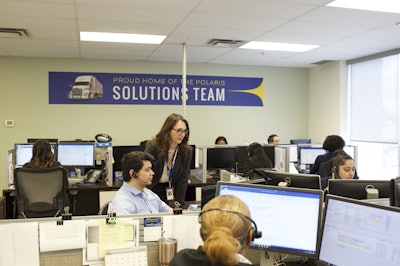
The RPA platform has reduced the cost per order for PTG and brought visibility to work in process (WIP). Workers can see the status of all orders at any time of day. Before the technology, “we had no clue what orders were ahead or behind schedule,” Brajkovich says.
The automated bots have enabled PTG to go from 22 full-and part-time workers – touching every order during the lifecycle, from order entry through operations – to 15. Most of the job reductions were temporary staffers, he says.
Today, about 80% of the orders and documents that PTG receives from customers are automatically processed straight through — sending customs invoices to border agencies to obtain clearance.
The company is able to clear WIP in the system up to four hours earlier every day and process orders at an accuracy rate of 99.9%. As a result, freight is getting cleared through customs faster, and “at the end of the day, we are not holding up trucks or shipments,” Brajkovich says.
Lucy Lewis, director of customer care, has seen the transformation in order entry. Prior to using the RPA technology, orders came in by phone, email or electronic data interchange (EDI) and were funneled to a single office worker who printed them out and distributed them to a team for manual entry into the company’s enterprise resource planning (ERP) system.
Workers had to validate the items they would input, such as addresses, cities and postal codes. Most orders arrive between 11 a.m. and 2 p.m., and during that period, the order entry team “had a huge bottleneck,” Lewis says. “We had to get assistance from other departments during the peak time to help us get through the backlog.”
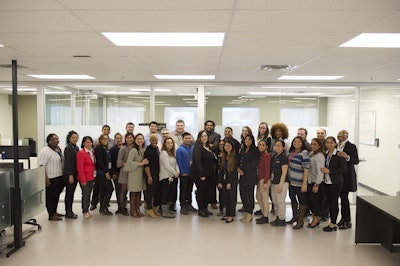
Today, the bots do the validation and data entry process for orders as quickly as they arrive from email, the website, EDI or application programming interfaces (APIs). Rather than process data, the order entry team now is focused on quality and managing exceptions, Lewis says.
The bots also feed orders directly into the ERP system for the operations team to start planning pickups. Overall, Lewis says, workers are more motivated and engaged because the technology is freeing them from data entry and other manual tasks, allowing them to focus on customer service and improving their skillsets.
“They feel like they are adding value and feel a part of something much bigger than just order entry,” she says. “They feel like they are part of the entire process from a customer perspective.”
About the award
Commercial Carrier Journal’s editors recognize innovators throughout the year and select one for special recognition as the CCJ Innovator of the Year. Innovators considered for the current award were those recognized in the magazine in 2019.
Innovation in any aspect of the operation is eligible for recognition. To qualify, the carrier must operate at least 10 power units in Classes 3-8 and maintain a satisfactory safety rating, if rated. Selection of innovators for recognition is at the sole discretion of CCJ’s editorial staff.
This year’s award was announced and presented at the CCJ Innovators Summit, a networking event for current and prior-year CCJ Innovators held Feb. 5-7 in Key Largo, Fla. Representatives of the innovative trucking operations updated one another on their initiatives.
The CCJ Innovators program is sponsored by Freightliner Trucks, Omnitracs and Shell Lubricants. For more information on the program and links to previously recognized CCJ Innovators or to fill out the online nomination form, go to CCJInnovators.com, or contact Jason Cannon, CCJ editor, at 205-248-1175.