Rebuild your stopping power
Solve brake system troubles through proper relining
Smart fleet maintenance managers know there can be major issues with brake shoes relined in an unsophisticated shop, largely because brake shoe rebuilding is an unregulated industry. Products turned out by rebuild shops often reflect that fact. Stemco, which believes strongly that a high percentage of brake shoes are relined improperly, is planning a line of all-new shoes at a price close to that of relined ones. New shoes, the company says, will take the variables out of remanufacturing and reduce overall costs.
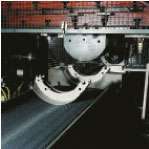
Bendix Spicer Foundation Brake has found chronic problems in shoes from reline shops, including creating table and rivet hole distortion when shearing old brake material off, incomplete removal of old anti-corrosion coating, improper application of the replacement coating and uncontrolled, inconsistent riveting. The shoe must be “coined” or reformed in a dye that will restore its original geometry, thus ensuring that the lining’s curvature will conform to the shoe’s curve.
According to ArvinMeritor, typical problems with unsophisticated rebuilding include a failure to coin the shoe, an ineffective process to paint the shoe to protect it from corrosion and a tendency to reuse old shoes even when they are not suitable because of a lack of cores.
Haldex, which grades shoes from 1 to 6 and throws away anything from 4 to 6, builds the cost of replacing shoes into the cost of relining them. Haldex believes recoining is a waste of time, as only a tiny percentage of shoes actually end up distorted enough to benefit from it.
On the other hand, the process “leads to the utilization of too many cores that should have been scrapped in the first place,” says Brian Cordle, sales and marketing manager for friction products. “Coining may flatten tables, but it can’t account for weakened shoe tables or weak areas around the rivet holes.” Haldex also says a coined shoe is fatigued and often does not retain its proper shape throughout its second lifetime – potentially leading to a cracked and loose lining – so the company simply replaces distorted shoes.
Don’t get rusty
Another major problem with relined shoes is rust-jacking, a process where moisture and road-deicing chemicals rusts the table. Metal expands when it rusts, much as water expands when it freezes. As rust builds up, it pushes outward against the lining, “jacking” it up between the rivets, until the lining cracks. Once the lining cracks, it is unsafe and must be replaced − cutting short the brake shoe life and denying truck operators its full value – often with a thick amount of lining remaining.
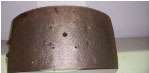
Matching the curvature of the shoe and lining is critical because a tight-fitting lining seals out moisture and road-deicing chemicals, while ensuring uniform contact with the drum so all of the lining goes to work, thus extending its life. Uniform shoe-to-drum contact is the key result of proper shoe remanufacturing and the reason it pays big dividends, says Todd Heim, Stemco’s brake product manager.
Properly coating the shoe is one critical key to preventing rust-jacking. Bendix brake shoes are coated with an enamel-based specified coating material to maximize their anti-corrosion properties. The coating material’s controlled application and curing process takes into account time, temperature and humidity tolerances. “This critical process improves corrosion protection and ensures proper drying, as well as superior adhesion,” says Carl Swanson, product manager of aftermarket brakes for Bendix.
ArvinMeritor’s PlatinumShield coating helps protect the shoe table by preventing microabrasions so that rust-jacking does not occur during the brake shoe’s expected life. Doug Wolma, general manager of remanufacturing, says the coating process was researched via the ASTM B-117 Salt Spray Test and that the company’s shoes rate “higher than 8” on the ASTM scale.
Corrosion protection is “50 percent the paint you use and 50 percent how you apply it and cure it,” Cordle says. Haldex Friction Centers incorporate computer-controlled processes to oversee environmental conditions during curing. Haldex also has a running program with paint manufacturers to develop new paint solutions that are better than their predecessors.
Remember riveting
Painting is only one aspect of the process; the means of riveting the lining onto the shoe and quality control inspections also are critical. Most field failures include cracked blocks, failed blocks (removing from brake shoe), drum distress or cracking, wheel-end burnup (fire) and failed roadside inspections, as well as shortened lining life and accelerated drum wear.
“Out-of-service issues are definitely a concern,” Cordle says. Compromised shoe aspects such as damaged roller or anchor ends hinder installation and braking performance, and such damage prevents the shoe from forcing the lining against the drum evenly.
During a brake job, replace hardware such as rollers and return springs, and check cam-bushing play, replacing worn bushings if needed. Drums should be well within tolerance; not only are worn drums less able to store heat, the larger inside diameter means poorer drum-to-lining contact. The right new shoes and other hardware mean full contact, which leads to cooler operation of the lining, more powerful stopping and longer life. n