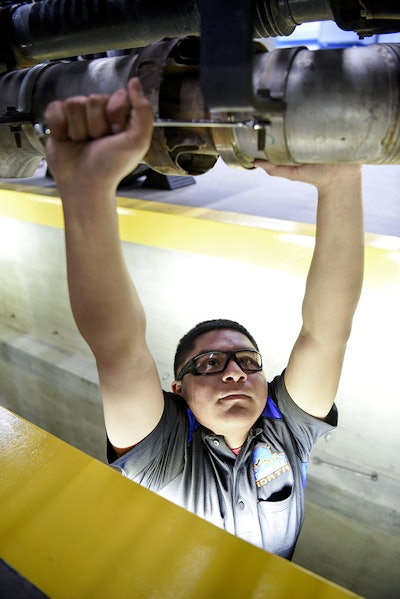
Trucking has become an industry of shortages. In the fleet community, there’s a shortage of drivers, a shortage of truck build slots and a shortage of new freight available.
Shortages haven’t bypassed the parts and service channel. Product and employment shortages are as much a part of the aftermarket as brake shoes and filters.
While production shortages commonly are tied to a strong market stressing a supply chain, the source of trucking’s employment shortages are tied to something much more serious.
Trucking’s recruitment pipeline is broken.
In Part II of our 2019 Special Report on trucking’s technician shortage, CCJ seeks to explain how trucking’s longstanding technician recruitment tactics have crumbled and how individual service providers and the industry at large can cooperate to help re-establish a stable recruitment strategy.
1. Fixing the industry’s message
One of the most alarming and damaging realities of trucking’s current struggle to find quality technicians is the disconnect between vocational education and the industry at large. What was once trucking’s strongest supporter has become an unreliable partner.
Far too many technical schools are teaching curricula for a trucking industry that doesn’t exist – educating students on systems and repairs that are antiquated yet also somehow more advanced than what trucking’s entry-level technicians require – while the industry itself continues to ignore its failures in transitioning young graduates into its ranks.
The result is a leaking, broken recruiting pipeline that’s carrying almost as many young people away from service bays as into them. Trucking’s technician shortage does not exist because no one is interested in the profession. Rather, it exists because those who are interested ultimately are choosing not to pursue the industry as a career.
“We always talk about our shortages like there’s nobody out there who wants these jobs, that there is a shortage of people interested in our industry,” says George Arrants, past chairman for the American Trucking Associations’ Technology and Maintenance Council’s SuperTech competition. “That’s not true. We don’t have a shortage of applicants, we have a shortage of qualified applicants. Those are two very different problems.”
Arrants offers this distinction because he believes it to be the linchpin to the trucking industry’s current predicament. He says service facilities might not be receiving ideal candidates for the open roles they are trying to fill, but those businesses can’t place the blame for their problem on the education system alone. He says the trucking industry has done a terrible job conveying to schools what it expects from the next generation of diesel technicians.
“We don’t let other forms of government spend our money unwisely, so why do we let the schools?” he asks. “We go to these [industry] meetings and talk about the shortage and act like education is someone else’s problem. It’s not. If schools aren’t teaching [students] what we need them to teach, we’re responsible for that.”
What the service channel would like to see taught is more than component identification and basic repair instructions. Vo-tech students and prospective employees also should be briefed on what will be expected of them when they enter the industry, what they’ll be paid and what their long-term future holds.
On that first point, Arrants says it’s time for the trucking industry to wean educators off engine-centric instruction. He says too many post-secondary programs are developed and marketed around advanced diesel diagnostics and repair — material that draws interest from prospective students but has little practical value. Arrants says entry-level technicians don’t overhaul engines, but they do perform preventive maintenance and Compliance Safety Accountability-readiness inspections. That’s what students need to learn, he says.
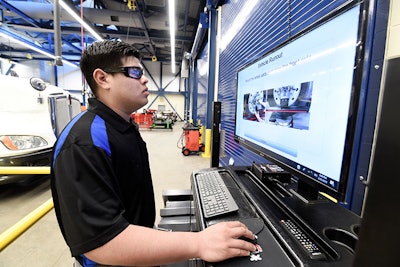
Then there’s the financial component. Tim Spurlock, co-founder and president for the American Diesel Training Centers, says most post-secondary diesel and heavy truck programs promote the possibility of high five- and six-figure salaries to entice student registrants. Spurlock says that message is misleading because it fails to convey the realistic wages that students will be offered from technical careers upon completion of their degree.
Coupled with rising admission rates at these same schools, many young technicians feel overburdened by the financial obligations of their new careers almost immediately, Spurlock says.
“I don’t know that there is another business where ‘ghosting’ is more of a thing than this business,” he says.
