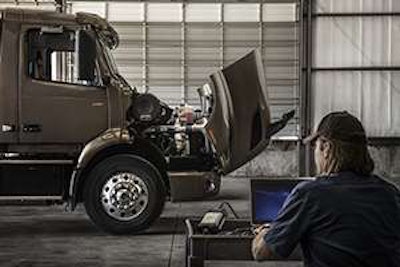
This is the second of a multi-part series on how drivers and the maintenance department work together to increase uptime. The first installment, “Pre-trip training, follow up critical in uptime goals” can be found here.
A good vehicle inspection is only as effective as the maintenance department’s ability to fix it.
When a driver for Little Rock, Ark.-based Maverick Transportation flags an item during an inspection, that is communicated to the maintenance department through the company’s Qualcomm system.
“We’ve got seven maintenance coordinators that work out here and manage the maintenance on our fleet,” says Maverick’s Director of Maintenance Brent Hilton, “and those forms go not only to operations and logistics but it goes to maintenance coordinators so they can follow up and get those items fixed.”
Memphis, Tenn.-based Ozark Motor Lines’ Qualcomm system requires the driver to acknowledge having performed a pre-trip, and every 24 hours prompts them to submit a Driver Vehicle Information Report (DVIR).
“Those, depending on what it is, go through our road breakdown department,” Ozark Director of Maintenance Glen McDonald says, adding the department would schedule any work needed with a priority based on its severity.
“It’s really important that operators are specific and detailed,” he says. “That gives the technicians a place to start addressing issues.”
It’s at this point where the onus of a good inspection shifts from the driver to the maintenance bay. If a driver is regularly performing high-quality checks but their flagged items aren’t getting fixed, Transervice Vice President of Maintenance Taki Darakos says not to expect that kind of quality for very long.
“If you have a group of drivers and they’re doing the right thing – they’re writing the equipment up and saying ‘we’ve got this problem and that problem’ – from a shop perspective you’ve got to get after it,” he says. “If I’m a driver and I’m writing it up for 30 days that I have this check engine light and no one’s doing anything about it, at some point my desire or my thoroughness starts to fade and maybe I get into a ‘I don’t give a damn’ type of mood. That’s when you start to run into a lot of problems.”
Incentivizing drivers
Hilton says Maverick has found success in rewarding the drivers who help keep their trucks in top mechanical condition. Their drivers are incentivized for clean CSA inspections, which ensures timely performance of preventive maintenance.
“That all plays into some of their pay,” he says.
Similarly, Ozark offers financial gain by way of gift cards, and all drivers for Alabama-based WTI Transport receive $100 for each clean Level 1, 2 or 3 inspection.
With the hopes of catching CSA violations before the truck leaves the yard, Jem Blair, WTI’s vice president of safety, runs occasional initiatives where high-quality pre- and post-trip inspections come with unexpected bonuses for the drivers.
“We’ve had programs in the past where we would be on a vehicle inspection campaign and we actually hid a $50 bill in a certain area of a truck or trailer, in somewhat of an inconspicuous location but in an area that would be part of the driver’s inspection,” Blair says. “If the driver finds it, they get to keep it.”
Excelsior Springs, Mo.-based Waller Trucking has found praise for a job well done has helped boost both morale and uptime. Amanda Schuier, Waller Trucking’s director of marketing and recruiting, says the company consistently sends out fleet-wide messages commending drivers for their performance and communicates any drops that may come in the company’s CSA scores through their efforts.
This summer, Waller kicked off a company-wide challenge for its drivers where they can earn poker chips for being caught performing vehicle inspections on premises. Those chips, and others earned through performance metrics, pile up in an internal contest that will award the winner $500.
“It’s important to be proactive versus reactive,” she says. “In a reactive situation, you have a breakdown on the road.”