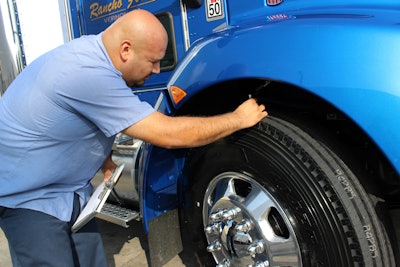
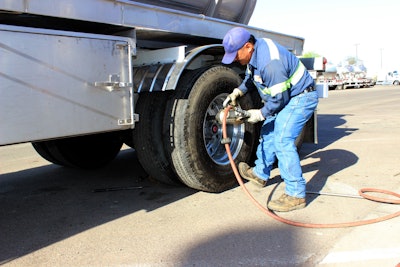
This story was updated April 27, 2021.
Tires accounted for 2,102 out of service violations (OOS) on the U.S. during 2020’s Commercial Vehicle Safety Alliance International Roadcheck – a whopping 19.7% of all trucks parked during the three-day enforcement event, and second only to brakes as a leading cause.
Roughly the same percentage of trucks were parked in 2019 and 2018 with tire and wheel violations.
With 2021 Roadcheck kicking off next week, a lot of things can go wrong with a tire. There are 12 tire violations that can place a rig out of service, but with 18 of them needing some degree of inspection, there’s plenty to overlook.
“When it comes to inspections by law enforcement, CSA assigns heavy point penalties for tire issues,” said Jason Miller, national fleet channel sales manager for Cooper Tire. “There are four times as many points against you for a worn-out tire as compared to driving a truck with no door.”
CVSA’s annual International Roadcheck tire inspections emphasize the importance of maintaining proper tire pressure. Industry research shows about 90% of tire failures can be attributed to underinflation, and nearly half of all emergency service road calls are tire-related.
“Driving on underinflated tires generates higher internal running temperatures, and that will lead to tire blowouts,” said Jon Intagliata, Bendix product group director for Trailer Controls. “What’s more, underinflation also puts unnecessary stress, wear and tear on the tires. This excess wear and tear has been documented and it can shorten the life of the tires. The American Trucking Associations’ Technology & Maintenance Council estimates that 20% underinflation can shorten tire life by 30%.”
Inflation level isn’t itself an OOS violation unless the tire is legally flat (an inflation pressure that is 50% or less of what is stamped on the tire sidewall), but overinflation and underinflation are leading contributors toward other citations.
“Thumping a tire with a mallet or club is and always has been useless,” said Paul Tatarchuk, B2BN special services coordinator for Michelin North America. Inflation levels should be checked using only an approved pressure gauge, he said.
“Using a thumper — a tire bat — is a longstanding ritual that really identifies only tires that are dead flat,” Miller added. “A tire that’s 20% to 30% underinflated is very tough to identify with a thumper.”
Proper pressure not only helps avoid potential violations, it also increases tire life, reduces fuel consumption and improves retreadability, said Pat Keating, senior manager of field engineering for Yokohama Tire.
“A $10 stick gauge is worth its weight in gold if used properly and consistently,” he said. “Some dealers provide yard checks as a free service.”
Fleets reluctant to invest in a tire pressure management system (TPMS) or an automatic tire inflation system (ATIS) should develop a manual system to standardize tire care and maintenance, Tatarchuk said.
“Even if a fleet doesn’t invest in one [a TPMS or ATIS system], the driver must check air pressure prior to each trip,” he said, adding that tires should be checked when cold before a trip. “If pressure is high in a warm tire, do not bleed out. Wait until it is cold, and then recheck.”
Time-consuming manual inspections actually can be more expensive versus investing in digital tire monitoring solutions, said Marco Rabe, Continental’s head of research and development for commercial vehicle tires.
“In addition, handheld gauges need to be calibrated frequently to ensure accuracy,” he said. “Even fleets with strong, standardized inspection practices can be deceived by an inaccurate pressure gauge.”
The inside position on a set of duals is more cumbersome to inspect, and, as a result, often get less attention, Miller said.
“Unlike steer tires, a low inner dual is very tough to detect visually,” he said. “Not only does that put the low inner dual in jeopardy, the additional load on the full tire it’s mated to may become fatigued.”
“Remember, an inside tire is there for a reason,” Tatarchuk added. “By design, it takes two tires at that axle end to carry the load. If the one inside is not carrying the load, the other is overloaded, and a dangerous situation may arise.”
In some ways, checking just the outside tire can increase irregular wear, because it increases the likelihood that the pressures won’t match, Keating said. Mismatched air pressure can cause irregular wear and have a negative impact on fuel economy.
When duals are mismatched for inflation, the tire with the lower psi wants to run at a smaller loaded radius, causing it to skip to keep up with the full tire, Miller said.
“Just a 5-psi difference in inflation between duals is the equivalent of one tire having a circumference that is 5/16″ smaller,” he said. “That means during every rotation cycle, the smaller circumference tire must scuff ahead to keep up with the tire with more inflation. These tires rotate around 500 times per mile, so simple math means you’re dragging a tire 13 feet every mile under load.”
Improper tread depth is one of several tire violations that can place a truck out of service immediately. Rabe said checking drive and trailer tires for at least 2/32″ of tread and steer tires for 4/32″ also provides an opportunity to give the tire a full once-over for pressure and damage.
“Even if tires are new, they need to be inspected prior to each trip,” added Tatarchuk. “Not just to see if the tread is deep enough, but to look for road hazard damages or if there are objects caught in the tread.”
When tires are worn to 2/32”, treadwear indicators become flush with the tread elements, making determining minimum depth easy. But Keating said any depth greater than 2/32″ should be measured.
“Despite their low cost, simple tread depth gauges are remarkably effective for determining tread depths,” he said.
Tatarchuk said the minimum tread depths set by the U.S. Department of Transportation are just that – the minimum – and that many fleets establish their own internal tread depth rules through their maintenance policy to determine when tires are to be removed and recycled for retreading.
“When fleets practice this method, they then have a factor of safety so they do not risk a violation for low tread depth or losing a good casing due to excessive wear,” he said.
“Pulling a tire at 2/32” leaves precious little room for error,” Miller said. “Any spot worn beyond that could sacrifice the casing, so fleets normally pull well before that. Plus, traction can be sacrificed when you run down to the legal limits.”
Keating said removing tires before they reach the minimum legal level also protects the casing for retreadability. “There is more casing protection at higher tread levels,” he said.
Miller said cutting it close on minimal tread depth can put a driver in a condition where the truck is legal on the way out but OOS on the way back. “Many line-haul truckers run as many as 2,000 miles per week, up to 4,000 miles for teams,” he said.
With steer tires wearing 10,000 miles per 32nd or less, a tire with 1/32” or 2/32” to spare is likely to drop below the legal limit by the time the truck returns to the terminal, Miller said. “It’s best to calculate those miles in advance to ensure you’re not cutting your tread depth to below legal limits,” he said.