“These guys have financial commitments. If they find somewhere else where they can make another dollar [per hour], they’re gone.”
Too many technical students also are entering school unaware of the financial aid opportunities that exist for them, says Brandon Eckenrode, director of development for the Collision Repair Education Foundation, the technician recruitment arm of I-CAR.
“We give out $250,000 to $300,000 in scholarships each year, yet we probably only see a total of 150 to 200 applications,” Eckenrode says. “We are sitting on more money than we have applicants.”
“[Universal Technical Institute] will make more than $15 million in scholarship and grant money available to students in 2019,” adds Duane Kramer, UTI’s vice president of education.
Experts say the industry has to do better in communicating its financial support to both education partners and prospective employees. They say technicians will commit to a business that demonstrates a willingness to financially commit to its associates the same way those associates committed to their new career.
“If your techs have student loans, and you hope to keep [those techs], then you have student loans,” says Spurlock.
Finally, the service channel also must improve how it conveys performance expectations and career path possibilities to new employees, says Homer Hogg, director of technical service for TA-Petro. Once a technician himself, Hogg now oversees more than 3,000 technicians across the truck stop chain’s national network of more than 220 locations.
Hogg says TA-Petro has invested heavily in a comprehensive technician training and mentorship program to help acclimate its entry-level technicians into its business and showcase the growth potential that exists within the national chain. With 300 to 400 open technician positions at any given time, TA/Petro can’t afford to lose a good technician when it is able to recruit one into its operation, he said.
“With unemployment numbers where they are, there are not enough people to go around as it is,” Hogg says.
2. Building technical school relationships
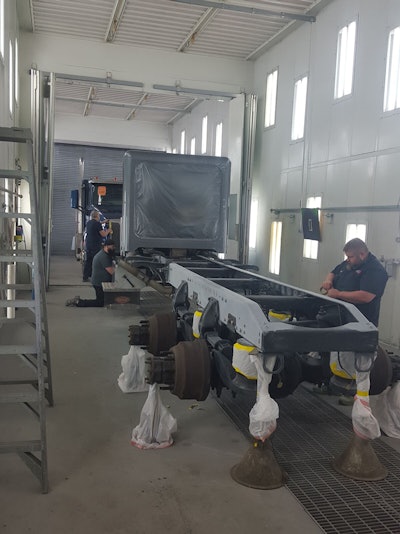
Though potential quality technicians can be plucked from anywhere, trucking’s most fertile recruiting ground remains vocational and technical education programs.
Yet as demand for technicians rise, so too has competition for graduates from such programs. Many of the more than 10,000 students who will graduate from diesel and heavy truck post-secondary programs in the United States in 2019 already have job offers. Some already are working as interns in the businesses they’ll soon call home.
For service operations, successfully leveraging a vo-tech program as a recruitment tool now requires more than just a booth at a career fair or a call to a program instructor. To ensure they can bring young technicians into their business tomorrow, many proactive service providers are learning they need to engage with their local technician programs today.
“That’s been our best resource,” says Charlie Nichols, general manager for TAG Truck Center in Calvert City, Ky. “We’ve tried a lot of different ways [to recruit] over the years. Classified ads don’t work in today’s world. [Online sites] didn’t produce many good candidates. We’ve had a little success networking, where our guys have convinced friends to apply, but overall, we are finding if we want to find a good tech, we have to grow our own.”
The first step for service channel professionals looking to develop a partnership with a technical school is outreach. Industry professionals must introduce themselves to local educators and express their desire to create a mutually beneficial partnership, says Arrants, who specializes in facilitating such meetings.
Arrants says that once a connection is made and a relationship is established, it’s the responsibility of the industry professional to maintain it. He says many educators are eager to work with trucking professionals, but they’re busy like the rest of us, so service professionals shouldn’t be discouraged if a single interaction with a technical school doesn’t turn into an immediately budding partnership.
“We can’t be afraid to go in,” he says. “We can’t avoid it because we don’t know what to ask or what to do. If half of our industry just showed up [at these schools], we wouldn’t be having this conversation.”
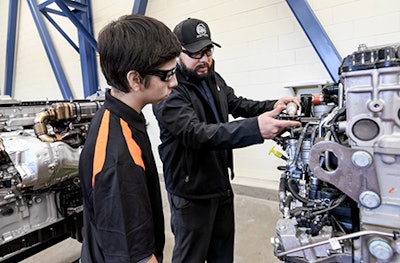
“You can’t give up after one bad experience,” Eckenrode adds. “It takes a lot of effort to make change.”
It’s early in this relationship-building phase where industry professionals should offer assistance. This can be done through donations, such as equipment and investments into a school’s budget or scholarship fund, or pledges of one’s time to assist the school in some way.
