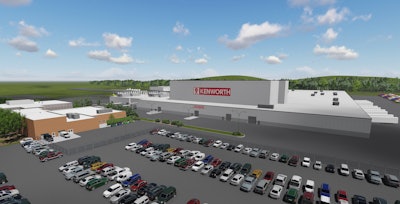
We saw it next to the robotic arm that installs windshields on truck cabs at the Kenworth assembly plant in Chillicothe, Ohio.
It was an elevator—a very large parts elevator—about 15 feet behind us. One of the reporters in our tour group spotted it behind a large sheet of plastic.
It’s part of the plant’s $17 million expansion into automated parts storage and retrieval which Kenworth execs say will make truck assembly more efficient and less labor intensive.
It wasn’t the only parts elevator. Another one was near an entrance to the plant, which we would see a short time later at the end of the tour.
Kenworth announced today that the expansion will add 25,000 square feet directly above the plant and allow them to automate the process of storing and pulling cabs, sleepers and hoods instead of having to store them outside.
“That’s to be commissioned in November to avoid another winter of tugging cabs in the snow,” plant manager Judy McTigue had explained prior to the tour.
“It’s a tremendous investment for the company, for the safety of our employees, for the quality of our trucks, but also for efficiency for this organization and for the company.
“We’ll have more employees doing value-added activities versus tugging product around. So, we’re really excited about that investment and excited about changing the face of our building. We’re going to be twice as tall as we are today.”
The expansion has taken place while the plant remains in operation. McTigue explained that engineers deserve credit for keeping the plant operational while the addition goes up above the assembly lines below.
“We’ve dug up concrete, set large footers down in the base of our factory to set columns in so that we could get the grid iron in place and then build this building on top of the existing building—and all while continuing to produce on both shifts within our factory,” McTigue told several reporters seated around a large conference table.
Normally, after being painted, large body parts have been stored outside. Some have been kept out of the weather, some not. Starting this November, the body parts will be assigned a unique identification tag after being painted and will then be transferred upstairs into storage through an automated system. Then, when the part is needed, it will be automatically retrieved through a giant vending machine-like process, McTigue explained.
The automated process will save time and effort at the 42-year-old plant.
Despite sluggish class 8 sales—FTR Associates recently reported that sales were at the lowest levels since April 2010—McTigue is confident about Kenworth’s position in the market this year and believes the new addition will only help to further enhance its business.
“The first quarter is always a little bit sluggish. We’ve gone up a little bit, just a few trucks this year. So, I wouldn’t say we’ve gone too far, because the first quarter is always a bit sluggish.
“But we’re pretty healthy right now and we’ve got nice visibility (lead time). Suppliers are performing really well for us. We have very few shortages. The supply base is pretty healthy. We’re sitting at really over five weeks, so that’s nice visibility for us.”