This is the second of a two-part series that looks at the maintenance challenges presented by parking a truck for a long period of time. Part one, “Freight volume drop presents unique maintenance challenge” can be found here.
Just because a truck’s sitting idle, the same may not be true for its batteries. Parasitic loads from telematics devices and onboard computers, along with self-discharging that occurs when charging stops, will drain the power bank.
For some idled trucks, it may be only a matter of days before its batteries tank, particularly for reefer trucks, said Marcus Hester, vice president of sales and marketing for Optronics International.
In a perfect world, batteries would be maintained during downtime. However, they’re surprisingly not always on the top of a fleet’s to-do list.
“We’re expecting an unprecedented level of battery failure at this point as fleets get back to business which will result in an unprecedented level of replacement cost,” Hester said.
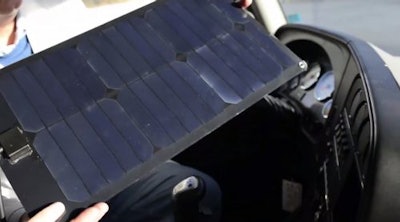
Jeff Barron, manager of engineering and technical services for Interstate Batteries, also painted a grim picture for fleets that skip battery maintenance.
“We’ve got to make sure [batteries] are ready to hit the ground running, because if not, you’re going to see thousands and thousands of trucks that aren’t going to be starting when this thing comes back around,” Barron said.
But parked trucks do present some opportunities, at least on a maintenance front.
“Now’s the perfect time to do a PM before you get back out on the road, and that entails checking your batteries,” Barron said. “Check the connectors. Clean off any corrosion. Retorque them back down just to make sure, because these trucks are going to vibrate, and these nuts don’t stay tight on there forever, so the vibrations can wiggle them loose.”
Larry Rambeaux, sales manager for Purkeys, said preventive maintenance is key before parking the truck and should include eliminating as many parasitic loads as possible.
“Run that thing through the shop, and while it’s there, give it a once-over,” Rambeaux said. “Disable the tracking system. Take a shop roll-around charger, and hook it up to the truck the whole time it’s sitting there getting service so that you’re charging those batteries. That way, when you do take it outside and park it, they should be 100%.”
Stede Granger, technical services manager for Shell Lubricants, suggested investing in a trickle charger, while Salter suggested disconnecting the negative battery terminal.
“This will help prevent parasitic electrical loads like computers from draining the batteries,” Hogg added.
However, some fleets would rather pass on disconnecting batteries.
“The easiest thing to do is when you park the truck is to disconnect the battery cables,” Rambeaux said. “That costs you five minutes of labor. The problem is that you tell somebody that, and they say, ‘We don’t have time to do that.’ OK, so you don’t have time to pull a ground cable, but you’ve got time to send guys out there to do jumpstarts or put new batteries in a truck?”
Barron agreed that for some fleets, disconnecting batteries will make sense, while for others, it may invite some headaches.
“The key thing that would be ideal is to disconnect the batteries altogether,” Barron said. “But a lot of these more sophisticated trucks that are out there, if they lose battery power altogether, there are a whole lot of things that actually have to come into play once you hook these things back up.”
For a truck that has to “relearn” optimum engine settings, disconnecting its batteries may not be a comfortable option for some fleets. “A lot of times, that’s not an option, to basically unhook them,” Barron said. “It’s better to roll out a booster charger or something to get a charge back into those batteries.”
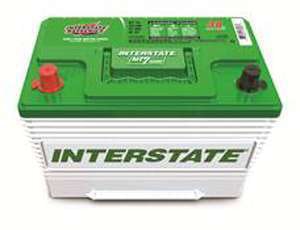
If outlets are nowhere in sight, solar charging and battery disconnect switches can prove helpful.
“Some fleets also connect solar panels to their batteries to help keep them charged,” said Homer Hogg, director of technical service for TravelCenters of America. “Some trucks have disconnect switches which do shut off some computers but in most cases will not disconnect enough computers to prevent excessive amp draw over time.”
