Today’s technology speeds driver-office interaction, workflow
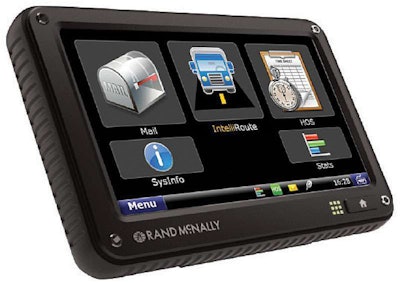
Until recently, new drivers for TransAm Trucking were being trained for 2½ hours on how to record hours of service properly on paper logbooks. Now training takes 15 minutes, and no paper is involved. “The learning curve is much less,” says Russ McElliot, president of the Olathe, Kan.-based company.
Similar to most commercial driving positions, working for TransAm has become more complex. Drivers face new regulations and are expected to meet higher performance standards – but that doesn’t mean more training time. At TransAm, the opposite has been true since 2008 when the company began installing a new in-cab computing platform from Blue Tree Systems.
Today, a driver turns on the ignition and sees his performance metrics from the previous workday. Color-coded bar charts give insight into how his mpg, speed, rpm and engine idle time compare to the current fleet average.
“We simplify some things for the driver to make the process more accurate.”
– Randy Boyles,
PeopleNet vice president of tailored solutions
TransAm began using this daily reporting system last November. Since then, drivers in the bottom 20 percent of mpg have improved by 0.1 mpg on average. Assuming the trend holds, McElliot estimates an annual savings of $1.8 million in fuel.
“It gives drivers more real-time information,” he says. “Everyone does better with instant feedback.”
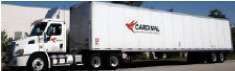
In December, TransAm converted to electronic logs from Blue Tree Systems. A feature called HOS Advisor is available at the press of a button. Drivers have live information on remaining hours and advice for what duty status will yield the most productive use of their remaining time.
“(HOS Advisor) makes it much easier for our support staff,” McElliot says. “The interaction that drivers have with safety and compliance since we went to HOS Advisor has been reduced by half.”
Besides simplifying compliance, drivers use the technology to breeze through pretrip inspections, plan routes and communicate with the office electronically. Drivers also can view settlement and payroll details and track their progress through required training.
Just as consumers are replacing personal computers with smartphones and tablets, the transportation industry is embracing next-generation technology to increase driver productivity. In particular, touchscreen displays and custom-tailored workflow applications are changing how drivers interact with technology to accomplish more with less effort.
Forms control
In the past, communications between the office and cab were limited to voice and free-form text messaging. To improve efficiency, fleets and technology providers developed specific message sets or “macros.” When a driver arrives at a pickup location and presses an “arrive” key, he would enter data such as a bill-of-lading number and piece count, and send the message.
This generic style of messaging created problems for Cardinal Logistics and its drivers. In the past, Cardinal had to develop custom applications and use a variety of onboard computing systems for each project as some customers want electronic signature capture at the point of delivery, while others also want to capture specific details such as trailer temperature and exception codes. The company’s programming and training costs were high. “If I moved equipment between two different locations, the way the macros were set up didn’t match the way the projects worked,” says Clay Holmes, chief information officer.
Cardinal decided to create a software application for vendor-neutral Windows Mobile devices. Its application, Cardinal Activity Tracker, includes a Dynamic Workflow feature to present drivers with customized forms that match the setup, or profile, of each customer in its dispatch and enterprise software system.
With a few mouse clicks, one set of customers can be set up with electronic signature capture for proof of delivery. For another set of customers, drivers scan barcodes on packages at pickup and delivery and capture load temperature. Each of these unique workflow requirements are sent to the CAT application on mobile devices as soon as drivers download their daily routes.
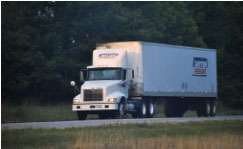
Through integration with a third-party navigation system, CAT also provides turn-by-turn directions to each stop so that deliveries must be made in sequence for employee drivers; for contractor drivers, the setting is turned off to allow nonsequential deliveries.
At each stop, Dynamic Workflow guides drivers through the steps to complete and provides dispatchers and customers with real-time detailed order and shipment information.
