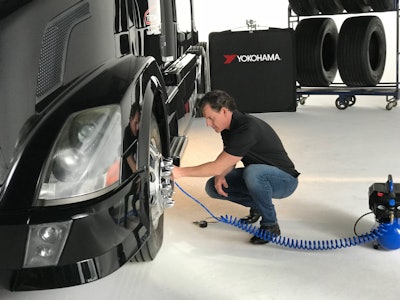
Various aerodynamic devices help move air out of the way and reduce resistance, but there are fewer options for reducing drag created by tires as they travel across the road.
“The most effective and least costly component to increasing a fleets’ fuel efficiency is air pressure,” says Tom Clauer, Yokohama Tire senior manager of commercial and OTR product planning. “Maintaining the proper air pressure is the single most important item to reducing a tire’s rolling resistance.”
Because the air pressure is what provides the tire’s load-carrying ability, inflation is a contributor to its rolling resistance. Tire rolling resistance is the third biggest factor affecting a vehicle’s fuel economy behind engine inefficiencies and aerodynamic drag, and fuel costs represent many fleets’ highest non-payroll operating expense. Rolling resistance from tires accounts for approximately one-third of fuel costs.
According to the Technology and Maintenance Council, “Improper tire inflation, defined as little as 10 psi low, reduces fuel economy by about one percent. About 30-40 percent of the fuel required to move a vehicle down the highway is spent overcoming tire rolling resistance. When tires are underinflated, the amount of drag created by the tires increases.”
“Simply consider dribbling a basketball at recommended air pressure versus one that has less air pressure. One has a lot [more] bounce because of the correct air pressure,” Clauer says. “Same applies to rolling the basketballs across a floor. The one with the correct air pressure will roll much faster and further due to its [lower] rolling resistance.”
If tire pressures are at the recommended level, the next step might be investing in a set of low rolling resistance (LRR) tires. Lower rolling resistance is achieved by manipulating a variety of tire functions, like casing materials and tread designs to stabilize ribs and blocks.
“Aerodynamic drag is also taken into consideration when designing tread patterns and depths,” Clauer adds.
Stabilizing tread blocks, which reduces the tire’s movement – or “squirm” – along with LRR rubber compounds affect the tires’ tread depth, mileage range and traction to a degree.
“A tire’s tread can account for up to half of a tire’s rolling resistance in many cases,” says Mahesh Kavaturu, Goodyear’s commercial technology director, adding LRR tires seek to reduce the amount of energy lost through the tread area via tread deformation. “This can be achieved by reducing the tread block’s height, by stabilizing the tread elements using higher angle drafts, by designing the tread elements to take more rigid shapes or by increasing the surface area of the tread block to increase its stiffness.”
Tire compounds are also key. Kavaturu says before a truck tire goes to market, the rolling resistance properties of its compounds are evaluated by measuring a dynamic called “rebound.”
“Think of bouncing a rubber ball on the ground and then measuring how high it bounces,” he says. “The higher the ball bounces, the less energy it has lost in its collision, or deformation, with the ground. Compounds with good rebound properties tend to exhibit lower rolling resistance.”
One widely held belief is that the lifespan of a LRR tire is shorter than a standard tire, but Toyo Director of Sales-Commercial Truck Tires Mike Graber says that is only true because the LRR tire usually starts with less tread depth off of the rack. The rubber itself doesn’t actually wear measurably faster.
“When measuring miles per 32nd of an inch of tread, the difference between the two is much closer,” he says.
With each new generation of LRR tire, wear-life improves and fleets who years ago strapped on a set and were left unsatisfied might be surprised at the performance improvements.
“As LRR tires have gained in popularity tire manufacturers have been able to increase the tread depths of LRR steer and drive tires and still maintain fuel savings with newer tread compounds and casing designs,” says Chuck Luther, Northeast sales manager for Triangle Tire USA. “In most cases today, LRR tires are capable of achieving comparable or better overall mileage than conventional non-LRR tires.”
Generally, Graber says traction tires have a higher content of natural rubber, which tends to be softer and offer more grip and cut/chip resistance. Synthetic rubber contributes to lower rolling resistance but comes with a tradeoff on traction versus a standard tire with the same tread pattern.
