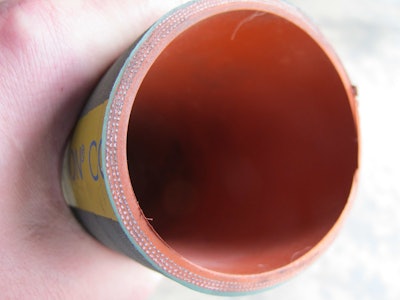
Today’s sophisticated vehicle systems receive the lion’s share of attention, and while some of those high-maintenance items can be aggravating when they fail, the vehicle still might remain operable to some degree.
If a truck runs out of diesel exhaust fluid, an irate driver can limp along the highway, eventually getting to a truck stop and refilling the DEF tank. But if a relatively low-tech belt or hose goes, that driver isn’t going anywhere until a tow truck or technician arrives.
Overlooking belts and hoses is an invitation to disaster. Most fleets target them as part of scheduled preventive maintenance, and good technicians know to change out belts or hoses if even a hint of trouble is spotted.
But truck engines are hellish environments, and good maintenance is no guarantee against premature failure. A fleet’s best defense is coaching drivers to target belts and hoses during pre-trip inspections to spot potential problems before they become service failures.
How to inspect hoses
Compared to the chemistry set required to test a truck’s coolant mix, checking the hoses and fittings in the cooling system is a relative snap. The primary diagnostic tools are with a driver all the time: his hands.
“Coolant hoses degrade from the inside out,” says Frank Burrow, manager of warranty and customer support at Red Dot, a supplier of A/C systems and components for heavy-duty vehicles and off-highway equipment. “At a glance, there’s rarely an obvious sign of wear and tear. Palpating a coolant hose is one of the simplest ways to gauge its condition.”
Coolant hose deterioration is caused by an electrochemical reaction between the coolant and different metals in the system such as steel clamps, a copper heater core or a cast-iron head. Tiny cracks develop in the tubing, typically near the hose ends, allowing coolant to reach and cause wear to the reinforcement yam.
As the hose degrades, it sheds debris into the coolant. “You have a weak point in the hose, and you have foreign material circulating through the heater core,” Burrow says. Any places the hoses or fittings are fastened, clamped, connected, bent or otherwise secured are potential wear points; this also applies to places where hoses are not clamped or supported but should be.
Burrow says that to inspect a hose, turn the system off and squeeze the hose near the ends, between your thumb and fingers, to gauge its firmness. If the hose feels spongy, it’s weak and should be replaced.
Manually examining the hose also can pick up scruffs, gouges, bulges and abrasions that are hard to see. Feel for moisture, seepage or excess dirt and grime around fittings, clamps and connections.
“Obviously, touch and feel aren’t going to replace the service equipment of a qualified technician,” Burrow says. “But if you’re an owner-operator or a mechanic doing a routine PM, they’re a good first step in the troubleshooting process.”
Other tips for checking coolant hose:
- Installation: Coming off the reel, consider the hose’s natural curl as it’s unspooled. Coolant hose should be installed so the bend is in the most relaxed position, not pulling away from the fitting. “That load, however slight, is an opportunity for pressure to build and a weak spot to form,” Burrow says.
- Clamps: There can be as many as 50 hose-clamp applications on a heavy-duty vehicle, as well as a variety of different clamping systems. For the cooling system, use a clamp that can provide uniform tension and sealing – especially in low temperatures – considering the hose type, size and material.
- Some clamping systems have specific torque ratings and require special tools for installation and removal. While screw-type clamps are simple and easy to find, more complex torque-specific clamps aren’t as susceptible to overtightening and do a better job at providing constant equal pressure on the hose material.
How to check belts
The primary inspection should focus on premature wear, which usually appears on the belt’s outer edges. Because of the high speeds of moving engine belts, the outer edges are sensitive to small misalignments in belt routing. Any lateral play introduced to a rotating belt quickly can lead to wear and eat into the belt’s main body.
Drivers should be alert for any signs of fraying on the outer edges; although the belt itself must be replaced, this type of wear probably also indicates a bigger problem that needs to be addressed.
Older belts that have slipped through multiple PM inspections usually show their age with cracks in the top, sides and bottom. Belts themselves should be supple and flex easily, so any brittle belt that cracks and resists flexing soon will fail and should be replaced immediately.
Proper belt tension also is critical. On modern engines, spring-loaded belt tensioners automatically keep belts at the proper tension, and they also help eliminate overtightened belts that can place added strain on bearings, leading to eventual misalignment or failure.
Check tension by pressing down on the belt to gauge its “give.” While some play is normal, look for movement of about ¼-inch up or down; such excessive play is usually a sign that a belt tensioner is failing and needs to be replaced.
The bottom line? Belt and hose inspection is vital to a truck’s productivity. The good news? Making sure that these components are in good working order is quick and easy.