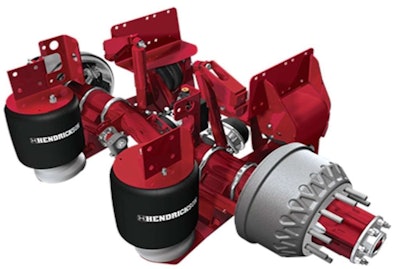
Heavy-duty truck suspensions have a thankless task. If they work correctly, they largely are forgotten in day-to-day fleet operations. It’s not until a suspension fails, or a driver starts complaining about his back, that many fleets pause to consider their suspension specifications.
But there are many good reasons for fleets to review their suspension specs and consider changes to better meet their application requirements as new designs are developed to complement today’s equipment trends. Today’s automatic lift-axle and tag-axle control systems can provide savings on tire life, fuel efficiency and vehicle downtime.
“Fleets should take the time to review the spec to be aware of any new efficient products that might not have been around when they first spec’d the suspension,” says Mike Lambie, marketing department manager for Meritor Wabco. Lambie suggests fleets should examine their operations to see if conditions have changed in any meaningful way.
[gtblockquote quote_text_size=”16″ quote_text_style=”normal” quote_text_color=”#ADADAD” border_size=”4″ border_color=”#E6E6E6″]“Fleets should take the time to review the spec.” – Mike Lambie, marketing department manager, Meritor Wabco
“Maybe you’re now doing more drop-load operations,” he says. “From there, it’s very simple to determine if there are new suspension technologies available that would make this operation more efficient.”
In both on-highway and vocational applications, weight savings are critical for both improved fuel economy and greater payloads. “The correct suspensions can save hundreds of pounds on a vehicle,” says Ashley Dudding, director of engineering for Hendrickson.
With emissions and brake regulation changes, many tractor configurations have been forced to go to higher axle capacities such as 13,200 or 13,300 pounds, which frequently drives the cost up, Dudding says.
Spec’ing weight savings in the steer position can keep the front-axle spec at a lighter 12,000- to 12,500-pound rating, and for vocational trucks, rubber suspensions can offer weight savings over conventional steel spring suspensions, “with obvious benefits to the fleet’s bottom line,” she says.
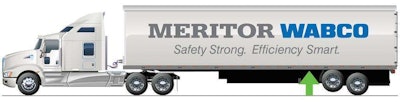
The increased popularity of 6-by-2 axle configurations in on-highway applications has led some fleets to consider changing axle specs, Dudding says. “It is well accepted that 6-by-2 configurations save weight and provide a fuel economy benefit,” she says. “However, application of this concept is limited by traction concerns, particularly when bobtailing or partially loaded.”
To work around this limitation, Hendrickson engineers have developed what Dudding calls a “liftable-forward” tandem axle – an Optimaax axle designed to allow the forward axle in the tandem to be lifted automatically when loads are light.
“Picking this unsprung weight up greatly enhances traction and is an enabler for 6-by-2 applications,” she says. When empty – such as on a return trip on a bulk haul – or lightly loaded, the tractor can operate as a 4-by-2, which eliminates the rolling resistance of the second axle as well as thrust and tandem scrub.
Likewise, Lambie says a new automatic lift-axle control system offered by Meritor Wabco assists in increasing vehicle efficiency in a similar fashion.
“Automatic lift axles reduce the probability of driver error that is typically associated with manual lift-axle systems that can overload an axle or not take advantage of fuel efficiency opportunities when they present themselves,” Lambie says.