“From a rolling resistance standpoint, a perfectly smooth rubber surface with no pattern would be ideal,” says Marco Rabe, Continental’s head of truck tire technology in the Americas region. “However, this would come at the cost of traction and wet/snow performance.”
As long as the tread design is conducive to the environment in which the tires are used, Luther says most carriers won’t notice any difference in traction, adding it all goes back to proper inflation.
“It is important to emphasize the role air pressure plays in fuel efficiency as well as tire footprint and traction. Always inflate tires to the tire manufacturer’s recommended air pressure for the load carried,” he says. “This, in many ways, goes against conventional wisdom of 100 psi in all wheel positions. However, proper air pressure to load carried translates into better traction, better fuel efficiency and casing longevity.”
Continental recently participated in an independent third-party test using its 11R22.5 LRR tires. In the long haul segment, the Continental tires delivered a fuel economy of 7.35 mpg. According to the “2018 Annual Fleet Fuel Study” from the North American Council on Freight Efficiency, the national average is 5.91 mpg.
Based on an annual average of 105,014 miles, burning more than 17,773 gallons of fuel per year – at $3.89 per gallon – Continental’s fuel efficiency improvement accounts for $13,500 in fuel savings per truck.
“The exact fuel economy benefit will vary from fleet-to-fleet depending on the exact nature of their operations,” says Cowart, “however, we can use a rule of thumb that, for line haul fleets, a 3 percent reduction in rolling resistance translates into a 1 percent fuel savings, or an increase of .05 miles per gallon. It may not sound like a lot, but for a fleet the savings can really add up.”
Savings can be further compounded by retreading the casings provided the casing is in retreadable condition.
“In many cases, as tires have evolved over the years, the casing itself has become more fuel efficient by optimizing the construction and rubber compounding,” says Phillip Mosier, manager of commercial tire development for Cooper Tire. “These improvements also lead to lower heat generation in the casing, which creates a very retreadable tire.”
Reducing heat reduces rolling resistance, but Rabe says it also improves the likelihood that a casing can be retreaded since heat deteriorates tires.
“The key is to make sure that the casing has been properly maintained throughout its initial lifecycle and that the casing is of premium original quality,” Kavaturu adds.
Applications that run at consistent steady state speeds – like long haul and regional segments – stand to reap the most from an investment in LRR tires.
“Applications such as [pick-up and delivery] or on/off road benefit less from low rolling resistance compounding because the engine and brakes make a higher contribution to fuel economy,” Mosier says.
“Whenever choosing tires, a critical question for a fleet to consider is, ‘What are we asking the tire to do,’” adds Kavaturu. “A mixed-service tire that has been designed to roll across severe terrain might not be the best choice for a long-haul truck, and a long-haul tire that has been engineered for low rolling resistance is probably not the ideal choice for a truck that primarily travels off-road, across debris-strewn surfaces. Some tires are better-suited to certain applications than others.”
In applications like on/off-road and waste operations – where there is a high probability of damage, frequent starts and stops, multiple turns and loose material slippage – Clauer says it’s difficult to measure benefits of LLR tires.
“Of course, fuel saving can be had in any operation/application, however the tradeoff may make it a moot point,” he adds.
Often the trailer is a no man’s land for tires – an afterthought or place to mount tires nearing the end of their lifecycle – but Cowart says the contribution of rolling resistance is linked to the number of wheel positions on the vehicle. Therefore, she says drive and trailer positions at eight tires each would contribute much more than two tires on steer.
Most fleets using LRR tires, Graber says, use them in both steer and drive positions. If opting between drive and steer axles to try them, he says the drive position would make the most sense because there are more positions to extract the fuel consumption benefit.
“The more wheel positions using LRR tires, the better the fuel consumption result for the user,” Graber says.
According to Continental research, the impact of each axle position on the overall rolling resistance is 15 percent on the steer axle, 42.5 percent on the drive axle and 42.5 percent on trailer axles.
“Fleets often discount the trailer as being an influence,” Rabe says, “but it has a high influence on fuel economy.”
“Of the three wheel positions on a tractor trailer combination, the trailer axle tire position contributes 35-40 percent of the tire rolling resistance and therefore should be considered as a valuable position for fuel saving tires,” Luther adds.