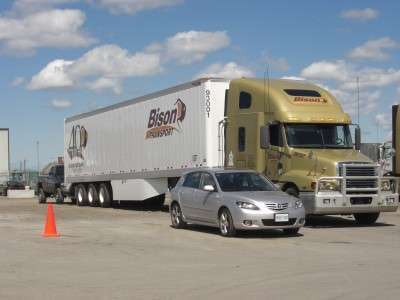
In 2006, Bison Transport won its first of three consecutive grand prizes in the Truckload Carriers Association’s National Fleet Safety Awards. One of the catalysts of Bison’s continued success in safety was a 2003 decision to purchase and deploy stationary and full-motion simulators, which it incorporated into the driver training and development program it calls Tatonka. Today, Bison executives are offering the success of its safety program and high-tech training tools to more drivers than just those on its payroll.
Bison launched a safety campaign called “You’re Safe With Me” in 2006 to celebrate the company’s people, culture and values. As part of this year’s campaign, the Winnipeg, Manitoba-based company added a new course to its Tatonka program called “Let’s Bring Safety Home.” The course grew out of an idea from an employee in Toronto. While teaching his teenage daughter how to drive, the employee expressed his concern that not enough motorists know how to operate safely around trucks. So Bison executives decided to offer a two-hour safety training course to employees’ families and friends. As part of the course, students spend time in a simulator.
Garth Pitzel, director of safety and driver development, says the advantage of using simulation is for students to see the consequences of their driving decisions. An instructor can use a separate “rabbit station” to take control of a passenger vehicle in a simulated environment and move into a truck’s blind spot or move out in front of the tractor and slam on the brakes.
The first three training courses were held on separate days in late June and early July at three of Bison’s terminals: Winnipeg, Mississauga and Calgary. Once the company announced the dates for the course, classes filled up within a week, and the company already is planning additional training events to meet growing demand, Pitzel says. Management also is considering ways to expand the course to a wider audience by offering it to groups such as customers and insurance companies, he says.
Driver development
Besides using simulators to train drivers, the Tatonka program uses high-tech tools to specify the appropriate training based on individual driver needs.
The trucking industry traditionally has used a “paintbrush” approach for safety and training, Pitzel says. Companies might decide to hold quarterly safety meetings where they offer the same message or training to drivers. Smaller fleets periodically may ride along with drivers to provide one-on-one assessments and training, but instructors cannot cover all types of circumstances a driver may encounter.
Driver training is most effective when you can apply the right amount of time, concepts and learning techniques according to the needs of individual drivers, Pitzel says. To identify those needs and specify the appropriate individual training, Bison developed a proprietary Driver Information Management System (DIMS), which assigns risk based on data collected on each driver for accidents, mileage, violations, speeding, following distance and other data points.
Bison uses DIMS to continually refine its driver development cycle. The company requires all drivers to take a set of simulation courses immediately after driver orientation, followed by new courses every three months for the first year. The order of the training courses is determined by analyzing the type of incidents that happen according to drivers’ work experience. For example, the company used to require drivers to take a backing course at the three-month stage; today, this course is required at orientation.
“We were finding that most maneuvering accidents were happening in the first six months of drivers’ careers at Bison,” Pitzel says. “We changed the cycle to have (the backing course) right up front. We did that and reduced backing accidents by 28 percent.”
Targeting needs
In addition to refining its driver development cycle, Bison uses DIMS to identify which drivers to bring in for additional training and meetings. “We’ve been able to design a program that gives a three-year snapshot of a driver’s risk level,” Pitzel says. The program assigns a weight factor to each type of incident based on the severity of risk.
To identify the risk of each type of incident, Bison uses the “Predicting Truck Crash Involvement” study by the American Transportation Research Institute of the American Trucking Associations. The study uses truck crash data to show the probability of future truck accidents based on specific types of driving behaviors and events such as violations, convictions and past crashes.
When an incident such as speeding occurs, Bison’s safety department reviews the incident and looks at how its DIMS classifies the driver – low, medium, high or extreme risk. The type of training a driver receives depends on his risk level. Bison has developed some online courses for low-risk drivers, but drivers in the medium, high and extreme range have to take courses that include simulation. “We have to train them differently,” Pitzel says. “You have to spend time and resources on people that need it.”
In the past year, Bison has reduced the number of drivers in the high-risk category by 21 percent, Pitzel says; today, 85 percent of drivers are low risk. Perhaps just as important, the company’s driver turnover rate is 20 percent – low for a carrier that employs more than 1,400 drivers. Its low driver turnover can be attributed partly to its success in changing the behavior of drivers who otherwise would be terminated. “Our goal is not to terminate (high-risk drivers), but to change their behavior,” Pitzel says.
The Tatonka driver development program is just one of many tools the company uses to improve safety and reinforce a safe driving mindset. All company equipment includes roll stability control systems and automated transmissions to allow drivers more freedom to concentrate on space management. Since deploying automated transmissions, the number of incidents and accidents from drivers making left- and right-hand turns has been reduced significantly.
“When we look at drivers, what we’ve really created is a safety toolbox,” Pitzel says. “We give them the best equipment out there and the safest. We train them on it, and then we have a solid training program to give them the necessary skills to make it home safely.”
Just as important, Pitzel says, is that Bison’s operations team gives drivers the sole authority for when to drive. “The only one who decides if they can drive is the one behind the wheel,” Pitzel says. “That load is late if the driver can’t do it, or we have to find another way to get it there. Our culture supports all aspects of safety.”