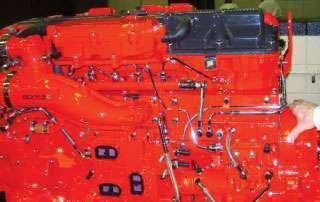
The clearances inside diesel injection system parts are closer than those found in any other technology. The plungers and needle valves in injectors need to fit tightly to ensure precise metering and avoid wasting energy in generating extremely high fuel pressures in excess of 30,000 psi.
While the new common-rail designs shun unit injectors in favor of a high-pressure pump and injection nozzles with on-off valves, the clearances in the pump and inside the nozzles are just as tight for the same reasons. “A single fingerprint on the XPI injector plunger will bind the injector to prevent injection sequence,” says Zack Ellison, Cummins’ director of customer technical support.
As emissions standards have gotten tighter, the already tiny holes in injection nozzles have gotten smaller to increase injection pressures. Research has shown that the tinier the holes and the higher the pressure, the less soot the engine will produce – and the better it will perform.
Tinier working spaces also mean that fuel must remain dry. Water not only can wash lubricating fuel off hard-working injector parts, its different flow characteristics also can blow the tip off an injector.
Use a primary filter that includes water separation capability (which means specially treated paper that keeps water from passing through), a reservoir to catch water and a drain, says Paul Bandoly, Wix Filters’ manager of technical services and customer training.
Most of Detroit Diesel’s engines are equipped with a Davco primary filter and water separator. “Not all primary filters have water drains,” says Scott Faris, technical service manager. Those that do have drains – which typically are called primary water/fuel separators – should have 93 percent minimum efficiency on emulsified water. “They should be drained daily, which is easy to do since most have a handy valve on the bottom of the filter.” All Series 60 engines built after January 2004 come with a water separator system. “It’s also essential to drain fuel tanks monthly, and never right after refueling,” Faris says.
Most engine makers specify an initial setting of overheads early in an engine’s life, just after it breaks in and settles down.
All DD15 filters should be changed at 50,000 miles, and a Davco filter allows change intervals to be extended to beyond 100,000 miles depending on fuel quality, says Brad Williamson, Detroit Diesel’s Powertrain communications manager. The filter assembly has a water-in-fuel indicator that a driver can check during a routine walkaround.
Also use the specified primary and secondary fuel filters for a particular engine; Bandoly calls this “prescription filtration.” Ellison says a 15-micron filter is used with Cummins’ HPI system, while a 10-micron primary Davco fuel-water separator and a 5-micron secondary filter are used with the XPI system. Fuel filters must be changed at 25,000 miles on both the HPI and XPI systems.
Caterpillar fuel filters should be replaced every 500 hours, says Geoff Monari, on-highway product service engineer.
Timing is everything
Most heavy-duty engines today have camshaft-driven unit injectors. While the actual timing of injection events as they relate to crankshaft position is determined by the electronic control module (ECM) on all electronic engines, the mechanical relationship between the injector, rocker and camshaft are critical, and the ECM has no control over them. The responsible parties in this area are a fleet’s technicians.
While heavy-duty overhead adjustments are fairly stable – especially after engine break-in and an initial correct adjustment – they change over time. Neglecting the injector rockers ultimately means the injector plungers will be forced downward by the wrong area of the camshaft lobes. This means a slower motion, and less fuel and lower injection pressure, which often means a loss of performance and possibly some smoke. On the Cummins ISX, failure to adjust also eventually will delay injection timing.
Most engine makers specify an initial setting of overheads early in an engine’s life, just after it breaks in and settles down. Caterpillar customers should do an initial adjustment between the first and fourth oil change, then adjust them every 300,000 miles, Monari says. Detroit Diesel recommends setting the overhead at 60,000 miles. “The injectors are electronic and do not require adjustment,” Williamson says.
The ISX is an exception, with no initial adjustment and regular adjustments every 500,000 miles. Adjusting the overheads according to the factory procedure will help guarantee long injector life and good performance. Valves are adjusted at the same time, and with the XPI, as with all common-rail systems, it’s only the valves that should be adjusted.
Common-rail uniqueness
Unit injectors drive a central plunger downward with the camshaft and rocker. Injection pressure is determined by the hole size and the rate of fuel delivery, which means the system performs best at governed speed. At peak torque and any low-rpm operating condition – especially during cranking – injection pressure is less than ideal.
The solution is common rail, which is used on the International MaxxForce Big Bore engines, the Detroit Diesel DD15 and its two sister engines, and both 2010 Cummins ISX engines, which use the new XPI injection system and have no injector camshaft.
A common-rail system uses a high-pressure pump that provides fuel to a rail that holds enough fluid to stabilize the pressure. Because the pressure can be kept high, even under cranking conditions, low rpm performance and starting are improved greatly. International says it will continually improve its system in order to enable its 2010 MaxxForce Big Bore engines to swallow more exhaust without generating more particulate matter.
Troubleshooting tips
Most troubleshooting today is done by the ECM and its onboard diagnostics, so the days of removing the exhaust manifold and examining the exhaust from each cylinder are over. The ECM of the Volvo D13, which uses an extremely high-pressure unit injector system, will store a trouble code if one injector delivers less power than the others.
On most late-model engines, when an injector is replaced, technicians must key it to the engine’s ECM so it can be identified in case of such trouble.
On common-rail systems, the ECM controls rail pressure by controlling pump output and matching it to fuel use, receiving pressure information constantly via a pressure sensor on the rail. On the XPI system, it accomplishes this by adjusting the length of time the valves admitting fuel to each pump cylinder are open.
Caterpillar’s common-rail fuel systems do not require pump performance checks. “The ECM is able to determine the health of the system and would log a diagnostic code if a problem were present,” Monari says.
Detroit Diesel’s fuel system diagnostics will alert the operator to any injector faults. “Our diagnostic link has very high-end diagnostic capabilities and troubleshooting procedures that can be updated online,” Williamson says. “Utilizing fault codes and the diagnostic link will lead the technician through troubleshooting procedures and service routines, and a verification of the repair.”
Troubleshooting trees and technician training are critical for accurate diagnostics, Ellison says. “Fault codes help the customer to know there is a problem that needs to be looked at – could be other symptoms, too – but the fault codes are the primary notification to the operator,” he says.