Everyone talks about shop safety. But how serious is your fleet about it?
Nobody wants accidents in their shops. Besides the physical harm they might cause, they’re also expensive in countless ways: Lost time and productivity, medical bills and workman’s compensation are just a few of the immediate costs. That’s not even considering more debilitating regulatory fines and legal costs.
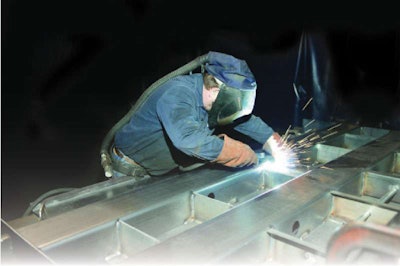
By all accounts, creating a safe working environment for technicians makes good business sense. But everyone talks about safety and insists it’s a priority for their company. Is it really?
Safety is indeed a stated priority for West Brother’s Transportation Services. Ralph Clemons, vice president of safety for the Durham, N.C.-based fleet, says that while safety always has been addressed, it always wasn’t part of the company’s culture the way it is today.
It was the same story at CFI in 2000 when Bruce Stockton and Randy Cornell began to look hard at the Joplin, Mo.-based company’s safety practices. Today, the company now known as Con-way Truckload is recognized industrywide as a leader in progressive safety programs. But 10 years ago, Stockton – who now is vice president of maintenance – says the emphasis was quite different. “It was in our culture to be safe if you were a driver,” he says. “But it wasn’t in our culture to be safe if you were anybody but a driver.”
Ten years ago, the fleet was outsourcing its maintenance work but was in the process of bringing that work in-house – a perfect time to address shop safety.
“One of the things I noticed that was missing right off was any kind of awareness toward safety,” Stockton says. “It seemed like every week somebody was getting hurt. The injuries weren’t serious – primarily cut fingers and things getting in peoples’ eyes. So we talked about safety, but in reality, it was a program without any principled practice.”
Starting at the top
Changing the culture at any company is never easy. Tradition, habits and simple human nature – “We’ve always done things this way” – conspire to undermine even the most well-intentioned safety program, especially when it’s just getting started.
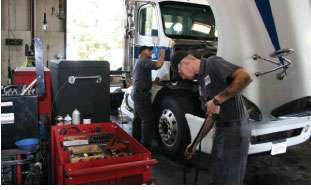
For those reasons, both Clemons and Stockton believe any fleet manager who is serious about putting an effective safety plan in place must have the full support of the company’s owners and upper management.
West Brother’s was serious about setting up a safety plan and did so in a rather plain-spoken manner. Clemons had the full backing of the owners at that time, Craig and Tommy West. “Our approach was very simple: We announced that we were developing a culture where our employees were simply not going to have accidents,” Clemons says. Over time, that basic philosophy has been stressed repeatedly. “Today, our technicians do their job every day just like somebody was watching them, when really nobody is. They have adopted a culture of not wanting to get hurt.”
Stockton says for fleets big and small, hearing that safety is a priority of top management can make a huge difference, but that only goes so far. “You have to reinforce safety by getting everyone involved,” he says. “The best way to do that is ask your employees for their input and feedback.”
Ask shop workers what the company needs to do to make the shop as safe as possible. “They’re going to think that’s funny and say, ‘Well, boss, it’s just me and one other technician.’ Your answer needs to be, ‘I understand that. But I’m asking you: What do we need to do?’ You’ll be amazed at how well that works,” says Stockton.
Another crucial factor, according to Clemons, is to begin safety awareness as soon as a new employee walks through the door. West Brother’s established its Excellence Training Program that gives all new hires two to three days of intensive safety training depending on their job.
“If they’re a technician, we cover shop safety on everything from grinding wheels to table saws to tire repairs,” Clemons says. The newcomer then goes to the shop for hands-on work with all components. Later, the new hire is taken on a mock road call on the company’s service truck. “We set up a large truck to work on. It’s a course based on real-world working conditions, and it’s very effective.”
Setting a baseline
Once a fleet is committed to raising safety standards, it must establish basic parameters to determine if the plan is successful. Greg Thieman, East Coast truck service director for TravelCenters of America and Petro Truck Stops, has 1,500 employees in his organization. “Our company, along with me and my managers, are responsible for their safety,” Thieman says. “Injuries are expensive. If I have hurt people out there, we’re not going to be able to serve our customers, so it’s very important to us to make sure safety is first in line.”
