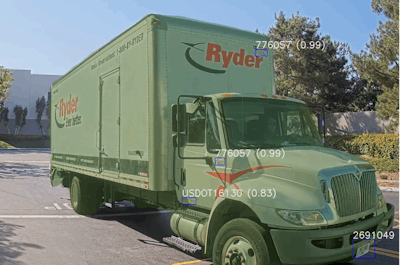
The supply chain has seen major disruption in the past couple of years – one common area of disruption being digitization across vehicles and warehousing, enabling an influx of artificial intelligence solutions, said Mike Plasencia, group director of new product strategy at Ryder and managing director of RyderVentures.
“But a place where it hadn't happened really was in the yard,” he said.
Plasencia said yard processes have historically been very manual. Individuals with a clipboard taking down vehicle, trailer, license plate and Department of Transportation numbers to keep inventory of available equipment is time consuming and often results in bottlenecks, delays, increased driver and labor costs and idle assets.
Ryder is changing that inefficient and error-prone process, moving away from the clipboard to computer vision.
Ryder launched a pilot with AI platform developer Terminal Industries in January, using fixed cameras at the gate to automatically index and analyze trucks and trailers using Terminal’s computer-vision technology. That program has processed more than 10,000 truck detections with 99% accuracy in capturing license plates and DOT numbers at a Ryder e-commerce fulfillment center in southern California.
Karen Jones, chief marketing officer and head of new product development at Ryder, said the yard has not previously seen this kind of accuracy with computer-vision technology.
“It’s one thing to build a text-recognition algorithm that works on static objects or in an academic setting, but it’s quite another in the real world, where we’re dealing with obscured license plates, hand-written DOT numbers, inclement weather and any number of scenarios that affect visibility for cameras,” Jones said.
The pilot’s success has led the logistics and transportation company to launch another pilot with Terminal at its truck rental and maintenance facility in the Dallas-Fort Worth area but for a different use case.
Ryder has 100 million square feet of warehouse space, over 700 shops, countless yards, all of different shapes, sizes and configurations, so no one solution is going to fit all, Plasencia said. Rather than having a fixed camera at the gate with a moving vehicle driving by like at the SoCal facility, the Dallas facility has a fixed vehicle with a camera moving by.
Ryder is using Terminal’s technology on mobile tablets to auto-capture available inventory. Employees can walk through the yard and capture data via a tablet rather than using pen and paper on a clipboard or even manually entering that data onto a tablet keyboard.
Plasencia said these pilots are helping the company drive efficiency; a task that previously took hours a day now takes only minutes a day. And, he said, there's no limit to the applications of this technology.
Terminal approached this as a core technology that works on commodity hardware, said CEO Max Constant.
“Other vendors may focus on one specific application or one specific use case. We actually like to build new science that enables a whole world of new use cases,” he said. “Then we turn the power back over to the folks who know how to use that data the best, which is the Ryders of the world.”
Plasencia said Ryder’s initial need was data capture for regulatory requirements. This pilot, he said, has provided accurate, auditable data, and Ryder is able to query off that data and build reports and databases. An added bonus was increased throughput because vehicles weren’t having to queue up and wait for somebody to manually record the data, so it’s savings in labor and allows employees to focus on other activities, he said.
Constant said once that data is at their fingertips, companies like Ryder can work with Terminal to determine best use of that data, like making a specific process more efficient.
“I think that's the right approach for the logistics space, broadly speaking, because there are a lot of different stakeholders around the table that have a lot of different uses for that data,” he said. “If I overfit to a very specific path, I lose the broader vision.”
Simply put, Terminal uses cameras – fixed or mobile – to index and analyze image and video data around what makes the supply chain move: trucks, trailers, chassis and containers. To compensate for common errors in recording this data, Terminal’s computer-vision technology uses machine learning by adding incremental knowledge to continuously improve, and integration with third-party databases provides full vehicle profiles beyond what cameras can see.
“The way we think about it is like we're building a universal or a common language of the yard upon which many different things can be built,” Constant said. “So you can imagine, over time, if you build your core technology the right way, you can connect hundreds if not thousands of yards with hundreds if not tens of thousands of cameras, all speaking together in real time, leading to a more efficient, transparent, stable, secure supply chain.”
Terminal estimates that more than 90% of yards lack the technology to operate efficiently, costing the industry up to $146 billion each year.
Offering a technology that embraces a broad range of use cases rather than focusing on a specific pain point simplifies and streamlines processes, manifesting itself in cost savings, he said.
Some of the potential use cases include regulatory and compliance, gate acceleration, asset tracking, appointment scheduling, inventory, and many other challenges yard operators face.
Constant said brining this level of visibility to the yard – and in the future many yards together – unlocks multiple layers of value. Plasencia said he sees Ryder eventually using this technology to connect all of the company’s yards and facilities for greater impact.
“At the end of the day, it's just a truck, trailer, chassis or container, but you have these core data points that can be reconfigured to drive a lot of different value all on the same backbone. In other words, one piece of technology – one core backbone that's used many times – as opposed to 10, 20, 30 different pieces of software that need to be integrated and cross-trained on,” Constant said. “There are all kinds of derivative effects that could come just by virtue of knowing what's on the yard, and a well-functioning yard drives everything else that comes after that.”