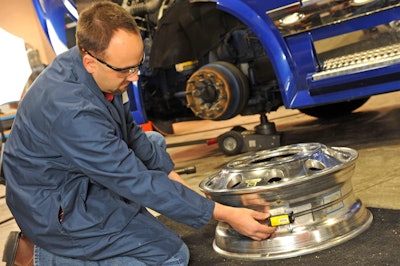
Regularly checking for inflation is a staple of every preventive maintenance and pre-trip program but with shippers getting antsy to move freight and carriers itching to oblige, the finer points of a pressure check can slip between the cracks.
According to the Federal Motor Carrier Safety Administration (FMCSA), approximately 7 percent of all tires are under-inflated by at least 20 PSI, and only 44 percent of all tires are within 5 PSI of their target pressure.
Fortunately, through systems like Automatic Tire Inflation (ATIS) and Tire Pressure Monitoring (TPMS), technology is capable of serving as a fleet’s wingman.
“Tires generally do not fail in the yard,” says Harry Trost, senior manager of product planning at Dana. “Fleets realize even a perfectly inflated tire can encounter road debris or be damaged in service.”
Both TMPS and ATIS systems provide backup by helping keep tire pressures at appropriate levels, but they do so in different ways.
“We view ATIS and TPMS as two different products that are complimentary in nature, not competitive,” says Pressure Systems International Vice President of Global Sales and Marketing Jim Sharkey.
Easily installed on a tractor or trailer, TPMS allows for the monitoring of tire pressure, but also provides temperature warnings via the TPMS sensor.
“TPMS systems enable the ability to monitor the whole vehicle combination,” says Jon Intagliata, TPMS product manager for Bendix Commercial Vehicle Systems. “Trailer TPMS data is wirelessly transmitted to the tractor and displayed on the dash to allow the driver or telematics system access to alerts and warnings, in addition to tire data for pre-trip inspections.”
TPMS monitors tire pressure through valve stem mounted sensors, which are good for ATIS with an auxiliary check port tire hose, flow-thru sensors that allow air to be manually added without removing the sensor, or internal tire sensors placed either inside the valve stem or banded to the wheel.
This data can also be off-boarded to the back-office, enabling the fleet to take action when required. Intagliata says further improvements in trailer telematics benefit the TPMS system since they enable the fleet to see issues with trailer tire pressures even when the trailer is sitting unpowered remotely.
“The TPMS system will continuously monitor the tires and send any alerts as they occur, allowing the fleet to proactively know if there is a tire problem before the driver arrives to pick up the trailer,” he says.
System sensors feed the information to the driver in the cab via a display, back to the fleet through telematics, or both. But discretion is largely left to the driver on whether to stop and re-inflate tires.
“This is inefficient and can be ineffective to preserve tire life, tire casing (re-tread ability), maintaining fuel efficiency and preventing an on-road tire failure,” Trost says of leaving the ultimate decision to re-inflate a tire up to the driver. “TPMS can provide the driver with information about a low-pressure tire but cannot take active control to properly inflate the tires.”
On the other hand, an ATIS directly measures tire pressure and takes proactive action to re-inflate tires while the vehicle is in operation, independent of the driver.
The ATIS uses air from the truck and trailer supply, but “air tank system reserve pressure will be retained for future braking events as a priority,” Trost adds.
The benefit of the ATIS system is that its primary objective is to keep an adequate level of air pressure in the tire, rather than simply monitor it.
“In the same way a speedometer cannot guarantee a vehicle will not travel above the posted speed limit, a TPMS system cannot guarantee tires will not fall below their target pressure,” says Aperia Technologies Vice President of Marketing and Customer Experience Judith Monte. “For that reason, any fleet wishing to reduce tire-related downtime would benefit from ATIS.”
The side effect is that process can hide potential issues.
“While the TPMS system lacks the ability to add air, the ATIS system continuously adds air when the tire has a leak. If the leak is too large, the driver may never know the ATIS system cannot keep up, ultimately resulting in a catastrophic failure – exactly the situation you are trying to avoid by using these technologies,” Intagliata says. “In our experience, some fleets seeking to move to TPMS from an ATIS have mentioned that the ATIS system will inadvertently mask a leak resulting in damage to the tire or a failure. Casings can be damaged due to long-term operation with objects embedded in the tire, causing rust or other damage and resulting in a casing that cannot be retreaded.”
