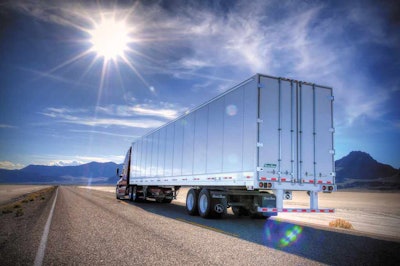
Without a trailer, a tractor is meaningless. A trailer, the argument could be made, is the piece of equipment that actually brings revenue in for a fleet. While it’s easy to dismiss a dry van as simply a “box on wheels,” the reality of trailer design is a never-ending series of compromises between cargo space and unit weight.
Today, as savvy fleet managers understand that any money saved in fuel costs adds to their bottom line, new aerodynamic aspects are being added to the trailer design mix. Also, new technologies – such as telematics, GPS tracking and real-time logistics information – are pushing trailer OEMs to reevaluate longstanding designs and look at how trailers will be used in the future in a new light.
Strick Trailers in 2011 was selected as Daimler Trucks’ trailer partner for its 2015 SuperTruck project, a five-year development process in conjunction with the U.S. Department of Energy and other leading industry manufacturers and suppliers. Daimler’s highly sophisticated and sleek vehicle was showcased in the Freightliner booth at this year’s Mid-America Trucking Show.
“The opportunity to work with the best engineering minds in the business has been a privilege and a gift,” says Charlie Willmott, chief sales officer with the Strick Group. “We have learned much about what to look for and where to begin. There is no question that the trailer is the ‘Final Frontier’ for major aerodynamic improvement in the combined truck-trailer configuration.”
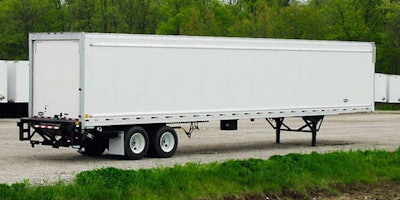
Willmott says Strick now is focused on key areas where the biggest improvements can be made quickly and easily. “It is a lengthy, expensive and full-enterprise process of innovation, design, build, test and refinement, but the end result will be far superior to today’s van products,” he says.
Wabash National operates under the belief that it has a responsibility to provide equipment that helps its customers be as successful as possible in today’s ever-changing operating environment, says Dick Giromini, president and chief executive officer of Wabash National.
“That includes seeking ways to continually enhance reliability, performance and durability, all while assuring the lowest total cost of ownership,” Giromini says.
Great Dane Trailers always has designed its products to respond to the specific needs of its customers, so evolving to incorporate current customer preferences and evolving technologies is nothing new for the company, says Charles Fetz, vice president of design and development. Regarding the impact of regulatory demands, Fetz doesn’t believe that regulations in general drive trailer design to a major degree.
“But they can provide additional challenges, since many proposed regulations require tooling, material or process changes for OEMs,” he says. “These can be both expensive and time-consuming to implement, which is why manufacturers generally like to see as much time as is reasonable to implement those as a result of regulatory changes.”
While Giromini says fuel economy regulations tend to get all the headlines, other mandates also actively shape the industry’s research and development efforts, such as the pending 33-foot twin “pup” trailer legislation that would extend the length of a standard pup trailer. “We are already prepared to build to a 33-foot standard,” he says. “If passed and signed into law, we can respond to customer needs immediately.”
On the manufacturing side of the equation, there also is pending legislation for eliminating or limiting certain foam-blowing agents in reefer insulation, specifically hydrofluorocarbons. Giromini says substituting these blowing agents could alter the trailer’s design to meet long-term efficiency and weight standards.
Integrated aerodynamics
As fuel economy became a greater priority for fleets, trailers lagged markedly behind tractors in terms of aerodynamic efficiency improvements. Aftermarket suppliers moved quickly to fill a new product niche by offering add-on aerodynamic devices, and OEMs say a more integrated approach is coming soon.
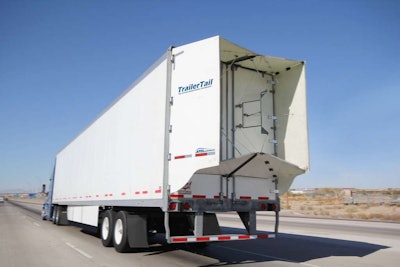
Giromini says that with the recent announcement of Phase II of the U.S. Environmental Protection Agency and Department of Transportation’s proposed fuel economy and greenhouse gas regulations, the trailer is becoming a more significant part of the overall equation.
