Brakes light and tires are annually the largest equipment out of service violations during Commercial Vehicle Safety Alliance’s annual Roadcheck campaign, but the truck isn’t the only thing inspectors are pouring over.
ACERTUS CEO Trent Broberg joins Jason and Matt this week on the 10-44 and talks about the role drivers play in keeping a truck in CVSA's good graces.
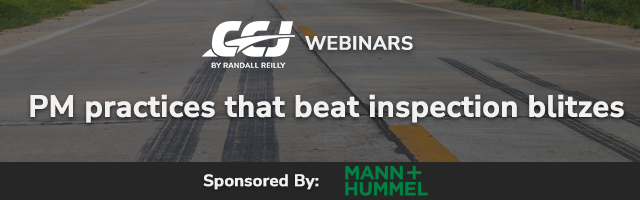
Did you miss CCJ's recent Roadcheck webinar?
Thursday, CCJ hosted a webinar, sponsored by Mann+Hummel, featuring some of the safest fleets in the U.S., to talk about roadside inspections. Did you miss it? Don't worry. We recorded it. Just click below, register and we'll send it right to you.
Contents of this video
00:00 CVSA’s Roadcheck and the driver’s log01:32 Using an ELD
02:48 ELD’s as a private matter
06:39 Preventative maintenance, pre-trip and post-trip inspections
07:52 Walking the driver through pre-trip and post-trip inspections
Jason Cannon
This week's 10-44 is brought to you by Chevron Delo 600 ADF ultra low ash diesel engine oil. It's time to kick some ash.
During CVSAs road check next month, recent history suggests inspectors are going to park more drivers for log problems than they will trucks with lights or cargo securement problems.
You're watching CCJs 10-44, a weekly webisode that brings you the latest trucking industry news and updates from the editors of CCJ. Don't forget to subscribe and hit the bell for [00:00:30] notifications so you'll never miss an installment of 10-44.
Hey everybody, welcome back. I'm Jason Cannon and my co-host on the other side is Matt Cole.
Brakes, lights and tires are annually the largest equipment out of service violations during CVSAs road check campaign, but the truck isn't the only thing that inspectors are going to pour over next month. Last year, 2,288 drivers were parked for either false logs or hours of service violations. That's about 70 more than lighting violations on the truck, and 350 more than [00:01:00] the number of trucks parked for cargo securement violations. And cargo securement is a focus of this year's campaign, which kicks off on May the 16th.
Matt Cole
Truck drivers are the original remote workforce. But that a log book or ELD is something the fleet rarely sees, it can be difficult for carriers to offer the same kind of management support into drive time like they can with truck maintenance.
Jason Cannon
ACERTUS CEO Trent Broberg joins us this week. And yes, while a driver's log is a personal thing to them, Trent says the fleet has to treat them more like a realtime time card than something that just lives in the truck.
Trent Broberg
If you're maintaining electronic logbooks, you can virtually eliminate hours of service violations when it comes to missing or incorrect driver logs. So when you think about hours of service compliance and basically fatigued driving, that's a big component. So around 30% of all driver violations during roadside inspections are attributed to missing or incorrect driver logs. So it's not about driving over the hours, it's not adhering to the policies, it's really just about displaying or making sure that the data is up-to-date.
So that's the way that I look at how technology plays a role in the driving community and the fleet community, is just ensuring you're maintaining the correct location of the ELDs. The ability to extract the log books out there in real time [00:02:30] to make sure that they're updating in real time and have a copy or understand what the operating instructions of the ELD are. Because trucks have ELDs in them these days, and our ability to assess the realtime data can eliminate those incorrect driver logs or missing driver logs.
Matt Cole
Maintaining the ELD and having access to the right and real time data from the ELD is critical in a roadside inspection. Thanks to Telemetry, the fleet has these insights into available drive time, whether the driver likes it or not. Sure that ELD is a personal account of a driver's day, but Trent says carriers and drivers have to agree to disagree on the ELD's consideration of being a private matter.
Trent Broberg
I think the JD, it's part of the job function. I think where that really stems from is back CSA 2010 timeframe where, and I understand this, the federal government is pushing regulatory practices on the drivers, even on the hours of service type regulations when the drivers oftentimes are pretty autonomous and should be treated as professionals out there in the space. And one bad apple can spoil a bushel, type mentality. But I think generally I'm for less policy restrictions and more at the fleet level, because I think at a privatized or fleet level, you can even do a better job with managing the safety and compliance of the fleet.
The collaborative effort between the fleet and the driver, and the entire industry as a whole, which includes parking issues and other challenges, it's really understanding the voice of the driver and understanding what the driver has to go through on a daily basis. Adhering to the policies that are in place, whether you like them or not, it's critical and I think everybody would say that they do, and that's important in leveraging technology to make sure you take the necessary steps to go through and understand where can I park ahead of time? What does the detention time look like at this location?
