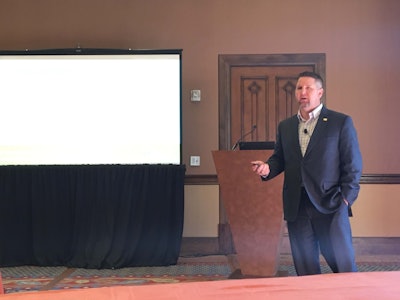
If you have more work than technicians and want to understand why you can’t hire enough people to fill the void, it’s important to understand why they leave in the first place.
“Technicians don’t necessarily leave for money,” says Darry Stuart, president of DWS Fleet Management Services. “I do not believe we have a shortage of technicians. I think what is more important to discuss why they stay and why they leave.”
Ron Crisp, Rush Enterprises corporate operations service specialist, says 100,000 potential technicians will enter the workforce in the next decade, but that is expected to fall almost 77,000 people short of the projected need.
Stuart and Crisp spoke on recruiting and retaining technicians at the CCJ Fall Symposium in Scottsdale, Ariz., Tuesday.
Several years ago, Rush hired a third party to help recruit techs but Crisp says it didn’t work because recruiters weren’t passionate about the industry and didn’t speak the technician’s language.
Rush turned its recruiting efforts internal, building a recruitment team of five people who built relationships with regional tech schools, including a partnership with Universal Technical Institute (UTI).
“We chose to partner with UTI because of the OEM investment within the company with the larger brands,” Crisp adds. “[Graduates] are still young but they can do that warranty work right out of the box.”
The Rush Truck Center network helps the school through donations of trucks, equipment and software for their curriculum. In turn, Crisp says, the company has seen a roughly 80 percent retention rate on students who have passed through the program.
Once you get the employees on the shop floor, Stuart says it’s important they feel their role within the company is valuable. That means not assigning them to wash your car or perform menial tasks that aren’t part of their job function.
It’s also important that management not flaunt the benefits of being the boss, like short days, extended lunches or expensive luxuries.
“It’s upsets the technician because he doesn’t know how to get there,” Stuart says.
Crisp says Rush Enterprises sends an annual survey to its technicians and uses the feedback to make corrections and address concerns.
And while Stuart says techs don’t always leave you for more money, the understanding of how they can build a career – which includes a path to making more money – is vital.
Stuart advises looking at your lowest and highest technician hourly rates and develop a plan to award merit raises every six months to get the employees at the low end to the high end within five years.
“He’s got to know he’s going to get that increase,” Stuart says.
Top earning automotive techs can earn nearly $100,000 within 8 years, but Stuart says it can take trucking techs almost twice that long to see that kind of money with increased responsibilities.
And just like home time is a key for driver’s, Stuart says it’s also part of the fight for keeping techs.
“You’ve got to learn to be flexible,” he says.
Broken and outdated equipment is also a factor driving techs from service bays, Stuart and Crisp say.
Outside the shop, Crisp says Rush pays for uniforms and cleaning because, “no spouse wants to wash those greasy uniforms at home.”
Both Crisp and Stuart agree that one of the biggest factors in keeping techs can be cleanliness and organization of the shop itself.
“A fleet [tech] cost per minute is about $1,” Stuart says. “If he spends 15 minutes looking for something because it didn’t get put back where it belongs, you just lost $15.”