Step-by-step transformation
LTL carrier removes waste from preventive maintenance practices
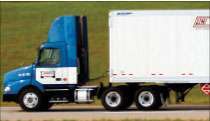
Identifying and eliminating waste is a cornerstone of Taiichi Ohno’s Toyota Production System, the processing method developed by the Japanese automobile executive that allowed the company to compete on a global scale and emerge as the world’s largest car manufacturer. Forward-thinking companies the world over have adapted Ohno’s lean manufacturing principles to their own work environments. One of the seven wastes – or muda in Japanese – found in today’s production environments involves the waste of motion: people or equipment moving more than necessary to complete a task.
It was in that spirit that AAA Cooper Transportation (ACT) decided to streamline the preventive maintenance practices for the company’s 41 house shops at terminals across the southern states and as far away as Chicago and Minneapolis. The Dothan, Ala.-based less-than-truckload carrier for dedicated services, port services and fleet maintenance repairs throughout the Southeast hired Terry Clouser as its director of maintenance. Clouser brought with him 27 years of automotive experience for UPS, the last two years of which he served on the company’s work management and time study team.
While Clouser notes there was nothing wrong with ACT’s existing preventive maintenance practices, he realized the potential to improve shop efficiency and add to the company’s bottom line. Clouser specifically cited a lack of standardization or procedures for how preventive maintenance was performed systemwide.
“If I walked into our shop in Dallas, the technician might start preventive maintenance at the left front of the cab,” Clouser says. “In Atlanta, they might start by changing the oil or adjusting the brakes. Nothing was centralized or had written procedures in place that would have the preventive maintenance performed the same way, the same time at every location on each piece of equipment.”
Time studies
Clouser’s team of four field maintenance trainers set out to establish a standardized preventive maintenance protocol to maintain each type of equipment owned. Company mechanics came in to help develop the system and perform time studies. A main focus of the team was to reduce wasted motion and lessen the amount of time it takes a technician to perform an inspection, including the number of times he had to climb in and out of the cab or crawl underneath the truck.
“We listed all the wear items, looked at our parts usage and what parts we were changing the most often and made sure those were on the PM checklist,” Clouser says. ACT also incorporated the annual inspection into the preventive maintenance standard to eliminate the need to bring a truck back in shortly after a PM inspection had been performed, thereby eliminating duplication of work. “Not necessarily would you update the sticker every PM, but everything we do on a PM qualifies for an annual inspection.”
The new written preventive maintenance procedure that resulted from the time study provides a systematic approach to inspecting, repairing and maintaining the company’s fleet of 2,000 Volvo power units. It complies with state and federal Department of Transportation regulations, and allowed ACT’s maintenance division to adjust the service intervals to match Volvo’s warranty criteria. As engine and truck technology evolves, ACT’s preventive maintenance program will be adapted to include items such as diesel particulate filters and urea tanks.
“It’s a change in mindset and a change in culture, and it was a new technology.”
– Terry Clouser, director of maintenance
In addition to developing a written procedure, ACT revamped its maintenance facilities to better serve its technicians. Some modifications were minor, such as adding convex mirrors so the technician can inspect lights and turn signals while driving the truck into the bay without having to leave the cab, and bolting six-inch risers to the floor so the truck doesn’t need to be jacked for the mechanic to get underneath it. Others were major, including moving tires and parts rooms to a central location, installing overhead oil lines and air hoses in the bays and installing new lighting. ACT also added multiple work stations around the shop to eliminate several technicians waiting in line to log on and update time cards or close out work orders.
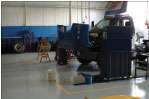
“Our mechanics benefit from not having to climb in and out of the cab as many times,” says Clouser, who notes that under the current system they only have to do it twice during a preventive maintenance inspection. “They don’t have as far to carry their waste oil or get their parts. Safety has also improved greatly because there’s less repetitive motion and no air lines or light cords lying around.”
Overall, the new preventive maintenance program reduced inspection time by 18 percent, down to 2.3 hours. Now the backbone of the company’s maintenance program, the new process has netted savings of nearly 2 cents per mile for the company, Clouser says.
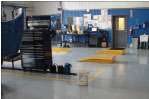
“If we can identify the problems before the truck gets out on the road, we can save a tow bill, driver downtime, freight not meeting a scheduled delivery time,” he says. “That savings is a combination of better parts and materials, better lubricants, quality training and preventive maintenance education.”
Proving ground
The biggest challenge associated with any procedural change is establishing total organizational buy-in, from company leaders to the technicians in the shop. “When the new kid on the block comes in and says, ‘We’re going to do it this way,’ if you go in and try to force-feed them and tell them they’re doing it all wrong, it won’t succeed,” Clouser says. “As long as you explain to them why we’re going to change it and show them what we are going to do and let them know how they will benefit, it’s an easier sell.”
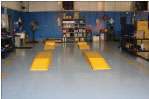
Once Clouser’s team of trainers realized the benefits of the process and had proven it to themselves, the training process continued in the field, where the average ACT technician has tenure of 15 years. The team trained each shop several times on the new preventive maintenance method before it took hold.
“They’re not going to pick it up the first time we show them – they are set in their ways after all these years,” Clouser says. “It’s a change in mindset and a change in culture, and it was a new technology. Now they’re all receptive to it and wouldn’t go back to doing it any other way.” n
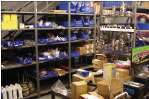
Innovators profiles carriers and fleets that have found innovative ways to overcome trucking’s challenges.
If you know a carrier that has displayed innovation, contact Avery Vise at [email protected] or 800-633-5953.