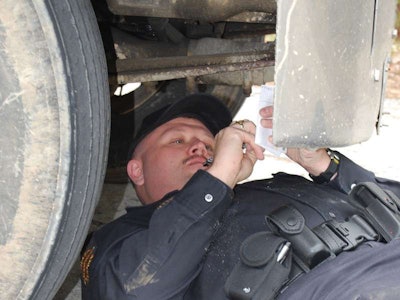
As part of the ongoing “All Hands on Deck” series, this section details how modern tools can be used during pre- and post-trip inspections to find and fix issues that could dock a carrier’s or driver’s CSA score if found during a roadside inspection. Part 1 covers how fleets are using modern tech to schedule and perform prevenative maintenance — see it here.
Inspections
Besides using technology to fine-tune PM schedules, companies can create more accountability for defects that could have been found and repaired prior to becoming violations.
AIM NationaLease, a full-service lease provider, maintains a fleet of more than 7,000 vehicles. The Girard, Ohio-based company also provides dedicated truckload services through AIM Integrated Logistics, a division that operates more than 400 trucks. AIM NationaLease’s maintenance program has an impact on the CSA performance of many more fleets than its own.
More than ever, the company is holding technicians responsible for “the little stuff” – such as broken marker lights or brake hose chaffing – that tends to be the most frequent violations. “We focus on zero tolerance,” says John Reed, chief information officer.
AIM NationaLease has fine-tuned an electronic checklist in the company’s Enrich fleet maintenance software from Richer Systems. Technicians complete the list each time a truck is brought in for PM service – about four times per year.
The checklist includes all items that are in the U.S. Department of Transportation’s federal annual inspection form to help ensure compliance. If a vehicle receives a violation from a roadside inspection, the company uses a “repairs between PMs” report to determine if the violation could have been caught during the last PM.
To better manage CSA performance, Venezia Inc. has implemented a “checklist” function in its TMT fleet maintenance software from TMW Systems. The Pottstown, Pa.-based bulk transporter has computer workstations in each service bay. As technicians perform PM services and inspections, the checklist function helps hold them accountable for finding defects and documenting repairs, says JP Venezia, maintenance systems and food compliance manager.
In the event of an onsite DOT safety audit, fleets can use maintenance software to prove that inspections were completed on schedule. Any inspections where a fault was noted can be tracked against the unit, along with the repairs.
“From historical records, you can look at an inspection and see the outcome – all of the subsequent work orders related to that,” says Vince Bull, director of marketing for fleet maintenance system provider Data-Dis. “That’s the advantage from a CSA standpoint.”
Electronic inspections
Under CSA, drivers’ pre- and post-trip inspections are valuable components of fleet maintenance software systems. Before CSA, drivers might have “pencil-whipped” inspection reports and gotten away with it. Now, because violations also count against drivers’ CSA scores, they are paying closer attention to details – and expect repairs to be made in a timely manner.
New technologies and features can help fleets and drivers streamline driver vehicle inspection reports. The technology removes the flow of paper between drivers, fleet managers and the shop while helping fleets create an audit trail and hold people accountable.
In 2010, Veolia Environment Services North America adopted Zonar’s electronic fleet management systems in its Electronics Recycling Division. The Phoenix-based ERD operates a mixed fleet of 33 tractors with dry van, flatbed and tanker trailers.
The Zonar system includes an electronic vehicle inspection reporting system for pre- and post-trip inspections along with an onboard telematics platform. Zonar’s EVIR uses radio-frequency identification tags. The tags, placed on vehicles in critical inspection “zones,” contain information about their location on the vehicle, the components to be inspected and the identity of the vehicle or trailer.
Veolia drivers place the Zonar 2010 handheld reader within inches of each tag and indicate the condition of the components within the zone with one-handed push-button responses. When a defect is discovered, the driver selects a description from a predefined list and indicates if the vehicle is safe to operate.
When the inspection is complete, drivers place the reader into the vehicle mount. The information is transmitted to a secure database that the fleet manager can access from a Web browser via Zonar’s Ground Traffic Control Web-based fleet management software.
“We’re catching more problems before they leave to go on the road, and we’re identifying potential problems and fixing them before we go out,” said Michael Bomgardner, ERD fleet manager.
As a result of using Zonar to identify and repair mechanical problems early, the division has reduced the time its vehicles spend in the maintenance shop by 13 percent, resulting in an annual savings of about $28,000 due to improved maintenance shop efficiencies.
Since adopting the Zonar system, the division’s percentile scores in nearly all of CSA’s BASICs were reduced by more than a third, which also contributed to lower overall company scores, Bomgardner said.
With all the choices in computers and software technology to collect, manage and disseminate CSA information, it might be easy to overlook how mechanical systems can round out your efforts to improve CSA performance. As an example, the Super MUTT trailer inspection system can detect future violations long before they surface in CSA. With a quick diagnosis, fleets can also speed repair time and increase asset utilization.