Solar charging can prove to be a sound option as long as fleets are mindful of its limitations.
“[Purkeys Solar Dash] is a small solar panel that you throw on the dash of the truck and plug it into the cigarette lighter,” Rambeaux said. “It will offset those parasitic loads. It’s designed to maintain batteries. If you charge the batteries and park it and put it on, it can keep them charged. It was not designed to charge dead batteries. That would take a much larger panel.”
While solar can be an attractive option that eliminates the need for dragging around chargers and extension cords, it’s not always practical.
“I think it can be effective, but what if we get into a period of bad weather for a week, and you get overcast skies, and you don’t get the output that you need from a solar collector system that can adequately feed the batteries?” said Brett Miller, engineering manager for Optronics International.
Regardless of whether a plug-in charger or a solar panel is used, monitoring battery condition is key.
“It’s always going to require, in my opinion, somebody going up to it and manually checking it to ensure that what happened actually did happen,” Miller said.
An old practice of briefly running a truck to recharge its batteries is no longer a sound option.
“The old thing used to be, ‘You just go out, start it up, let it run for 20 or 30 minutes, and it’ll be fine,’ ” Barron said. “That’s no longer the case, especially in diesel trucks, which require a lot of amperage when cranking. Plus, when you’re looking at the initial warming-up of the glow plugs, it takes time, and it really pulls down the batteries. If they actually have a way to plug a charger into the battery, some kind of a trickle charge or some kind of charge in general, that’s great.”
Barron said if maintenance charging through trickle and solar chargers can’t be penciled into the budget, then at least opt for once-a-month charging, which may take up to 48 hours for recharging depending on voltage level. But if running chargers around to parked trucks isn’t much of an option, fleets may want to consider maintaining a used battery bank.
“We’ve actually got a lot of fleets that actually store used batteries,” Barron said. “They’ll take and match up batteries that are the same capacity ratings, and they’ll use those as spares. They’ll keep them on a charge while they’re there in a battery barn. This gives them another upper hand as far as having something right there to replace out.”
Letting batteries go dead and then reviving them later isn’t a sound choice. Left uncharged long enough, batteries will begin to sulfate, which will lessen their power and shorten their lifespan, paving the way for downtime and increased replacement costs.
“Instead of having a 1,000 CCA, you may have only 800 CCA,” Barron said of recharging a dead battery. “Your degradation just continues on with nonuse, so that’s why it’s very important to make sure there’s some kind of charge going into these batteries.”
Keep the lights on and the current flowing
While COVID-19 lockdowns have hampered freight movement and have fleets scrambling to pinch pennies, maintenance should remain a priority.
“We’ve got a catch-22,” Rambeaux said. “We’ve got slow freight, so we’ve got trucks parked, but then everybody’s worried about spending money, so it’s danged if you do and danged if you don’t.”
Still, that’s no excuse for not taking the time to do some spring cleaning on lighting and electrical systems.
“We just went through a winter, and these trucks have been running 27 different chemical compounds for deicing and snow and everything else,” Rambeaux said. “Open those connectors up, and make sure they are clean. It’s not going to get any better with time, so you might as well fix it now while you have time and it’s at your place versus having that corrosion cause you a CSA violation down the road.”
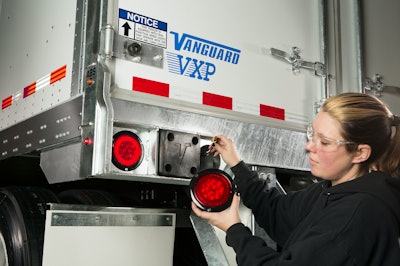
Brett said the frequency of checking connections can vary.
