Proper data analyzed in the proper manner can help you reduce maintenance costs. However, maintenance is just one piece that goes into figuring out the optimal life cycles for your assets.
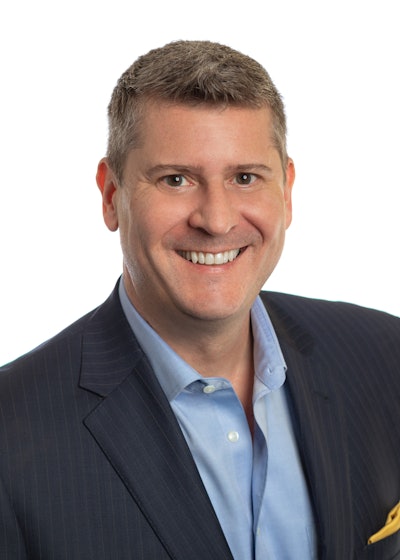
As it relates to reducing maintenance costs, the repair order is the place to begin. You should itemize each repair order by VMRS code and also capture parts costs, labor costs, labor time and the amount of time the vehicle was down. Essentially what you are doing is dissecting the repair order, and the reason you break it down into these various parts is so that you can measure trends and pinpoint anomalies and items that start costs trending upward.
You need to get all the data about each repair warehoused in the dissected format in order to be able to identify anything that sticks out. Moving forward, you use that information to make decisions which allow you to bring costs down.
One note of caution: you may want to eliminate certain types of repairs from your analysis. The most common one would be repairs that resulted from an accident.
Analyzing maintenance data allows you to see if you are operating your assets at the most optimal life cycle.
Of course, maintenance and repair costs are not the only factors to consider when determining an asset’s optimal life cycle. Examples of other factors include the cost of new equipment; used truck values; inflation; the fuel economy of both the existing asset and a potential new asset; fuel costs; interest rates and asset utilization rates.
While analyzing maintenance and repair data can help reduce costs, you need to consider these other factors to ensure you are not running the asset too long or not long enough.
When analyzing data, start at a micro-level – for example, by month and by asset. Then continuously roll up the data. Doing this allows you to not only look at an individual asset, but also spot trends by truck maker, truck model, etc.
For example, you can see that a particular component problem occurs on certain model trucks at X number of miles. The data then allows you to project that it is likely that other trucks of that same model may experience the same component problems at that same mileage. You can then decide to proactively deal with the problem before the failure results in a roadside issue or decide to retire the asset to avoid the expense of replacing the component.
The bottom line: you need to look at the big picture when it comes to determining optimal asset life cycle. You can’t just look at the maintenance data — although that will tell you a great deal about the condition of your assets — but you need to include all the other factors in order to make the best possible decision about how long to keep assets based on your fleet’s specific data.
Frank Bussone has spent more than two decades providing business analytics and business intelligence to the transportation and real estate industries. For the past six years, he has helped Corcentric customers find lower cost solutions for their truck fleets by working through the big data broadcasted from trucks.