“Obviously, designing a trailer with a lower coefficient of drag results in higher fuel economy and less GHG emissions for the tractor-trailer combination,” he says. “Additionally, we are constantly looking at the balance between weight and design.” About 60 percent of fleets today are in weight-sensitive applications, Giromini says. “This drives our ongoing efforts to optimize trailer weight to improve freight efficiency while increasing durability and corrosion resistance.”
Willmott says Strick looks at current industry and regulatory demands as design improvement opportunities for trailer OEMs. “The EPA’s pending GHG2 regulations are destined to force dramatically improved fuel efficiency over the next decade,” he says. The National Highway Safety Transportation Agency’s recent focus on key safety enhancements such as side underride guard and roll stability also are current design considerations.
At the same time, Willmott says, added pressure is being applied to trailer manufacturers from the free-market side of the equation.
“Fleets are pushing us hard for lowering fuel, operating and maintenance costs while simultaneously looking for increased payload productivity in an environment of increased highway traffic and growing driver shortages,” he says. “There are plenty of trailer design forces at work today. The real question is how do trailer OEMs respond to these drivers with satisfactory and compelling solutions? The answer is we each must respond in order to remain relevant in the market.”
Fetz sees a high degree of variability in today’s aerodynamic trailer designs. “Some trailers are quite efficient, but without devices or designs to enhance their aero performance, they are not what I could consider to be aerodynamically efficient,” he says. “The challenge is determining what can and should be done based on a fleet’s specific operational requirements. A solution that works for one fleet might not help another.”
As an example, Fetz says today it’s easy to add an aerodynamic skirt on a dry van trailer and get an instant 5 to 7 percent improvement in fuel economy, as well as improved drag reduction.
“That’s at 65 mph on a test track, though,” he says. “In actual operations, however, fleets typically report about half of this degree of savings in fuel economy. This is because no fleet can run 65 mph all of the time – they average something slower.”
Also, Fetz says, many fleets don’t benefit as much from aerodynamic add-ons due to short-haul distances or slow operational speeds in pickup-and-delivery operations, whole others can’t run skirts at all due to their specific equipment needs or operational profile.
“Today’s typical dry van trailer is aerodynamically equivalent to flying a cardboard box from New York to Chicago,” Willmott says. “There is still plenty of room left for significant efficiency and productivity design improvements to be made. The current bar is set pretty low.”
Willmott cautions fleet managers to remember that trailer aerodynamics are a mixed bag and can make pinning down a mpg improvement difficult. “Add-on devices add weight, initial cost and long-term maintenance responsibilities,” he says. “Each of these factors raises the bar for the investing carrier to find a real return.”
Fleets first have to determine basic information such as average speed and length of haul. “From there, simple mathematics determines if and when the benefits of those devices will ever materialize,” Willmott says. “On the other hand, adding aerodynamic features inherent or integrated into the design of the trailer itself without adding significant weight or cost can be a win-win every time.”
The primary factors and limitations for integrated trailer aerodynamics are driven by customers’ needs and preferences, Giromini says. “Trailers are designed to move freight as efficiently as possible,” he says. “Modifications from the current optimized design would result in reduced cargo capacity or would require size and shape legislation to change.”
To that end, Giromini says, Wabash’s wind-tunnel testing results indicates its van trailers have been engineered to maximum aerodynamic efficiency while not compromising cube capacity. “Rounded front corner posts and smooth transitions at the front contribute to aerodynamic efficiency,” he says. “Although enhanced aerodynamic designs are certainly attainable, they come with interior cube reductions that may not be practical for fleets.”
In most cases, Giromini says, add-on devices work well to maintain maximum internal cube dimensions while increasing aerodynamics. “We recently introduced a new SmartWay Elite option package that provides up to a 9 percent improvement in fuel efficiency,” he says. “Used in conjunction with low-rolling-resistance tires, this suite of options could provide greater than a 10 percent fuel savings for our customers. Opportunities may exist to integrate many of these solutions into the standard design of the trailer in the future.”
Still, Giromini says, the last chapter on trailer aerodynamics has yet to be written, and new concepts and approaches are being tested continuously by OEMs. He cites recent tests showing that lowering the trailer’s rear while at road speeds has been shown to improve aerodynamic performance with external aerodynamic devices.
“It is possible to achieve multiple ride heights with special air-ride suspensions,” he says. “This is an area that shows some promise. However, feasibility and application need to be further understood. In some applications, it is possible to lift an axle to reduce rolling resistance and tire wear.”
The never-ending weight battle
“Unlike aerodynamic add-ons, weight does not depend on external conditions to deliver fuel economy benefits for fleets. Saving weight in trailer design reduces drag and saves fuel every time, every day, empty or loaded.”