I've seen some police just go to Google reviews and start understanding when I'm delivering at this big [00:04:30] retail DC is there a lot of wait time? Is there not? And how can I help that driver be successful, because they're driving and that's the only thing they should be doing. They shouldn't be out there looking for parking on Google. They shouldn't be understanding where they're going to park, they should be driving and it's up to the dispatchers and those that support the drivers who are our most important commodity or asset in the space, support them, not just in finding them a load and forgetting them, but supporting [00:05:00] them throughout their day on their journey. Just as we would support everybody else in our offices and our customer support teams, and finance teams, and sales teams, that we're supporting them on a daily basis. It's important. Just because they're out of sight doesn't mean they're out of mind.
Jason Cannon
A Level 1 inspection is a comprehensive 37 step inspection process that involves a thorough inspection of the vehicle. And Trent says there are a few areas that fleets can shore up, but again, it goes back to the driver. He tells us what those areas are after a word from 10-44 sponsor Chevron lubricants.
Protecting your diesel engine and its after treatment system has traditionally been a double-edged sword. The same engine oil that is so essential to protecting your engine's internal parts is also responsible for 90% of the ash that is clogging up your DPF and upping your fuel and maintenance costs. Outdated industry thinking still sees a trade-off between engine and emission system protection and Chevron was tired of it, so they spent a decade of R and D developing a no-compromised formulation. Chevron lubricants developed a new ultra low ash diesel [00:06:00] engine oil that is specifically designed to combat DPF ash clogging. Delo 600 ADF with OMNIMAX technology cuts sulfate ash by whopping 60%, which reduces the rate of DPF clogging and extends DPF service life by two and a half times.
And just think what you can do with all the MPGs you're going to add from cutting your number of regens. But Delo 600 ADF isn't just about after treatment. It provides complete protection extending drain intervals by preventing oil breakdown. Before you had to choose between protecting your engine or your after treatment system, and now you don't. 600 ADF from Delo with OMNIMAX technology, it's time to kick some ash.
Trent Broberg
I think it's the same that it's been since I started 20 years ago, and it's really about the preventative maintenance and the driver inspections, so the pre-trip inspection. The same that it always has been. It's taking the time to validate the pre and post-trip inspections on not just the truck, but the entire equipment, [00:07:00] the truck and the trailer. Oftentimes, in these fleets, you're turning trailers, so you're unfamiliar with the trailer. I think north of 30% of roadside inspections, I was looking up a stat, are triggered by visible vehicle defects.
So when you think about lights and tires and just generally those visible and pre-trip can almost eliminate all of those roadside inspection triggers. When you think about lights, you think about brakes, and you think about tire issues, that accounts for half of, at least if my memory serves me, about half of the roadside inspection on vehicle maintenance side of things. So it's focusing on pre and post-trip inspection. It's the same that it's been for 20 years and taking the time to do that and then focusing on the vehicle maintenance and the preventative maintenance on lights, brakes, and tires.
Matt Cole
Fleets challenged with higher than ideal safety scores can get themselves on the right track. And Trent says it doesn't always have to be a significant financial investment or a drain on your time, but it will require a commitment to accountability
Trent Broberg
Fleets, small, medium and large, alike, including owner/operators out there in the space, which obviously make up a huge portion of the trucks on the road, can look to software to help remind and help walk through the checks in a pre- or post-trip. I've seen in our space, as a service, we work with around 8,000 carriers, we're not asset based, but I think where I've seen the best product from a carrier is where they take the time they adopt softwares for DVIR, which is at Driver Vehicle Inspection Reporting checklist through a mobile app. There third party softwares out there that you can sign up for. Some are free, some are paid. That'll walk you through that pre-trip every day and incorporating that into your general business practice, which includes vehicle maintenance, taking pictures of the [00:09:00] truck and trailer on the pre-trip and post-trip would be really helpful.
I think it's really just taking the time to walk through those steps. It's really an analogy. With ACERTUS, we do a lot of automotive logistics. That's what we focus on. And every time we pick up a car or deliver a car, we're doing that inspection report on the vehicle and it's the same that should be done even at a more granular level on the truck and trailer, pre- and post-trip. Just as everything, if you were to ask ACERTUS partners or maybe even my wife, I focus on discipline.
Having that disciplined regimen to make sure that you go through every step in a pre- or post-trip just to avoid the headaches down the road. And ultimately, we all want a safe driving community. We all have families on the road, and the more that we can provide back to that story and make sure that we're doing this together, the better off we all will be. And you eliminate your friction with your customers. If you have a breakdown on the road, you're creating friction in your customers, where oftentimes, like I mentioned, almost 50% of those vehicle maintenance to preventative vehicle means could probably be eliminated with the right steps and the right controls in place.
Jason Cannon
That's it for this week's 10=44. You can read more on ccjdigital.com. While you're there, sign up for our newsletter and stay up to date on the latest in trucking industry news and trends. If you have any questions or feedback, please let us know in the comments below. Don't forget to subscribe and hit the bell for notifications so you can catch us again next week.