Let trannys do the tough work
Automated gearboxes take pressure off drivers
The first automated gearboxes shifted only between the top two gears, and while the second generation shifted between all the gears, it required the driver to operate the clutch to start out. The next step was competing methods of automating the clutch.
ZF’s FreedomLine, originally marketed by ArvinMeritor and the product of a regulated European industry accustomed to more costly equipment, achieved full automation with a processor-controlled air-powered clutch actuator. Eaton Corp., as part of a less regulated American industry that nearly always desires low-cost equipment, came out with a simple but effective automated clutch in its UltraShift. Eaton combined a sensitive centrifugal clutch that was purely mechanical, coordinated with processor control of engine throttling based on driver input and vehicle speed to make it work.
Automated transmissions are available for a variety of applications.
Not long after, Volvo and Mack each began marketing their own adaptation of a fully automated 12-speed gearbox, a design that was fancy in its control capability – including fully automated clutch actuation – yet simple in that it, like the FreedomLine, substituted computer control for the synchronizers other Volvo gearboxes use.
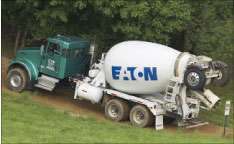
The UltraShift’s only real limitation was its restriction to normal highway truck usage because of how the clutch would behave when moving at a crawl. As a result, the company ultimately developed the Ultrashift Plus, which has a clutch controlled by an entirely electronic actuator and thus can engage fully at a lower speed when the driver needs to crawl.
The Ultrashift Plus is approved for use in on- and off-road applications such as concrete mixers. It also shifts more quickly between gears by declutching and using internal means to synchronize transmission parts more quickly than can be done via the decelerating engine.
Virtually every variety of Eaton Fuller transmission – even units like the 8LLs – has been automated, says Eaton’s Shane Groner, the company’s NAFTA product planning manager. Now the market is filled with automated gearboxes that can be specified for use in on- and off-road applications.
Automated applications
So which nonhighway applications are proving most suitable for the new generation of automated gearboxes?
Groner says concrete is an ideal application for the UltraShift Plus. “Not having to learn how to shift speeds the learning curve for a new driver,” he says. “It’s a much less intimidating environment for him. He can spend his time learning about the commodity itself and the handling of it during the delivery.”
Ed Saxman, director of Volvo powertrain for Volvo Trucks North America, says Volvo is selling I-Shifts into dump trucks, fire trucks, walking floor trailers, logging and other applications.
Whatever the application, an automated gearbox can improve fuel economy from 2 percent to as much as 30 percent depending upon the driver’s skill level and the duty cycle. Over the course of a long day, even a good driver who has the truck’s efficient operation down to an art can miss the occasional optimal shift point.
The results are even more dramatic with the less experienced driver who tends to accelerate under full throttle to governed rpm in every gear, impacting both fuel economy and driveline life. “Mack mDrive removes driver variability from the picture,” says David McKenna, the company’s powertrain products marketing manager.
Saxman says the Volvo I-Shift delivers a fuel efficiency advantage because “it’s always in the right gear at the right time.” Intelligent microprocessor technology allows the I-Shift to continuously monitor changes in grade, vehicle speed, acceleration, torque demand, weight and air resistance. “Automatically selecting the best gear for the engine also puts less stress on the driveline, so you can expect longer life and less maintenance,” he says.
Fuel economy depends on duty cycles and drivers, but a fleet that adopts automated gearboxes will see its average fuel economy move up as less capable drivers get better quickly, Groner says.
The reason UltraShift automation works is the high degree of integration between the engine maker and Eaton, Groner says. “We have the fuel maps for every engine, so every version of each transmission is specifically programmed for each different engine,” he says.
This extends to specific programming that reacts to multitorque engine arrangements that induce a driver operating a manual gearbox to stay in top gear, and the same thing happens when an automated transmission is mounted behind such an engine setup, giving the fleet a similar benefit from specifying it.
“An mDrive coupled with a Mack multitorque Econodyne engine affords the best of all worlds – remarkable fuel economy and grade-pulling power only when needed,” McKenna says. When a grade is encountered, mDrive holds the engine rpms to the lowest manageable value. The engine returns to the normal torque-mapping strategy when the hill is crested or the driveline senses zero torque.
Saxman says Volvo’s Eco-Torque ratings are becoming more popular, comprising about half of all Volvo engine sales. Eco-Torque ratings are sold specifically to improve fuel economy, not to allow the use of “less-than-full engine torque-rated” transmissions, he says. The I-Shift transmission has the hardware to be compatible with all Eco-Torque ratings.
Fatigue is another issue. “Every driver will be fresher at the end of his day,” Groner says. “And two eyes on the road, two hands on the wheel can enhance safety.”
Drivers that have spent 10 hours on the road are reporting that they’re much more relaxed than they would be with a conventional manual transmission, McKenna says. “This is especially apparent in rolling country and on twisting roads or interstates,” he says.
Maintenance matters
Maintenance is always an issue, and a fleet manager’s first thought might be that with a more complex piece of hardware, there may be more maintenance. However, automated gearboxes have the ability to preserve hard parts like clutches and drivelines – and are more likely to reduce maintenance costs than to raise them since they never slip the clutch by starting in the wrong gear or use a higher clutch engagement rpm than necessary. And engaging the clutch via electronic control is good insurance against abrupt driveshaft-twisting starts.

The hill starting aids that keep the truck from drifting back when starting on a hill take that principle a step further and also remove the inducement for the driver to hold the truck on a hill with the clutch. “Our experience regarding maintenance is that I-Shift requires significantly less clutch maintenance than manual transmissions,” Saxman says.
McKenna says the mDrive also yields lower maintenance. “Electronic control greatly extends clutch life,” he says. “There is less stress on the driveline in general.” An easily accessible lube oil filter and easy-to-see oil level sight window also reduce maintenance time and cost and increase vehicle in-service uptime.
With Eaton transmissions, the clutch release bearing’s greasing interval has been extended from 25,000 to 50,000 miles, and the zerk fittings have been moved to the outside of the bell housing so they are easier to reach and will take less time to grease, Groner says.
As far as repairs go, Groner says what needs to change most is not repairs to the transmission itself, but attention to basic electrical system maintenance. He recommends careful attention to battery spec’ing, periodic battery load testing, alternator output checks and maintenance of wiring and both positive and ground connections.
“A transmission with processors and electrical actuators is bound to work better if every item always gets full voltage,” he says.