PeopleNet’s Pacos automated workflow system stores planned route information on the onboard system through integration with fleet dispatch software. The onboard unit compares current location with the stored locations of each stop. Pacos automatically updates the load status in the dispatch system as the truck arrives or departs from a planned stop within a prescribed radius or geofence.
Besides automatically capturing arrivals and departures, Pacos prompts drivers to complete work forms for each event. Work forms can be customized with a Decision Tree tool to map the sequence and logic for the data entry.
“We simplify some things for the driver to make the process more accurate,” says Randy Boyles, vice president of tailored solutions for PeopleNet.
Pacos can be customized to include documents or videos that are presented automatically to drivers as part of the location-based workflow, such as instructions for what services a driver is to perform at the loading/unloading site.
Auto verification
Instead of drivers and fleets sending text messages back and forth, drivers now are able to query their mobile devices directly. This time savings is possible through a mini-database, replicated from the office database, being loaded onto the device and updated through wireless communications.
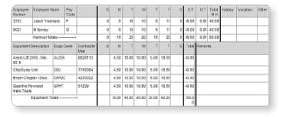
The data replication model enables instant validation as drivers input data such as bill-of-lading numbers, load weights, piece counts and trailer numbers. Fleets also can provide drivers with instant access to driver-related information such as year-to-date earnings or the status of a toll reimbursement.
CarrierWeb recently added a driver workflow application to its CarrierMate mobile communications system. Through integration with dispatch software, the application captures the required information for each shipment. Using server-based architecture, the in-cab device is able to verify instantly that the driver has entered the required information before sending a message, says Norm Thomas, vice president of professional services.
Less-than-truckload carrier Dayton Freight has invested heavily in office technology, but before 2010 it lacked a way to automate information flow between the office and drivers.
Cell phones were used for two-way radio communications, and drivers used paper forms to complete vehicle inspections and capture work process details such as arrival and departure times, shipment weights and piece counts for pickups and deliveries.
After drivers completed their daily routes, clerks entered work data from the paper forms into the company’s capacity management system.
In August 2010, the company adopted Qualcomm’s MCP200 platform and Circle of Service Workflow application. Dayton Freight uses Workflow to create electronic pre- and post-trip exception forms to categorize, rate and add vehicle defect alerts in the fleet’s maintenance software program. The workflow application also integrates with Dayton Freight’s dispatch and other office systems to capture load details from specially designed work process forms.
“Our pickup information is much more accurate now because it is near real time,” says Anthony Rocco, vice president of operations. “Now we receive this data at the time of pickup, allowing us to plan transportation runs earlier in the day and detouring freight into a hub.”
As part of the implementation, Dayton Freight tethered a barcode scanner to the MCP200. Drivers now scan tracking numbers on barcoded PRO labels that they affix to shipping documents. Scanning improves accuracy by eliminating manual data entry errors.
The company also input company service point locations and ZIP codes into the work process forms stored in the MCP200 devices to validate data entry by drivers. When a driver enters a destination ZIP code, the software asks the driver to confirm the city. This instant verification enables Dayton Freight to get accurate shipment data immediately so load planners can begin routing freight to the correct service center destination.
Since converting to this electronic workflow, Dayton Freight has seen its stops per hour increase by about 3 percent and has reduced data entry labor.
Intermec, a provider of rugged mobile computers, has developed features that help drivers automate data collection. Its Verdex (verify data extraction) tool has expanded the use of barcode scanning and automatically can capture and verify machine-printed information such as addresses from paper forms.
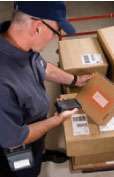
Intermec’s CN50 and CN70 devices were designed for transportation applications. Drivers for couriers and express delivery services typically have a lot of key entry at the point of pickup. The consignee’s address must be entered into the mobile computer to update the office systems.
With Verdex, a driver could aim an Intermec device at a bill of lading to extract the address into the device; the software then would validate the address with an onboard database in a matter of seconds.
Intermec computers also have an option called Enhanced Mobile Document Imaging (eMDI) that can capture images of documents at the time a driver steps on the customer’s dock to make a pickup or delivery.
Self-assessment
Fleets using the latest mobile computers are not limiting driver workflow applications to data entry. As part of the workflow routine, drivers are able to monitor and improve performance without management intervention.
