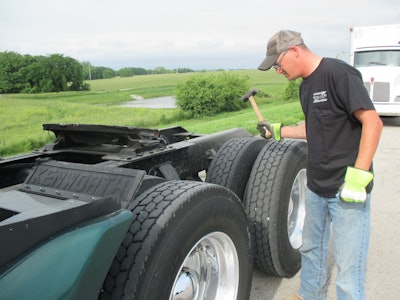
Pre-trip inspections are one the first things listed in the Commercial Driver License manual, hammering home the importance of the process.
However, with fleet managers outnumbered by tractors and drivers tens or even hundreds to one, the inspection process can be one of the most challenging to organize.
“It is hard to give fleet managers pointers on how to manage their people because pre-trip inspections are really a people process,” says Joe Puff, vice president of technology and maintenance, NationaLease. “We can have all of the electronics and all of the behind-the-scenes telematics at our fingertips, but at the end of the day, if the driver wants to bypass the process and pencil whip it, he or she can make it look pretty good.”
Electronic systems like Zonar’s Electronic Vehicle Inspection Report (EVIR) have taken the pencil out of the pencil whip by forcing drivers to scan a radio-frequency identification (RFID) bar code at each inspection point.
“It’s time stamped, so you know how long that driver is in that specific zone and, over the totality of it, how long it took for them to do the entire inspection,” says Zonar’s Vice President of Compliance, Fred Fakkema, who estimates upwards of 85 percent of all pre-trip inspections are done incorrectly if they are done at all.
Once the scanning tablet is returned to its cradle, a customizable inspection report is automatically synched on a fleet’s Zonar platform to back office and maintenance personnel, streamlining and documenting the process from inspection to repair to the truck being placed back in service.
For fleets who still reply on pencil and paper, Puff says one of the best ways to measure the quality of a driver’s pre-trip inspection is to periodically re-inspect behind them.
“A re-inspection makes sure that everybody is doing things by the book and it sends a clear safety commitment message. It’s a no excuse great coaching opportunity,” Puff says, adding problems rarely stem from a driver’s unwillingness to perform a proper pre-trip. Many times, he says, it comes down to training and education.
Dennis Abruzzi, senior vice president of enterprise solutions for Penske Logistics, says pre-trip inspections are a key part of the company’s safety program.
“We provide documented expectations for both the driver and our location management via company policies and procedures,” he says, adding Penske also provides training to its 4,440 drivers across North America.
Training, with an emphasis on ensuring drivers understand what they are looking for in the process, Puff says, is a critical part of developing a safety culture.
“They really need to understand what they’re looking at. One of the things I often see is drivers looking at brakes and tires but they really don’t know what they are looking for,” he adds. “They don’t know at what point it’s a pass or fail.”
A veteran of the enforcement field for 25 years, Fakkema agrees.
“Number one, do [drivers] know what they are looking at when they are doing the pre- and post-trip? Then, number two, are they actually doing it?”
Bob Waller, CEO of Excelsior Springs, Mo.–based Waller Truck. Co., says driver education will be a big part of his company’s focus as it rounds the corner on the second half of 2016.
“As part of our Q3 safety efforts, we will be focusing on a driver education program encouraging pre-trip inspections,” he says. “There will be social media, in cab messaging and an incentive-based program that catches our drivers in the act of doing a pre-trip inspection.”
“The more training we can give drivers to teach them the process correctly, the better,” Puff adds. “If you notice in re-inspections that things are not being done as they should, you need to retrain on specific areas — like recurring issues with brakes, for example.”
The top violations during CSA roadside inspections are generally lights, tires and brakes, each of which Fakkema says can be spotted during a quality pre-trip inspection before they drag down CSA scores.
“Enforcement [officers are] like everybody else. You’re always looking for that low-hanging fruit,” he says. “If you have a truck … and they have a couple marker lights out or a headlight out, that’s the easy stuff and then your inspection can go from there.”