On speaking terms
Communication key to engine-transmission teamwork
Today’s trucks need a simple form of technology that communicates between the engine and transmission for the various multitorque arrangements that give drivers a powerful incentive to stay in the top two gears. More sophisticated communication is needed for fully automated transmissions.
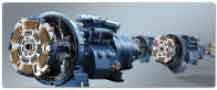
Scott Steurer, Eaton’s global manager of service and customer support, says it’s important for the engine and transmission to communicate with a multitorque setup. “We provide stronger bearings, and we may apply a different material or a harder finish for the gears that carry the extra torque,” Steurer says. The engine’s electronic control module needs to know the transmission’s gear so it won’t apply 1,750 lb.-ft. of torque in 8th gear if running a 1,550 lb.-ft. 10-speed designed to carry 1,750 lb.-ft. of torque in just the 9th and 10th gears.
On Eaton’s multitorque setups, the engine ECM handles the processing and knows the transmission’s current gear because of sensors on both the input and output shafts that generate a wave-type signal that varies with the speed of rotation. An SAE J-1939 data link carries the signals between the engine and transmission, and the ECM measures both frequencies and calculates the ratio between the frequencies of the signals; the ratios are preprogrammed to identify the top two gears.
Volvo Trucks North America uses the same basic arrangement for its Dual Torque and Eco Torque multitorque options, deducing the transmission’s gear with the same calculation, says Ed Saxman, director of powertrain.
More data has led to more intelligent shifts.
Since automation has developed, the amount of data communicated has grown over time. “We’re getting more and more data so we can make smart, truly intelligent shifts,” Steurer says. “An automated transmission doesn’t have eyeballs looking through the front grille, so it’s hard to anticipate what will happen the way a good driver does. So we need grade sensors, speed sensors and engine torque output measurements to try and make the right shift decisions.”
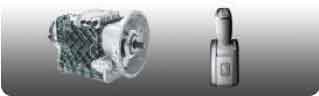
An automated transmission incorporates not only the input and output shaft speed sensors but also one that measures the rotating speed of a countershaft gear so the processor knows “what the front box is doing.” From there, by knowing the ratio between the rotating speeds of the input and output shafts, the sensor also can determine what is happening in the range box and, if applicable, the splitter. Another “ball switch” sensor lets the processor know when the driver has engaged reverse, which helps the processor determine what gear goes next.
But more is needed. The transmission processor also will receive information from both the throttle pedal – the driver’s input – and the engine’s processor. Information from the engine ECM, which determines fueling because of its preprogrammed torque and power curves, will enable the transmission processor to determine torque output.
A complicated business
Determining engine torque output can be a complicated business. “Understanding engine torque and driver input – what the driver is asking for – is essential if we are to give him good shifts,” Steurer says. “We have a large group that has been working with the engine companies to get information regarding the fuel maps so torque output at each rpm can be determined.”
Added next are vehicle speed and, on the latest designs, an “inclinometer” device that knows when the truck is on level ground, an upgrade or a downgrade. Knowing those things – especially driver demand and engine torque output – enables the transmission processor to be programmed to work in concert with the engine and know the operating conditions so it can anticipate what is going to happen and make smarter shift decisions going both uphill and downhill.
The holy grail
Steurer describes surface mapping technology as “the holy grail of gathering this kind of information” and believes the industry eventually will have complete mapping that can work in concert with GPS to allow the transmission to anticipate the need for power and torque as it varies with grade, effectively giving the transmission those “eyeballs looking through the front grille.”
Saxman says Volvo’s I-Shift also has its own processor with occasional authority over what is happening with the engine. If the engine is turned off with the transmission in reverse, the processor shifts the I-Shift to neutral before the engine shuts down; but when the key is turned back on, the indicator shows the transmission is in neutral, even though the shifter is in reverse position, ensuring the engine is started only when the transmission is in neutral.
Since the shift intelligence is in the transmission processor, that’s where shift decisions are made, and it is programmed differently for each engine because it needs to know the engine’s torque output under different conditions. The processor calculates the vehicle weight and grade; it can shift down one or even two gears at a time depending on the grade, and it calculates when the grade is so steep that it should not attempt a downshift. The I-Shift also has a grade sensor to measure the grade directly.
The transmission knows the throttle position and has a position sensor that tells the processor what gear is engaged. Communications are carried along a proprietary data link that resembles a large conduit between two offices so that information can be carried back and forth continually.
As for service, Eaton has a “Service Ranger” software program that can be installed on a laptop; the computer then can be plugged in to the underdash data plug using a special communication box and cable available from several suppliers. The technician then has access to active and inactive trouble codes, the number of times each code was set and help in analyzing the problem. He also can contact a call center for further assistance.
The technician also can read the codes via flashes on the dashboard’s driver display by turning the key on and off three times and using a card supplied with the vehicle for interpretation, but Steurer says the laptop software provides a real “repair strategy.”