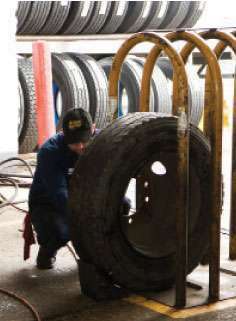
Thieman started with the basics before expanding his shop safety program to meet the company’s specific needs. This included OSHA 300 logs, in which the number of recordable injuries and illnesses – and the lost days associated with them – are summarized for each workplace. The summary must be certified by a company executive and posted at a location were it will be seen by employees. “That’s a good starting point for any fleet, and it’s how we judge our individual profit centers and shops.”
From there, Thieman says, a safety program should become a living, breathing thing and move toward education and personal protective equipment. TravelCenters of America and Petro recently trained all technicians and managers on the Tire Institute of America Safety Standard; about 60 employees now are TIA-certified tire safety trainers. “It’s a recent example of how we’ve upped our safety program and kept it current.”
Ivan Wagner, director of response and risk for TravelCenters of America and Petro, believes monthly safety checklists also are important. Each manager is responsible for completing them and also picking a technician to do the inspection with him. The goal is to increase the safety education of technicians so they will better understand the safety-related issues managers must address.
Also, a company technician from each shop is required to attend a monthly safety committee meeting. “If there are any issues out in the shop, the technicians have the opportunity and the responsibility to bring them to the attention of the safety committee,” Wagner says. “The issue is addressed, noted and followed up on.”
Con-way Truckload’s technicians serve terms on the fleet’s safety committee and must nominate co-workers to replace them when their terms are up. Stockton also sends any technician who is injured on the job to meet with a safety supervisor for an interview to see what can be learned from the incident, such as: What could management have done to help you prevent this injury? Is there a piece of protective equipment that we don’t have that we should have? Is there a process that we’re asking you to follow that’s not as safe as it could be?
“We’re not trying to make them feel bad or put them on the spot because they had an injury,” says Stockton, who developed the interview process with Cornell. “We’re just trying to reinforce that awareness that ‘Hey, they’re making a big deal about this. They pulled me off the floor and had me go to the main office and talk to this guy.’ I think making a big deal out of it keeps it in their mind, that safety really is important.”
Following up
A safety program must be reinforced vigorously or else it will fade into the background. Most managers stress the need to get out in the shop, walk around, talk to technicians and see for themselves what’s going on. “When I look and see things that are clean, organized, people working well and working safely, it’s a pat on the back for that technician and a ‘thank you’ for what you’re doing and the way you’re doing it,” Clemons says.
Steph Sabo, maintenance manager for Nashville, Ill.-based Norrenberns Truck Service, is always on the lookout for tripping hazards. “Air lines and oil and grease are everywhere in the shop, and they can cause a lot of problems if you don’t clean them up when a job is done,” Sabo says. He also makes sure that safety glasses are being worn and jackstands are being used. “I want to know that everyone is being careful anytime anything is going up in the air.”
And safety education never ends, managers say. New technology coming out today – hybrid trucks with high-voltage powertrains and selective catalytic reduction engines with higher engine and exhaust temperatures, for example – will change the way technicians work tomorrow. As a result, continuous improvement on existing safety programs must become part of the technician education process for successful fleets. n
Making safety training fun
At Con-way Truckload, whatever works is on the table
It might seem strange to think of safety as fun, but Randy Cornell and Bruce Stockton have worked hard to interject a lighter side to their safety program at Con-way Truckload. “Bruce started all this,” Cornell says. In 1998, Stockton made a challenge to then-CFI drivers that he would shave his head if they set a new record for low accidents. They did, and he lost a lot of hair.
But the stakes have escalated since. Stockton has allowed his technicians to shrinkwrap him to a shop beam for a half-hour of good-natured abuse if they met certain safety goals. In 2008, Cornell agreed to take a shot from a police-issue Taser if the company met certain safety goals. In 2009, he parachuted from 10,000 feet after Con-way Truckload drivers exceeded their safety goals for the year.
“We set a record low for vehicular accidents two years in a row,” Cornell says proudly. “Really, it’s amazing how word travels through the company – even with drivers because they’re so transient. But something like getting Tasered or skydiving just becomes viral. I can walk down the hallway and have drivers come up to me joking about jumping out of the plane. While it’s all fun, they probably don’t realize that every conversation like that instills safety in their minds. It makes them think about it.”
Regarding the shrinkwrap hazings, Stockton says he’d rather be embarrassed for 30 minutes than have to call OSHA and tell them about a serious injury or have to sit in a witness stand taking questions from a lawyer. “I’ll make that trade anytime.”
For tips on some of the most common shop hazards and how to handle them, see the online version of this article at www.ccjdigital.com.