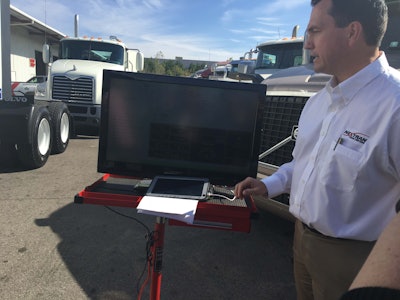
Barely a year after their respective launches, Volvo Group says its network of Certified Uptime Centers have helped cut downtime and streamline the repair process at dealerships nationwide.
Mack Certified Uptime Centers were introduced in late 2015 while Volvo Trucks rolled out its Certified Uptime Center process earlier this year. To-date, there are currently 67 Mack Certified Uptime Centers across North America. Volvo Trucks currently has 57 Certified Uptime Centers across the U.S. and Canada.
Jeff Lester, senior vice president of sales for Volvo Trucks North America, says by implementing standardized workflows and service processes – including redesigned service bays – the company provides faster and more efficient service for its customers.
“It allows consistency in our dealer network from east to west, from north to south,” he says.
Phillips Swaim, director of network fixed operations for Volvo Group, says the push behind the Uptime Center is to manage workflow in a manner that prevents major repairs from clogging up dealership bays.
“The idea is don’t let the short jobs get stuck behind the long jobs,” Swaim says, adding repairs that take four hours or less head directly to the dealership’s Uptime Bay. More complex repairs are directed to the Advanced Bay.
“When a truck goes into an OE truck dealer, that truck is down for an average for four days for an average of three and a half hour repair,” Swaim says. “That’s inexcusable for our customers.”
Jim Ussery, executive vice president of operations for Nextran Truck Center – a Mack and Volvo dealership with 14 facilities across Florida, Alabama and Georgia – says his company folded many of the missions of Volvo’s Certified Uptime Center into an existing internal push the dealership called ROAR (Rapid Observation, Assessment and Repair).
Under the company’s ROAR initiative, techs were challenged to assess a truck within an hour of its arrival to determine the potential length of repair time. If a repair time is determined to take less than 5 hours, Greg O’Connor, Nextran Truck Center’s director of service operations, says their commitment is to dedicate all necessary resources to getting the truck out as quickly as possible.
“We had always worked on a first come first serve basis,” he adds. “This served us well in those prior years because with technology on the truck being at a lower level, and the availability of very high skilled technicians, we were able to make it work.”
“The challenge was that [the new trucks] were much more complex than what we had been seeing,” Ussery says, adding Nextran began experiencing service backups that were not acceptable and a post-recession bounce only added to the backlog.
“Today our customers expect more from us … and first come first serve had to go,” O’Connor adds.
To expedite service, Certified Uptime Centers add a triage lane to quickly diagnose faults and better manage the time it would take to make the repair. It also helps insure that simple fixes are shuffled ahead of more complex repairs.
O’Connor says initial research revealed more than half of Nextran’s repairs were taking five hours or less, but on average it took more than three days to put the trucks back on the road.
“What we realized is that we needed to focus on the small jobs,” he says. “What would happen is when the small jobs would come in, they would get stuck behind the larger jobs.”
Organizing service offerings, Swaim says, has led to a 22 percent increase in repair orders for the group’s dealers and a 16 percent increase in labor sales. Volvo and Mack say their Certified Uptime Centers have shown an 8 percent improvement in service efficiency and a reduction of two-and-a-half days in the overall time a customer’s vehicle spends at the dealership minus the time required to perform the repair.
Certified Uptime Centers also offer a potential savings of up to $2,000 each day per event, Lester says, reducing diagnostic times by 70 percent and repair times by 21 percent.
In 2013, O’Connor says Nextran Truck Center got 43 percent of repair jobs taking five hours or less out of the shop in under 24 hours.
“We set a team of people in place to focus on these trucks,” O’Connor says. “A dedicated group of technicians needed to be put on this team. There needed to be clear separation between this team and what was going on in the rest of the repair bay.”
By 2014, the company’s success rate of pushing small jobs out in under a day swelled to 50 percent and to 55 percent in 2015. O’Connor says Nextran is up to 63 percent this year.
“The Certified Uptime Center program takes the mystery out of a service event,” says Nextran Truck Center President and CEO John Pritchett, whose Birmingham, Ala. facility was the first Certified Uptime Center in the U.S.
Volvo Group’s Certified Uptime Centers training program, which supports Mack Trucks and Volvo Trucks dealerships across North America, was recently awarded a Brandon Hall Group gold award for the Best Learning Program Supporting a Change Transformation Business Strategy. The award category recognizes how learning programs are developed and applied in support of major organizational changes.
The training program was judged on five criteria: the fit to the needs of the business, design of the program, functionality, innovation and measurable benefits and a panel of senior industry experts along with Brandon Hall Group analysts evaluated award entries.
Jonathan Randall, Mack Trucks North American senior vice president of sales, says the award is validation that the company is providing quality training to support its dealership staff and technicians to quickly and efficiently serve customers and improve uptime.
Randall notes that since 2010, Mack dealer locations are up more than 5 percent and have seen service bays balloon by more than 40 percent. The company employs 90 percent more technicians and has seen a more than 250 percent jump in its number of Master Technicians on the heels of more than half a billion dollar investment in its dealership network.
Since 2010, Volvo dealers have invested more than $530 million dollars into expanding service, including adding 63 new locations, which has boosted bay capacity by 50 percent and service capacity by 63 percent. Volvo’s technician labor force has grown by 109 percent and the number of Master Techs has jumped by 372 percent.
Winners will be honored at Brandon Hall Group’s HCM Excellence Conference Jan. 24-27, 2017, at the PGA National Resort in Palm Beach Gardens, Fla.