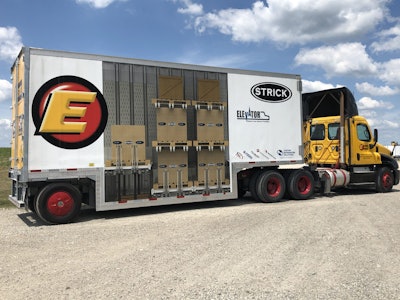
CCJ Innovators profiles carriers and fleets that have found innovative ways to overcome trucking’s challenges. If you know a carrier that has displayed innovation, contact CCJ Editor Jason Cannon at [email protected] or 800-633-5953.
Hearing the ghost of disgraced Chicago White Sox outfielder “Shoeless” Joe Jackson hint, “If you build it, they will come,” fictional Iowa farmer Ray Kinsella defied all naysayers and constructed a baseball diamond in the middle of his cornfield.

Mike Palmer, vice president of fleet services for Estes Express Lines (CCJ Top 250, No. 12), must have been within earshot.
Estes, with a fleet of more than 7,000 tractors and nearly 29,000 trailers, is among the nation’s largest less-than-truckload and truckload carriers. Size and scale matter in the trucking business, but the Richmond, Virginia-based carrier remained flummoxed by the amount of “empty space underneath the trailer,” Palmer said.
Management saw the opportunity cost of not being able to pack in more cargo. “We always cube-out before we weigh-out,” he said.
Three years ago, Palmer was cruising the 2017 North American Commercial Vehicle (NACV) tradeshow floor with Justin Bell, vice president of engineering for Strick Trailers. Palmer was venting his frustrations with the additional tractors needed to haul cargo that otherwise could have fit in the dead space between the trailer floor and the road surface, which led to his “Field of Dreams” moment.
If he built it – or at least prodded the design of it – more pallets would come.
“We were just talking about how the space between the landing gear and the axle could be used,” Bell said. “It just kind of blossomed from there.”
Flexibility without compromise
The list of wants and needs was long, but Bell noted that Palmer mentioned several critical items that were required. “You can’t go super-low on the belly, because you’ll create ground interference,” he said. “You have to be able to drive a forklift over [the belly], and you have to be able to use it as a standard trailer, otherwise it’s going to be too niche.”
Palmer worked with Bell and Strick Trailers to develop an elevator system for the Monroe, Indiana-based manufacturer’s 28-foot pup trailers, allowing them to hold six additional pallets per trailer in an additional 104-cubic-foot area that previously was occupied by wind and road noise underneath the trailer floor.
With the platforms locked in their standard position, the interior floor-to-ceiling height is 9 feet, 2 inches. Lowering the platforms creates an additional 30 inches of vertical space on each platform.
The Elevator van trailer itself is 99 inches wide from post face to post face, and the lining is installed vertically to use logistics posts for cargo control. The exterior is just over 102 inches wide and a standard 13 feet, 6 inches tall. The trailer boasts a 40,000-pound gross vehicle weight rating and 2,269 cubic feet of volume.
The elevator system uses three linear-actuated platforms that drop the floor segments between the truck and trailer axles from the standard floor level, allowing the carrier to triple-stack pallets on those three segments and increase capacity by 33% thanks to the use of swing doors (versus rollup) with additional load bars at the rear.
“We made [the rear door] a swing door so we could we stack all the way to the back,” Palmer said. “We can get six pallets in the belly, 12 on the floor and 12 more on top.”
Unlike other variable bottom trailers, a forklift can drive over Estes’ adjustable sections to load and unload the front.
When pallets are placed on the 93-by-50-inch aluminum elevator sections, they can be lowered to allow for additional pallets to be stacked on top. A 24-volt control panel is mounted on the interior sidewall and controls individual platform motion with individual lighted pushbuttons. An integrated sidewall multi-light warning system indicates a stowed or unstowed platform position, as well as platform-in-motion scenarios.
Rear internal amber strobe lights operate when the elevator system is powered and the rear motion sensor is activated, cautioning those entering or working around the trailer of its unique attributes.
The platforms are located above the drop section with 1 3/8-inch extruded aluminum knurled flooring and recessed floorboard joints atop each platform. An integrated latch system provides each platform with standard dynamic and static floor ratings when stowed/latched. Each platform features 5,000 pounds of lifting/load capacity in its unstowed position.
The Elevator power system is designed to handle dual- and triple-trailer configurations. A standard 200-watt solar-charging system manages power levels and allows loading and unloading without being tethered to the tractor. The onboard 12- to 24-volt power converter reduces the total current required for lifting loaded platforms, and an interior roof-mounted passive infrared (PIR) motion sensor with a 15-minute timer function powers down the system when not in use.
The coronavirus pandemic delayed Estes’ initial planned rollout, but Palmer expected to have the company’s first two units on the highway by Labor Day and another 200 waiting in the wings. The pup trailers will be deployed on long-haul runs.
Bell noted the seamless fixed trailer belly offers a measure of aerodynamic gain, even though it takes up the space that otherwise would be occupied by a skirt.
“The aerodynamic advantage is equal to or better than a skirt,” he said. “A skirt has inherent inefficiencies. How many times have you gone down the interstate and seen a trailer skirt flapping in the wind? That’s creating harmonics and disrupting airflow.”
Bell said that by heaping on six additional pallets, carriers could eliminate every fourth trailer and cut transportation costs and their carbon footprint.
“No skirt I’ve ever seen has been able to carry any kind of freight,” he joked, adding the company also is working with Flow Below to close the gap between the rear of the belly and the trailer’s tires.
Oversized liftgates for oversized cargo
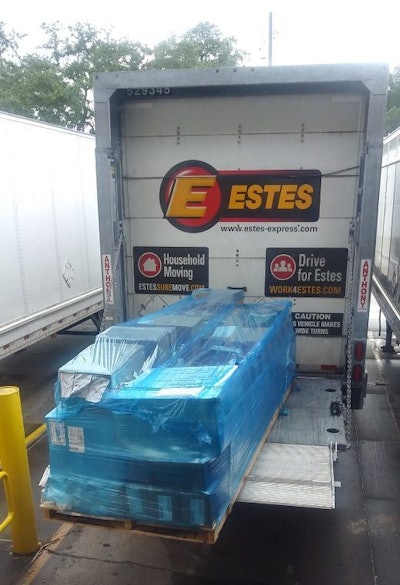
The space beneath the trailer wasn’t the only area under Palmer’s review. The delivery of bulky items also had become an increasing challenge for Estes.
A driver mentioned to Palmer that his 60-inch tuck-away liftgate wasn’t up to the challenge of hauling large items such as swing sets and hot tubs.
“[The drivers] were having to turn it sideways to unload,” he said. “Imagine coming out with a 6- to 8-foot skid and then turning it sideways just to get it down on the ground.”
Liftgates can be spec’d in a variety of sizes, but the larger gates can limit driver access to the rear door, and Palmer said the company’s drivers had long derided railgates.
“Railgates had not been popular, because you have to raise and lower it every stop,” he said.
Estes and Palmer worked with Anthony Liftgates to develop a tri-fold platform that opens up to an 89-by-102-inch load area with a hydraulic open/close function, and it also has a spring-assisted third section. The platform is rated up to 5,500 pounds and can be stowed at bed height or in a fully-raised position during transit.
“It’s a railgate, but it stows beneath the door,” Palmer said. “If I’m delivering residential, I can pull it out and use it, but if I’m bumping a dock, I don’t have to worry about getting out and taking it down.”
Estes installed the larger liftgates on 10 trailers this spring, and Palmer said drivers “haven’t had to turn anything sideways yet.”