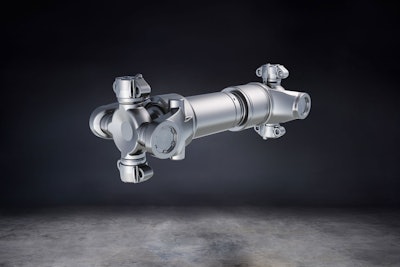
In the search for a smoother and quieter ride, industry trends such as engine downspeeding have had an effect on vehicle dynamics and harmonics, often contributing to noise, vibration, and harshness (NVH) issues.
While component manufactures and OEMs have adapted truck designs accordingly, tire imbalance, a damaged driveline, driveline imbalance and driveline angles are several potential causes for vibration in a truck that can result in driver discomfort and potential vehicle impairment, making it important to properly identify the root cause before starting any repairs.
As a first step, Dana Director of Global Driveshaft Product Planning for the Commercial-Vehicle Business Tom Bosler suggested following Dana’s step-by-step Vibration Diagnostics guide – a quick, easy-to-follow flowchart for diagnosing the most common causes of vehicle vibrations and how the issues can be addressed. Similarly, the Technology and Maintenance Council’s recommended practice (RP 648) on troubleshooting vehicle ride complaints offers a comprehensive diagnostics guideline for ride complaints in heavy-duty tractors and trucks.
“While the driveshaft or tires are often assumed to be the NVH culprit, the problem of vibration in the powertrain should be handled with a systematic approach,” Bosler said. “NVH issues may be rooted in a variety of vehicle configurations and can interact with the natural frequency of many parts of the vehicle such as the transmission, axle, suspension, clutch, tires, dashboard, door panels, or other components. A technician should investigate beyond where the immediate symptom is being experienced.”
If a driveline is suspected as the source for vibration, Meritor Chief Engineer Anthony Lentini said to first look for missing or loose parts like bolts, snap rings and balance weights.
“Inspect for other damage such as bent or dented tubes or excessive run-out, lash or end play in universal joints, slip section and center bearing indicating excess wear,” he said. “If these conditions are found, repair or replacement of components as needed will likely resolve the issue. Driveline layout can also be a source of problems if universal joint operating angles are too high or not well cancelled.”
Maintenance manuals and application guidelines are available from driveline manufacturer websites providing details and analysis tools on how to inspect shafts and driveline layouts.
If inspection of the driveshafts checks out and joint angles are within recommended limits, the next step involves more detailed troubleshooting using a vibration analyzer to determine the frequency at which the vibration occurs through the use of accelerometers.
“This will help to positively identify the root cause. The identified frequency will match the operating parameters of the source component – for example, wheel or driveshaft rpm when vibration occurs,” said Meritor Chief Engineer Jason Ley. “Placement of accelerometer sensors is critical as you’ll want to detect vibration levels where drivers feel the problem – for example, at the seat rail and steering column.”
If a vibration analyzer is not readily available, Ley and Lentini agreed that using the conditions where the issue is present can help troubleshoot. To determine if the imbalance is tire or driveline-related, turning the vehicle could help. If the vibration gets faster or slower on turns, they said, it is likely tire-related. If the vibration only is present under load or throttle, and not when in cruise, it may be an angle issue. If the vibration is in a very narrow speed range, balance or center bearing isolator would be the likely root cause.
If it’s necessary to have the shafts rebalanced, it is best practice to “system balance” where two or more shafts are connected, which will represent the assembled condition in the vehicle, Ley and Lentini said.
Isolation of driveline-induced vibrations can also be improved by changing the stiffness of the center bearing cushion. Driveline manufacturers offer a choice of cushion stiffness to optimize the isolation feature. The vehicle OEM or driveline manufacturer should be consulted before making this change.