Arrants says most educators are looking for help any way they can get it and will accept any assistance they can find, though he adds investments of time and expertise shouldn’t be overlooked for the simpler, more straightforward monetary donation. He says good educators also want advice and to eliminate the disconnect between industry and education as much as anyone.
“Most schools and school districts want industry to drive the train,” he says. “They want to be told what they need to do.”
Assisting an educational program shouldn’t be a one-time deal, either. The more involved industry is in a local school, the more likely its curriculum will fit its region’s needs and produce graduates capable of entering the workforce seamlessly.
Nichols says he speaks to students and educators at his nearby school nearly every semester to keep his bond with the program strong. In Fresno, Calif., Mike Betts, chief executive officer for Betts Co., led a group of trucking professionals who spent years engaging with the community’s school district on the importance of career technical education before finally persuading the district to invest in a new facility to support a diesel and heavy truck high school education program.
Eckenrode says many technical schools are looking for a similar level of support. “I know a lot of instructors who are eager to bring industry into their schools,” he says. “They see that as support for their program, a way to attract students and also show their superiors that their programs are important. A lot of these [instructors] work in fear that if they can’t find more students, their programs will be shut down.”
That is a legitimate fear. Nationally known WyoTech closed in 2018, and ASE research shows the number of students entering vocational education programs has stalled. Experts say industry can assist in this area, supporting recruitment initiatives by education partners to steer young people into vo-tech classrooms.
Eckenrode says CREF has found success in this area by holding career fairs in conjunction with public events such as auto shows that are filled with car and truck enthusiasts. “It’s allowed us to showcase our industry to a captive audience,” he says.
3. A California example
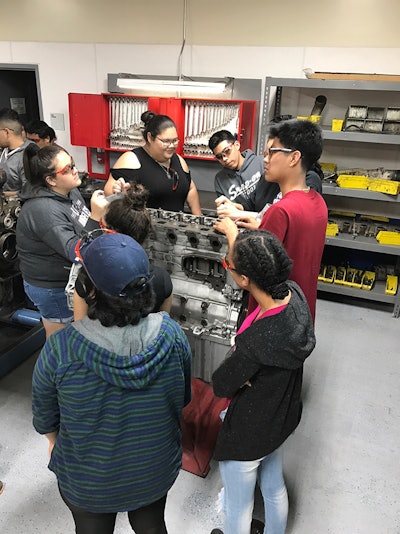
The crown jewel of a decade-long process to bring elite technical education to central California was unveiled this spring with the opening of a diesel and heavy truck career technical education pathway at Duncan Polytechnical Career Pathways High School in Fresno, Calif.
Developed in partnership with the Fresno Unified School District, the Fresno Chamber of Commerce and the greater trucking industry of central California, Duncan Poly’s new program comes complete with a state-of-the-art training facility and a curriculum to match.
For those in the school district, community and trucking industry who have spent the last several years tirelessly turning their dream into a reality, the program is not just another vocational pathway available to the students of Fresno. It’s an example of what can be done when education and industry come together and how vision and determination can transform a community.
It’s also a blueprint. If the trucking industry is ever going to solve its technician shortage legitimately by addressing its root causes and not its downstream symptoms, then the efforts of the men and women of Fresno should not be overlooked. The new Duncan Poly diesel technician program, and the other new and refurbished programs in the communities surrounding it, is the future of technical education.
“Fourteen months ago, we stood right here on this spot, and you will recall it was a grassy field,” said Bob Nelson, superintendent for the Fresno Unified School District, during Duncan Poly’s ribbon-cutting event in March.
“Today, a once-in-a-lifetime opportunity has arisen, a facility that is absolutely better than anything we ever could have imagined. This is about every high school kid having a stellar and unbelievable high school experience. And this is what our kids are going to receive.”
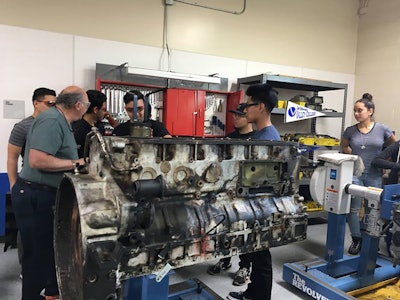
Fresno’s blueprint already has started to spread. Just four hours south in San Bernardino, construction is underway on a four-bay training facility to support diesel and heavy truck education at Pacific High School. Berchman “Kenny” Melancon, instructor at nearby San Bernardino Valley College, says the new building will enhance what already is a strong truck technician career pathway that exists in the community.
Thanks to a partnership between the San Bernardino City Unified School District, SBVC and local industry, high school students are eligible to take Pacific and SBVC technician courses as part of their public school curriculum. Melancon says SBVC plans to introduce a non-credit program in its fall semester that will allow students of all ages to take any vocational course the college offers for just $30.