RandMcNally’s TND 760 and Truck PC products have a Stats feature. By touching an icon, drivers can see an onboard scorecard of fuel economy, idle time, hard braking, engine overrevving and other measures. Data can be tracked by day and month.
“The driver can see the same information that their management sees,” says Mason Meadows, director of product management.
CarrierWeb’s mobile communications system displays a driver’s idle time, fuel economy and speed compliance. Drivers also can go to a Website to see a more detailed performance review and compare themselves to other fleet drivers.
PeopleNet’s in-cab display has a real-time driver scorecard. The company plans to add new enhancements to its BLU2 and Tablet platforms to make it easier for fleets to send integrated performance reports to drivers as a PDF and other file formats. PeopleNet’s Tailored Solutions group has a Software Development Kit that customers can use to create applications that integrate with office systems for drivers to have in-cab access to payroll information and other corporate data.
J.J. Keller’s Web-based Encompass fleet management system combines a low-cost onboard computer with a mobile app for Windows Mobile and Android devices. The app allows drivers to capture vehicle inspections, logs and fuel receipts electronically.
The Encompass system displays drivers’ fuel and safety performance. Fleet managers can e-mail these reports to drivers’ mobile devices, but most customers now are printing the reports and meeting face-to-face with drivers, says Amy Daley, ASP product manager.
J.J. Keller’s roadmap for Encompass includes integrating the company’s online driver training and a Web portal for drivers to monitor their fuel, safety and productivity performance.
Xata Turnpike includes driver logs, vehicle tracking, vehicle inspection reporting and engine diagnostics and telematics. The Turnpike driver app, tpMobile, runs in an open software environment on Android, BlackBerry and Windows Mobile platforms, allowing companies to use a number of third-party apps to create a richer driver experience.
“We have customers who e-mail hazmat permits or driver scorecards directly to drivers on their device,” says Charlie Mohn, director of product development for Xata.
Renn Transportation, a 50-truck fuel hauler based in Grenada, Calif., began using Xata Turnpike on smartphones in 2009. Drivers start their workday by logging into tpMobile with a four-digit number; next, they complete a pretrip inspection by using the app to designate items with a mechanical or safety issue.
“It does everything else for them,” says Steven Boyle, director of operations and safety. Once the pretrip inspection is complete, Xata Turnpike begins tracking drivers’ hours of service. A driver’s on-duty status automatically changes from not driving to driving, and vice versa, as the app detects motion or lack of it.
Renn accesses Xata Turnpike’s driver scorecard online. Boyle reviews exceptions with drivers regularly for speeding events, engine overrevving, excessive idling and hard braking. “Drivers are getting more conscious and operating as efficiently as they can,” he says.
Renn plans to deploy Xata Turnpike on tablet devices to expand the options for data capture and back-office integration with mobile driver apps. “Our biggest goal is to get away from smartphones to a larger tablet and integrate payroll, hours of service, vehicle inspections and everything else electronically,” Boyle says.
Using technology that makes drivers more efficient also benefits safety by providing more time to drive and limiting distractions.
Navigation, electronic logs among preferred features
This past summer, Jimmy Keller was hired by Rand McNally to drive for its Moving America Tour. Keller, a veteran driver, had his first experience using what a growing number of fleet drivers now have in their cabs. With an earlier mobile computing system, Keller needed to carry a “cheat sheet” to learn its many functions and soft keys. Technology has changed a lot since.
During the Moving America Tour, Keller drove a truck equipped with two fleet management systems from Rand McNally: the TND 760 Fleet Edition and TruckPC. Both systems have touchscreen displays – a feature that Keller says makes it simple for any driver to use navigation – as well as electronic logs, messaging, performance monitoring and other features designed to make a driver’s work easier.
The TND 760 combines navigation, electronic logs and mobile communications for less than $800. The Truck PC is a full-featured system that adds in-cab scanning, backup cameras, tire pressure monitoring and other options.
Navigation was the most beneficial feature to Keller. At the start of each day and as the day progressed, he knew what time he would arrive at each stop so he could plan in advance how to use his remaining driving hours. Another feature Keller rated highly was electronic logs, which gives drivers and fleet managers real-time visibility to the same information.
“It keeps everyone on the same page,” he says.