Can investing in training during tough times tighten up your bottom line?
Controlling costs is a hallmark of any successful company. But when times are as hard as they have been in the trucking industry, managers must make tough choices to balance the books. All too often, technician training is a target that bean-counters can’t pass up.
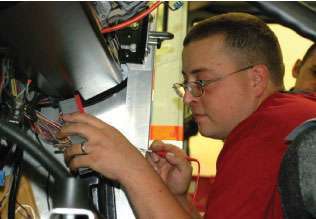
In many ways, it’s the technicians’ own fault. “I think that for quite a long time, technicians in this industry have done such an outstanding job keeping fleet vehicles on the road, their ability to do so kind of gets taken for granted,” says Bonne Karim, fleet training manager for the U.S. Postal Service. “Why waste money sending technicians to schools when they’re clearly getting the job done anyway?”
Savvy fleet managers like Karim know that’s not how the world works. Technician motivation and training are two key drivers in controlling maintenance costs and reducing downtime. For James Mathis, senior manager of global vehicles for FedEx Express, highly trained technicians are vital to his company’s success.
“Any time you can have a qualified technician – one who is highly skilled and educated in diagnostics and repairs – you can control the quality and cost of a repair,” Mathis says. Benefits of highly trained technicians include higher quality repairs and fewer road failures.
It’s not hard to translate fewer road failures into additional profits. “Technicians have a direct impact on customer service,” Mathis says. “They hold the key to minimizing loss of revenue from service failures.”
Education matters
An educated technician can better diagnose and repair a problem in a timely manner, which enhances the entire team’s productivity. “Educated technicians absolutely can have a positive impact on maintenance cost by utilizing expensive shop diagnostic equipment more effectively to make good repair decisions, using only the parts required and preventing repetitive failures and extensive downtime,” says Eric Benge, regional maintenance manager for Wal-Mart Transportation.
Advanced technician training probably is more important than ever as vehicles grow in complexity. “An untrained technician attempting to work on today’s complex equipment will in many cases find themselves chasing ghosts and throwing parts at a problem hoping for a positive outcome,” Benge says. This typically will result in unnecessary high parts costs, along with extended, repetitive equipment downtime.
FedEx Express technicians show their skills on the floor during a company technician competition.
Everyone is under pressure to reduce operating expenses, especially in today’s economic environment, Mathis says. Unfortunately, maintenance is viewed as a cost because it doesn’t generate a revenue stream. While that makes accounting sense, Mathis argues it’s a shortsighted strategy that ultimately is self-defeating.
“We always must be mindful that truck technology is ever-changing,” he says. “If the technician work force is not up to date on the latest technology, your company will pay the cost down the road in excessive out-of-service time, possible delivery service failures and progressive damage from improper diagnosis.”
Continuing education helps technicians add value to the organization by reducing repeat repairs and unneeded parts replacement while increasing vehicle life. “Any time you can develop your people, the long-term result is a reduction in overall operating expenses,” says Mathis.
Nick Knebel, a U.S. Postal Service lead automotive technician based in St. Louis, believes technician training is a top priority. “In a fleet atmosphere, you’re working on the same types of vehicles all the time, and then, all of a sudden, you get a thousand new vehicles, and they’re all high-tech and everything’s different,” Knebel says. “That’s why you have to keep building your knowledge base. It’s too overwhelming to just stay complacent and then all of a sudden everything changes. You have to change with the flow of technology and keep educating yourself slowly, so it’s not such an overwhelming task to figure out how these new vehicles work.”
Outsourcing anxiety
Another argument for cutting technician training is that ever-increasing repair costs and complexity issues make it justifiable to outsource major repairs to an experienced dealership or specialized repair shop. But it’s an argument most fleets don’t buy for a variety of reasons – mostly because of the need to get the vehicle back on the road quickly and earning money again.
Guy Warpness, campus president of WyoTech technical college in Laramie, Wyo., owns a pickup that’s still under warranty, but since his local dealership closed, he has to take it to Cheyenne for repairs – but only when he has time, and only when he can secure a rare available slot at the Cheyenne dealer’s shop to book an appointment.