Melancon says the goal of the program is to eliminate the financial barrier to technical education. Rather than asking students to pay for their training in advance of their career, non-credit courses will enable students to earn certifications for completing courses they can use to help gain employment. SBVC developed the program in response to local industry input as a low-risk way to draw talented young people into vo-tech careers.
“Our goal is [those students] will get a job and then come back and pay for the credits they’ve earned toward their degree,” he says.
The financial commitments made by the school districts in Fresno and San Bernardino also have been backed by significant support from trucking’s supplier community and service channel. The new facilities at Duncan Poly and under construction at Pacific will feature millions of dollars of trucks, engines, tools and equipment donated by industry partners. The schools also have introduced internship programs with area service centers to bolster their students’ education opportunities in advance of their graduation.
Duncan Poly instructor Eric Rubio says his students are taking note of that investment. Duncan Poly’s program already is at capacity for the fall school year, and Rubio says the school is searching for a second instructor to expand the pathway’s admission capabilities.
“I think a majority of these kids didn’t know what they were going to do after high school, but now they do, and they’ve found they have a passion about it,” he says. “They are really excited and ready to be challenged.”
Melancon concurs. “When I ask students what was rewarding to them about my class, a lot will say they will now be able to support themselves and their family,” he says.
4. Where are those potential techs?
Cooperating with vocational education isn’t the only place where service providers can uncover technician talent. There are other avenues that can be considered to fill open positions.
POACHING
Offering better wages and benefits to draw technicians away from competitors has been an established hiring practice in the service channel for decades. The tactic has obvious benefits because positions are filled quickly by experienced technicians. However, many in the industry say they are trying to move away from the strategy and toward more sustainable recruiting practices.
If a 50-cents-per-hour raise lures a technician away from his current employer into your business, what’s to stop him from leaving again if another competitor does the same, asks John Devany, general manager for Betts Truck Parts & Service. “There’s no telling how long they’ll stay,” he says.
Instead of adding new technicians to the employment pool, poaching just moves them around, Arrants says. With the industry’s employment gap widening, searching exclusively for existing technicians to fill open positions ultimately creates more job openings on a national level.
“We should be adding techs,” he says. “Our industry is growing. Yet we’re losing more [technicians] every day.”
MILITARY
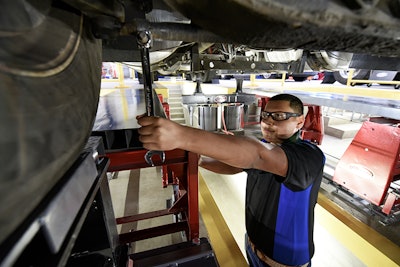
The U.S. Department of Defense reports about 250,000 enlisted service members exit active duty for civilian life annually, and many of those veterans are ideal candidates for trucking’s service channel. Hogg says that’s a good thing. TA-Petro has added multiple veterans to its nationwide technician roster in recent years, and he finds them to be capable and reliable associates.
“I think the training they receive in the military gives them a base of skills we can build on,” he says.
In addition to skills such as work ethic, professionalism and discipline, many veterans also have experience working with heavy equipment. Each branch of the armed forces features a substantial technical division, and when those service members enter the workforce, they increasingly are gravitating toward similar private-sector work.
“We have really started searching for people exiting the military, and we’ve had good luck hiring them,” says Jim Hinton, service trainer for Summit Truck Group.
OTHER INDUSTRIES
Spurlock believes trucking’s technician shortage ultimately will be solved by people who aren’t in trucking but want to be. He says the biggest leak in trucking’s employment pipeline is the financial and time commitment expected of young people before they even get a job in the industry.
Multiyear $30,000-plus tuition technician programs drive away more prospective employees than they graduate. Spurlock says ADTC has developed its customizable 300-hour training curriculum specifically to reduce such obstacles.
“There are a lot of people out there in low-wage high-effort jobs who want something better but can’t find it,” he says. “If we [as an industry] can offer them educational programs that eliminate those barriers, I think they’ll come to our market in droves.”
Adjacent industries such as agriculture also offer potential avenues for technician recruitment, says Chris Sterwerf, chief financial officer and chief operating officer for Fairfield Auto & Truck Service.
“I’ve had success getting involved with 4-H, going to farm bureaus and county fairs and finding people who have worked on tractors and done similar work” as truck technicians, he says.
Click here to download the Randall-Reilly technician wage survey
TARGETING TECHNICIANS
Part 1: Trucking industry faces major shortage, opportunities for diesel mechanics
Part 2: Why trucking must change its technician recruitment practices
Part 3: Investment in your business can help retain your best technicians