Wheel end emphasis
Keep your hubs in condition – and your wheels on
To avoid a wheel-off nightmare, close attention to wheel ends is vital. For years, a technician’s skill and the proper tools and parts were essential. Wheel bearings require careful monitoring of oil levels, checks for grease leakage and periodic repacking with grease.
Before preset and unitized hubs were invented, a technician always had to take the bearing apart for greasing, to fix a leak or to renew parts, and then reassemble and adjust the bearing exactly to the proper preload.
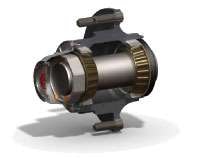
Bundled performance packages such as the Stemco Platinum Performance System (PPS) or Platinum Performance Plus System (PPS+) combine a traditional-style wheel end with premium components to create a long-life system.
The most critical issue always was setting the end-play to control the preload, and correct adjustments were elusive. When the bearings were too loose, seals were vulnerable to failure because of cocked parts, and the fleet would get complaints about steering performance; irregular tire wear also was a frequent result. Bearings that were too tight were subject to continuous excessive stress, resulting in premature failure after only a few weeks of normal running.
Preset and unitized
Today’s preset and unitized hubs present two different ways for technicians not to have to control all of the variables. In a preset hub, wheel bearings consist of two tapered roller bearings, with one handling stresses going in one direction, and the other handling the stresses in the other.
When the two are forced together with the right amount of tension, the wheel runs true because of a slight preload or bearing loading that prevents wobble. But the preload must not add too much stress to all the other loads the bearings already are carrying.
With the traditional system, the technician has to adjust the preload of the bearings directly with a fully adjustable nut that clamps them together with the force he sets. Most of the problems related to not doing this precisely were solved with the invention of preset bearings, which became an option in 1995. “You need a precision spacer to separate the bearings by the correct distance,” says Mark Stangl, manager of product management at Timken. “All the parts of the hub and bearings must be machined more precisely, too.”
Dana produces preset bearings with its LMS hubs, and the bearings must be machined precisely for everything to fit together at the right dimension. Once the bearings and spindle nut are installed, all the technician has to do is torque the spindle nut to the proper torque, and the preload will be at the optimum setting.
The spacer and bearing dimensions do almost all the work of determining the critical preload, a procedure that replaces the typical prior complex business of first seating the bearings by torquing the nut while rotating the wheel, and then backing it off a controlled amount and actually setting and measuring the end-play with a dial indicator.
The preset hub system also eliminates variation in operator performance. “It also takes much simpler tools,” Stangl says.
A unitized hub is a prepackaged bearing and seal assembly that eliminates most routine maintenance and only requires an occasional check for leakage and excessive end-play. But when it develops trouble, the entire bearing and seal assembly must be replaced.
With a preset design, the bearings and seals can be replaced as with the traditional design, and the assembly can be taken apart to look for spalling or other damage. Parts should be replaced only with those having the correct part numbers, and technicians should double-check those numbers, as bearings that won’t work can look exactly like ones that will. Quality seals also are critical.
Most large fleets today are using preset hubs. “It’s a matter of ‘pay me now, or pay me later,’ ” Stangl says. With adjustable systems, the potential for trouble is too high because it’s hard to ensure that it’s set right, so although initial costs and parts expenses for preset hubs are higher, fleets are paid back in reliability and longer life, says Steve Slesinski, director of global product planning at Dana Holding Co.
Old-school affordability
Stemco has a different approach, says Kevin Dillon, product manager, seals. “A traditional-style wheel end typically will be less expensive initially and may require more routine maintenance,” Dillon says. Bundled performance packages such as the Stemco Platinum Performance System (PPS) or Platinum Performance Plus System (PPS+) combine a traditional-style wheel end with premium components to create a long-life system. “These systems have an affordable upfront cost and require simple routine maintenance,” Dillon says.
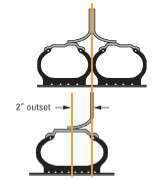
This diagram from Timken shows the shift in the load line when a two-inch outset wheel is used to accommodate a wide single tire.
Stemco also employs its own Pro-Torq spindle nut designed to simplify the traditional end-play adjustment procedure and to allow continued adjustment of end-play in small increments to compensate for normal wear.
To get fully adjustable systems to work, a dial indicator is needed to check end-play. “No matter how seasoned a technician is, they cannot determine end-play by feel,” says Sibin Luke, Stemco’s product manager, engineered products. Using proper seal installation tools also is critical.
Most seal manufacturers design their tools specifically with their seal geometry in mind, Luke says. “Make sure the right tool is available for the specific seal application.”