— Charlie Willmott, Strick Group
The battle to save every single ounce of unnecessary weight is one that trailer OEMs have been fighting since their earliest days. While the knee-jerk reaction is that reduced weight equates to more payload, there’s actually much more going on, Giromini says. “This effort has been ongoing for years within the trailer Industry,” he says.
As a result of years of research, development and implementation, today’s standard design is 1,000 pounds lighter than trailers produced just 10 years ago while actually being stronger and more durable, Giromini says. “To further advance the science, we are currently designing structural components with advanced high-strength steel and exploring applications of composite materials in various nonstructural areas.”
When trailer OEMs look at weight, another important consideration is the immediate impact on a fleet’s fuel economy numbers. “Unlike aerodynamic add-ons, weight does not depend on external conditions to deliver fuel economy benefits for fleets,” Willmott says. “Saving weight in trailer design reduces drag and saves fuel every time, every day, empty or loaded.”
But simply using lightweight materials to build trailers doesn’t work. “If you build the trailer too light for the intended service and it breaks or wears out in half the expected life, that’s a problem,” Willmott says. “The key with trailer weight is to design carefully to the needs of the intended service, and then stick to that service range without exception.”
Willmott cites paper rolls, which are a tough payload for van trailers. Once loaded, the rolls normally are well within the standard van’s static load capacity of 50,000 pounds. However, depending on the size of the rolls and the clamp truck used to load and unload, the dynamic load under the footprint of the clamp truck’s front tires can exceed the normal dynamic floor load rating by as much as 100 percent.
“If a trailer is not properly spec’d for this kind of service, it becomes an acute economic and safety risk to both the carrier and shipper,” Willmott says. “The problem is that saving empty trailer weight and properly spec’ing for heavy loads can be contradictory and mutually exclusive. At Strick, we emphasize working with the customer in depth to understand the characteristics of the intended service before recommending the optimal weight-versus-durability spec combination. In that regard, the possibilities are almost endless.”
Fetz agrees, noting that while Great Dane does everything it can to reduce overall trailer unit weight – taking into consideration everything from material improvements to manufacturing redesign – there are tradeoffs. “These efforts cost money, and many customers can’t reliably calculate ROI from weight reduction, so they are often hesitant to pay for improvements they can’t quantify,” he says.
To work with fleets and provide the widest range of weight reduction solutions possible, Great Dane offers lightweight features and components as options and tries to incorporate them into its standards wherever its designers can. “We balance the use of aluminum, high-strength steel and composites versus cost and durability,” Fetz says. “We do a lot of research, development and testing to offer good solutions, and trailers have been getting lighter and, at the same time, longer-lived.”
Telematics and tracking
“At the current rate of development and change, van trailers 10 years from now will bear little resemblance to the trailers of today.”
— Charlie Willmott, Strick Group
A new piece of today’s trailer technology puzzle is the integration of telematics and GPS tracking systems into new designs. For fleets, the benefits appear to be huge.
Wabash currently is integrating trailer-tracking and load-sensing equipment into its trailer designs. “In the future, as technology continues to develop and become more affordable, it is likely that you will see more and more ‘smart’ technology being incorporated,” Giromini says.
He also points to the latest developments in the so-called “Internet of Things” movement that will allow fleets logistical transparency and flow into all facets of their operations that was unthinkable just a few short years ago.
“We’re rapidly moving from IoT being a possibility to more of a reality,” Giromini says. “As a result, Wabash engineers are exploring various technologies that fit our industry. One challenge is to merge truck technology and trailer technology effectively.”
Willmott says trailer and cargo tracking are only the tip of the iceberg for making trailers “smarter” to provide a more compelling ROI – in addition to enhancing public safety and security.
Historically, he says, optimal trailer-to-tractor ratios were often as high as 5-to-1 for most fleets, with conventional wisdom holding that the trailer should be cheap and “stupid” while also offering maximum cube space and maintenance-free longevity. Today, Willmott says, those notions are changing rapidly.
“Today’s better operators are already much more savvy about how the trailer contributes to the distribution chain,” he says. “The fleetwide trailer-to-truck ratio now is more like 1.5- or 2-to-1. Trailers work harder and need to last longer and be smarter. That said, there are literally dozens of opportunities for added-value trailer technology available today, and more being developed all the time.”
Willmott says that in the near future, “smart” trailer systems will be fully integrated with the tractor to provide enhanced telematics, sensors for self-inspection, predictive analytics for diagnostic maintenance, data for better driver and management operating visibility and control, improved public safety and security, and reduced cargo loss and theft.
“At the current rate of development and change, van trailers 10 years from now will bear little resemblance to the trailers of today,” he says.