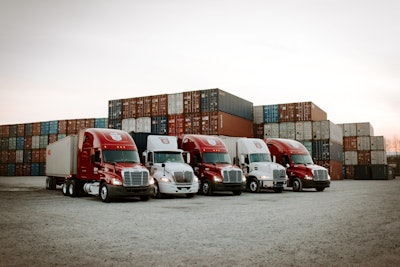
CCJ Innovators profiles carriers and fleets that have found innovative ways to overcome trucking’s challenges. If you know a carrier that has displayed innovation, contact CCJ Chief Editor Jason Cannon at [email protected] or 800-633-5953.
The infamous congestion that began last year at the ports of Los Angeles and Long Beach laid bare the supply chain inefficiencies and system-wide turmoil that exist throughout the nation’s marine and inland terminal network.
From a trucking perspective, backups can cause hours of detention time, fewer turns per day and lost revenue. The traditional practice of a drayage truck waiting as a crane sorts through stacks of containers to get a specific load is only exacerbated during times of high volume when containers are often stacked eight high, resulting in more container moves to reach the prescribed one.
The concept of peel piles was introduced in container port operations less than a decade ago to help alleviate wasted time and improve truck utilization. In a peel pile operation, containers from a single shipper or importer are grouped into stacks (or piles), and truck operators simply receive the container on top of the stack and take it to a common inland distribution center for further routing. This process eliminates the need for terminal cranes to move multiple containers just to load one truck.
Peel piles can greatly improve productivity for drayage operations. According to Mason George, IMC Companies’ president of national accounts, peel piles can reduce driver detention by three times and cut dwell time – the time a container sits at a port terminal – from nine days to an average of three days. A driver might make five turns instead of two at the Port of Los Angeles, and seven turns instead of three at an inland terminal like Memphis or Chicago, George said.
The main drawback to peel piles is their limited scope. Only the nation’s largest beneficial cargo owners – think Amazon, Walmart, Home Depot, etc. – can create enough container volume at a port terminal to make peel piles a viable alternative. Containers for smaller volume importers are relegated to the traditional and inefficient terminal operations of the past.
Building a smarter stack
IMC, the nation’s largest marine drayage company and operating in nearly 50 inland and marine locations, wanted to bring the peel pile concept to more of its customers, with some added efficiencies for its 2,200 drivers.
“We use our scale and our density with our customers to say, ‘We don't need one customer. We don't need one destination. We can do this across the board for all destinations, all customers, in all the terminals that we do business for,’” said George.
In 2020, Collierville, Tennessee-based IMC began development of a proprietary version of the peel pile concept that it now markets as SmartStacks. As containers arrive at a terminal, those for participating IMC customers are grouped into separate SmartStacks piles for priority service. Unlike a regular peel pile, in which all containers are typically hauled to a single location, containers in a SmartStacks pile could be destined for any number of inland terminal locations.
Using a proprietary app developed by IMC, once the driver receives the container in the terminal, they instantly see the container’s destination and can deliver the load to the final location.
Once a driver receives a container from a SmartStacks pile, they have the option of delivering it to its destination or routing it to a closer terminal if they are low on hours.IMC Companies
“If a driver says, ‘Hey I only have an hour left in my day and you're trying to send me on a five-hour trip,’ how do we account for that?” said George. “We have what's called a parachute option, and they're able to take that box, hit a button [on the app], and it routes them to our yard that's closer.”
The SmartStacks system has yielded impressive results for both customers and IMC drivers.
“In a place like Chicago, where we were getting two turns a day, we're now able to get eight,” said George. “We are anywhere from three to four times more efficient with this process than the traditional appointment system.”
Likewise, dwell time of containers at terminal locations has dropped from seven or eight days to just two days or fewer, providing customers with substantial savings by lowering or eliminating demurrage costs.
“We're saving the customer money because we're billing less detention,” said George, "but we're also making the driver more money because they're so much more efficient. That's the key; our ability to close that gap, be more efficient and pay the driver more money. It's a huge deal for us.”
In addition, the SmartStacks system has reduced driver idling time by 67%, reducing emissions and fuel usage. It also helps improve chassis utilization and facilitates empty container returns.
“We wanted to improve the overall process for our customers, drivers and the industry,” said George. “This new process not only gets containers out of the gate faster, it gives the freedom to choose based on their own schedule and hours, provides the speed, attention and faster throughput at port facilities and improves the environmental impact caused by idling vehicles.”
The CCJ Innovators program is brought to you by Comdata, Freightliner Trucks, Omnitracs and Valvoline.