“It may take me a week to get it in the shop, and I don’t think a lot of fleets can afford to have a truck sit for a week before a dealership can take it in and turn around and have it be there for another week, and then be without a vehicle for two weeks,” Warpness says. “Your technicians are a competitive tool that are absolutely crucial to your fleet’s ability to make a profit, because if your trucks aren’t moving, they’re not making money.”
Outsourcing may make sense for some fleets, Mathis concedes. The issue, again, is cost. Sending complex repairs off depends on the size of the fleet and the complexity of the equipment mix. “In some situations where you have very small fleets – 50 to 100 power units – it may be more cost-effective to leave the complex diagnostics to a specialist, dealer or repair facility, especially if the fleet will be required to invest in very expensive equipment that may be used infrequently,” says Mathis.
Although Wal-Mart prefers to keep its maintenance work in-house, the company maintains good relationships with dealer networks that support its fleet. “They are critical to our success,” Benge says. “For that reason, we partner with our OEMs right out of the gate with new equipment.”
Understanding upper management’s concerns regarding maintenance costs has helped Mathis acquire the tools necessary to help make certain his technicians stay ahead of the ever-present learning curve so they can perform those functions in-house and help control quality and cost. “We try to minimize the cost of the equipment by encouraging our suppliers to provide the software and the diagnostics capability that we can load onto the shop computers,” he says.
Simple steps, impressive results
The thought of establishing an effective technician training program from scratch may seem daunting. Even simply recommitting resources to renew or upgrade existing programs can be tough for fleet managers facing reduced budgets and lack of management support.
Luckily, help is available: OEMs and dealers are outstanding resources, technical colleges are emphasizing computers and sophisticated electronics, and state, regional and national associates such as the Technology & Maintenance Council are placing new emphasis on technician training.
“Training of technicians should not be an afterthought,” says Lee Long, director of maintenance for Southeastern Freight Lines and chairman of TMC’s national SuperTech competition. Before signing any equipment purchase contracts, fleets should include a supplier agreement letter asking for technical training, diagnostic software and access to service literature so technicians can maintain the units being placing into service.
“You may not get everything that you have asked for, but you should be able to negotiate some of these items from the supplier,” Long says. “Many of the OEMs have internal training. There may be a possibility to access this information to allow for the training to your shop associates. In doing so, this will drive down your training costs.”
A good – and easy – starting point is encouraging technicians to participate in voluntary ASE certification programs as a basis for developing their baseline skill set.
“Listen to your technicians,” Benge advises. “They’ll tell you what they need. Seek out a continuing education platform that works for your organization. Establish a multipronged approach, and remember there is no ‘one size fits all’ program out there.”
Mike Jeffress, vice president of maintenance for Maverick Transportation, says fleets considering additional training must take generational differences into account. About five years ago, Maverick began offering different types of classes for its technicians in order to give them the optimal means of educating themselves. “We found that senior employees prefer classroom theory and then a hands-on approach,” Jeffress says. “Our younger technicians just wanted online courses and time to research the material at their own pace. Both approaches required additional planning and organization.”
Maverick’s courses evolved over time, and today most of the company’s technicians use online courses first and then follow up with hands-on instruction. “I feel this works best because we all learn at a different pace and no one likes to be ridiculed for how fast or slow they may read or learn,” Jeffress says. “I don’t care how long it takes as long as we are putting an effort toward continuous development.”
Getting away from the shop – even for just a few hours – is another trick Warpness has found to be effective. “Training onsite never seems to work as well as I’d like it to,” he says. “The problem is you get the technician in class, and the service manager is coming in there every 30 minutes and pulling him out because they have a problem. But if you can get them away, even two blocks away, they get more out of their training.” Leaving the shop also is seen as a reward. “They feel special that they’ve been sent somewhere and the company is investing in them.”
High-tech techs are crucial in today’s environment, Mathis says. “You hear a lot about the costs of these programs, and I know a lot of fleets are small and they have a very difficult time doing the cost-analysis to justify the return on their investment,” he says. “They’ve just got to remember to keep it very simple. What is the cost of the training? Add in the wages for the tech that’s going to be in the training, and divide that out by the return that you’re going to get by not having downtime or service failures.”
It’s easy to capture the cost of training, but it’s more difficult to quantify ROI, Benge says. “But you see the benefits of advanced training in technician morale, confidence and productivity.” n