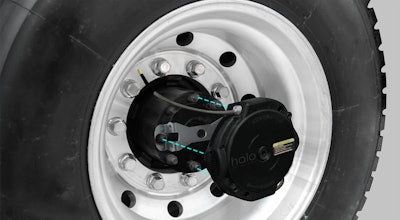
Monte says ATIS solutions are capable of overcoming 97 percent of tire leaks. In order to flag persistent pressure loss, Sharkey adds most ATIS provide a warning light that identifies when air is flowing through the system to fill a tire.
“Whenever the warning light is activated, a driver should always stop to inspect and determine the cause … the light should be treated similar to a check engine light,” he says, “and action must be taken.”
“The purpose of this light is to alert the driver of the abnormal situation,” adds Ramses Ortiz, Meritor’s product manager for trailer products.
Intagliata says in some cases fleets are combining TPMS with ATIS “to provide a belt-and-suspenders approach to tire management.”
“When we first introduced ATIS to the market, fleets began to understand the value in having an automatic system on their trailers,” Sharkey adds. “Now, with so many telematics providers in the market providing a data path, fleets see the opportunity to be more proactive with maintenance by adding TPMS as an enhancement to the ATIS, not a replacement.”
Most applications spec TPMS for the truck and ATIS for the trailer.
The trailer’s hollow axle makes routing airlines for re-inflation much easier, and such systems can be more vital for trailers which often sit off-site for extended periods awaiting pickup and don’t receive regular maintenance attention.
“It is not just about the tires that leave the yard,” says Ortiz. “What about a trailer that has been sitting at a customer’s yard waiting to be loaded?”
“A tire may not leave the yard underinflated, but it could be damaged while in operation,” Intagliata adds. “Or in the case of a trailer, you may not see that trailer for 30 to 60 days – plenty of time for a potential tire problem to develop.”
Sharkey estimates the take-rate of ATIS to be north of 60 percent on new trailers, “plus there is a healthy retrofit market,” he says. “While the volumes on the vans/reefers is high based on the percent of the market they represent, we see customers from literally every vocation.”
Once installed, the maintenance needs of TPMS and ATIS are relatively low-tech, and most problems can be discovered as part of a pre-trip inspection.
Depending on the duty cycle, Ortiz says bi-annual to annual inspections are recommended.
Trost says occasional inspections may be performed to identify any potential leaks in the air system or tire hoses and re-tighten fittings as appropriate. For a TPMS system, Intagliata says the required maintenance is typically limited to reprograming sensors when they are moved or replaced.
“With TPMS, much of this is more related to monitoring battery life and battery replacement,” Sharkey adds. “With regard to ATIS, operators should always verify that the system is turned on, which can usually be accomplished with a visual check that the on/off valve is in the on position.”
Periodic maintenance guidelines provided by the manufacturer typically include a check of the output pressure from the control box, tire pressure checks and validation of the indicator light operation. A leaking connection or worn component, Sharkey says, will cause the system light to activate, in which case a soapy water check will identify the location to take appropriate action.
Fleets generally aren’t anxious to tack new tech onto their fleet unless they can quickly reap some kind of benefits, but often those calculations – taking into account fuel savings and tire life – are complex.
“There are several benefits of running either ATIS, TPMS or both,” Sharkey says. “The ones that are quantifiable, include fuel economy, tread wear, roadside call avoidance and labor savings. The individual impact of them will, of course, vary with vocation.”
For example, in specialized short haul applications, fleets find that more of their savings come in the reduction of roadside calls versus fuel savings. However, those savings are only realized by the fleets that have protocols in place to deal with issues as they arise.
“If a fleet doesn’t have a process to react to a low tire, they are simply wasting their money” on TPMS, Sharkey says. “After all, drivers are generally compensated by the miles they drive, not by how much pressure they have in their tires.”
But sometimes, Intagliata says payback calculation doesn’t need a lot of variables.
“In general, a TPMS system pays for itself if you avoid one on-road tire failure,” he says. “When you add up the cost of the tire, road call and downtime, the investment you made in a TPMS system is more than covered.”
Similarly, Sharkey and Ortiz estimate payback on an ATIS system is about 12 months.
“Keep in mind that this return on investment based on the quantifiable aspects,” Sharkey says. “Items such as safety, driver satisfaction/retention, casing utilization and HOS efficiency are icing on the cake.”