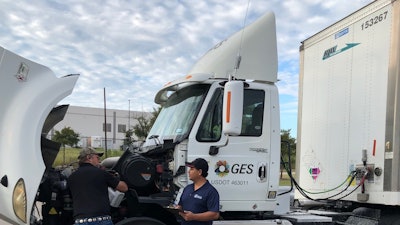
CCJ Innovators profiles carriers and fleets that have found innovative ways to overcome trucking’s challenges. If you know a carrier that has displayed innovation, contact CCJ Chief Editor Jason Cannon at [email protected] or 800-633-5953.
Non-compliance identified during a DOT inspection can result in substantial repercussions for carriers, including out-of-service orders, negative consequences on CSA scores, financial penalties, loss of time, and potential safety risks.
GES, headquartered in Las Vegas, Nevada, is a full-service provider in the exhibitions industry with hundreds of trucks and 400 trailers. Additionally, GES also supplements their need for product movement with rental trailers, which are often in poor condition due to lack of use and attention. After a string of poor inspections from 2019-2021, the company found themselves looking for alternative ways to improve vehicle maintenance and increase employee engagement.
Dane Holleron, Senior DOT Compliance Manager of GES, created the Gate Check Program as part of the solution. He noted that drivers often become complacent when it comes to vehicle pre and post trip inspections. “Regulations require that the driver be satisfied that their equipment is in good working order prior to utilization. The only way to do that is to conduct a thorough pre-trip inspection, allowing the opportunity to identify and correct any issues.”
Holleron proposed the idea of the program to ensure pre-trip inspections are being done and issues are being addressed. “The idea is to spot check drivers as they approach the gate [or] leaving the yard. By doing this, we can keep our drivers on their toes and possibly catch issues in the yard, before they are problems on the road," he theorized.
The program also encourages all employees, especially operations who often know very little about DOT regulations and restrictions, to get involved and perform gate checks. The gate check isn’t just a Monday morning pre-trip task, it can be done anytime and anywhere – from the warehouse, to the marshaling yard, and even at show site.
It’s also a way to ensure drivers can demonstrate a proper inspection on their equipment. “If a driver doesn’t have a very good system for inspecting the truck, it’ll be obvious to anyone who performs a gate check. When an employee, who is often unfamiliar with DOT, finds obvious issues, it’s embarrassing for the driver. This causes the drivers to make a better effort daily to avoid the embarrassment,” Holleron said. With the program, GES drivers are now doing their due diligence to ensure they are truly satisfied that their equipment is in good working order prior to use.
From a litigation standpoint, the program enables GES to have documented inspections and create indication of their engagement with drivers. It is also designed to meet the DVIR requirements, which effectively reduces a step should any defects be found.
Operating in 16 cities and with two maintenance facilities, GES launched the program in March of 2022. “Receiving top-down support from the beginning was crucial in its implementation and fostering a safety-first culture,” Holleron said. Before he joined the company and initiated the program, the company relied on other compliance and safety products. Prior to the program, GES posted maintenance percentiles in the 90s for several months in 2021 and a DQ compliance average of 65% during that same period. A CSA score of 90% or higher for more than two months in a row in two or more categories is considered high risk by the FMCSA.
Once the program was started, GES quickly saw success. The company achieved a maintenance percentile average of 76% in 2022 and an average of 57% in 2023. From March 2022 to March 2023, the company received 15 out of 20 “no violations found” inspections. In July 2024, GES posted a 26%.
GES
Holleron has attributed their improved CSA score in large part to the gate check program. When it was first introduced, GES was able to find and correct a multitude of possible infractions, such as faded/missing retroreflective tape, no annual inspection, chaffed hoses, and unsecured fire extinguisher. He pointed out, “When you improve your overall maintenance, you’re far less likely to get violations roadside, and that was the case for us.”
Before the program, driver managers focused more on hiring and qualifying drivers. To ease the process, GES implemented the use of driver recruiting software Tenstreet, allowing driver managers to focus on equipment maintenance and training. Holleron said, “Prior to the Gate Check Program, no one was really focusing on vehicle tracking and maintenance. We were reacting to issues once they became problems instead of proactively dealing with issues before they became problems.”
GES has larger depots in Chicago and Las Vegas with maintenance facilities, while the other locations rely on mobile and local maintenance providers. In lieu of this, the smaller locations tended to rely heavily on their drivers to identify maintenance issues.
The program promotes accountability by tracking metrics, maintenance, and repair of vehicles and trailers. GES aims for 50% of their trucks to be “gate checked” monthly, which has been successfully maintained for over 2 ½ years with companywide support.
Besides improving equipment maintenance, GES has seen additional benefits. Drivers appreciate management’s involvement, and employees are gaining a better understanding and appreciation for DOT complaince. “They are feeling a lot better about DOT now, it’s no longer a scary subject for them,” notes Holleron.
In 2021, GES also formed a DOT Committee with representatives from each of its operating cities to review metrics, create standardize practices, and provide monthly training on DOT-related topics. Driver managers use this information to conduct and document monthly driver meetings.
A crucial aspect in implementing a program like this, said Holleron, is seeing it through. Many companies lose enthusiasm over time, but for such policies to succeed, they need commitment, and sustained, top-down support.
The CCJ Innovators program is brought to you by Bestpass, Chevron Delo, Comdata and Freightliner Trucks.