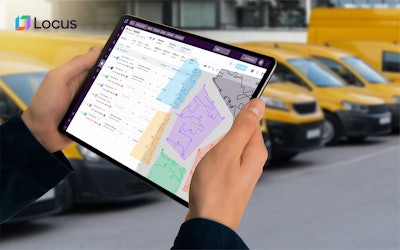
The face of the global supply chain has seen a significant shift in recent years as consumers have changed how they obtain their goods, and the turn to e-commerce was exacerbated by the COVID-19 pandemic when people couldn’t leave their homes and needed goods shipped directly to them in short periods of time.
It’s no longer early adopters using the technology it takes to participate in e-commerce. Nishith Rastogi’s parents order everyday products to be shipped to their home with the click of a button, and like all consumers, they expect that shipment to be at their door by its estimated time of arrival.
“What has happened in the last 10 years is a very interesting shift where people, as end consumers, have entered the supply chain. We used to go to a retail store and pull our goods from there. Today, most of our goods and now even services are being pushed down to us at our home and offices,” said Rastogi, founder and CEO of last-mile logistics technology company Locus. “That creates an entirely new leg of supply chain and a significantly more random, dynamic piece, which requires intelligent decision making.”
Shippers now have considerably more locations to ship to when getting consumer products to their individual households at a certain time on a certain day rather than a select few stores that then distribute products to the masses, and it’s not an easy thing to do, Rastogi said.
It has created logistical challenges from order to delivery as companies’ demand patterns are completely different on a daily basis, but Rastogi said real-world visibility can help alleviate those pain points.
Rastogi’s company recently launched its real-world order-to-delivery dispatch management platform that removes the responsibility of dispatching from shippers by connecting to their order management systems and offering a bundle of options to deliver goods to customers in an effective manner.
The platform uses advanced optimization algorithms and intuitive workflow automation to learn from previous outcomes to drive more efficient dispatch planning, scheduling and routing. It also helps increase visibility, capacity and carrier management under an integrated API-ready solution that helps streamline logistics complexities, maximize operational efficiency and improve end-user experiences, according to Locus.
The Locus platform provides a management dashboard that gives customers available delivery slots to select from so dispatchers can consider that in their planning. If a delivery gets delayed, Rastogi said the customer has the option to reschedule a limited number of times, which can save costs in last-mile delivery by avoiding failed delivery attempts, as a second attempt to deliver, he said, is four times more expensive when you account for the return costs.
And last-mile is one of the most troublesome and costly global supply chain processes. Rastogi said the last 14 miles of a 400-mile journey account for about 51% of the cost of the entire logistics process.
And it has real-world obstacles that can challenge even the most established companies. That’s why real-world visibility is more impactful than real-time tracking. Rastogi said it’s not just about knowing the location of materials; it’s about understanding the overall health of the system.
“In accomplishing all of this, one of the core aspects of the real-world (visibility) that comes out is factoring it in the decision making,” he said. “The problem of delivering between 9 and 11 a.m. is two parts: 1) Collecting the preference that you want to deliver between 9 and 11. 2) Having route optimization, which is capable of delivering between 9 and 11, not because it's mathematically the most optimized route, but it's a route that factors the real-world conditions: the traffic, the weather, of course, but also things like how wide is the road, and can the truck enter there; are there any local restrictions; is there a low bridge; what is the wind speed, which can factor into a side curtain truck; are there any pollution restrictions like is it an electric vehicle only zone; are there any railway bridges that it can't cross; what are the number of loading bays that exist, and what kind of stagger rate does it need to have; and so on and so forth, including driver preferences.”
But while real-world visibility may be more impactful for the supply chain, Rastogi said most companies today are engaging first in real-time tracking.
“Think of it as a digital adoption curve,” he said. “Layer one is digital visibility, layer two is automation and optimization, layer three is customer experience and layer four is realization of gains, where you can now start leveraging some of this customer experience to create your supply chain as a competitive differentiator.”