“We think it’s a good maintenance procedure to open each of those connection points on a three- to five-year basis, and it may depend on your operating conditions, it may depend on the weather you’re experiencing and the places that you run, and other things of that nature,” he said. “Do a visual inspection to see if there is any corrosion that has started, and clean it if necessary, make any corrections that are necessary to stop further corrosion, and then reapply new dielectric grease to it before mating it back together again.”
Also be sure to check for signs of condensation and moisture in light housings.
“Ideally, there shouldn’t be any if the lamp is built properly and installed properly and has an adequate connection from the harness to the light,” Hester said. “But we all know that moisture intrusion does happen, so it’s definitely a good time to be looking for that.”
Moisture intrusion can lead to corrosion issues and light malfunctions. On this front, LEDs may fail before incandescents.
“LED lights operate on a certain voltage window, and if they drop below that, they go from working just fine to not working,” Rambeaux said. “Versus an incandescent, which may have a bit more corrosion than it did last week and it’s just a little bit dimmer. But with an LED, that is not the situation. They hit that set point, and they go from working fine to nothing.”
John Golden, sales manager for Whelen Engineering, said the two biggest truck-related problems his company sees in the field are moisture intrusion and improper installation.
“People don’t follow the instructions carefully, so they end up mounting the products improperly onto vehicles, like upside, and that can lead to water issues,” Golden said. “The other common thing we see is a phenomenon called wicking, which is where water comes up between the strands of the wires. With the hot and cold cycles of the lights, when things cool down, it acts as a giant straw to pull moisture into devices.”
Wicking results in wire corrosion and can lead to eventual connectivity failure. Preventing it can be an ongoing battle given the harsh conditions of the road.
Whelen now has a patented water-block technology that it recently started building into its products to prevent moisture from coming up through the wires and into the electronics, Golden said. “Otherwise, you have to make sure to use weatherproof connectors and really good procedures with sealing up electrical connections,” he said.
Brett said to take the time to check for damage on cable and wire looms.
“Maybe something kicked up off the road and nicked open a jacket or a conductor somewhere that’s going to be an entry point for corrosion,” he said. “Make sure that the harness is installed in a way where it’s not vibrating against the frame and abrading itself down to copper or anything like that.”
Now that winter has passed, power demands will increase, which requires keeping an eye on alternator performance.
“You don’t have nearly the electrical loads in winter, because you’re not running the air conditioner,” Rambeaux said. “A lot of times, you can have a weak alternator that will make it just fine throughout winter because of those reduced loads, plus batteries don’t want to take a charge when they’re cold. You could have an alternator that’s lost a diode, and just for easy math, if you have a 135-amp alternator and you lose one diode in it, now you have a 90-amp alternator, because you just lost a third of its performance.”
To help gauge charging performance, load-test batteries, and perform a voltage drop test on alternator cables.
“You could have the best batteries in the world and the best alternator in the world, but if you don’t have good cables connecting them, all bets are off,” Rambeaux said. “It still doesn’t work, and that can be either defective cables from the factory or just age and corrosion, because again, you’ve got that 135-amp alternator, but if you’ve got cables that can only handle 100 amps, it doesn’t do you any good, because the cables can’t handle it. All this goes back to getting those batteries at 100%, which is very important right now if we’re going to park those trucks.”
Stop on a dime
Keith McComsey, director of marketing and customer solutions for Bendix Spicer Foundation Brake, didn’t hesitate when asked about how to make the most of COVID-19 downtime.
“This is a good time to do a full wheels-off inspection,” he said.
For air disc brake systems, perform a visual inspection of the caliper, carrier, pads and rotor, McComsey said.
“Verify caliper slide-ability, and inspect pads for irregular wear,” he said. “Measure pad and rotor thicknesses. Inspect the rotor for cracks. Check boots for holes and tears.” To access Bendix’s troubleshooting guide with visual pictures, go to bendix.com, select “document library,” and search for BW7610.
For foundation drum brake systems, perform a complete visual inspection of the brake shoes, S-cam, drum and other components, McComsey said.
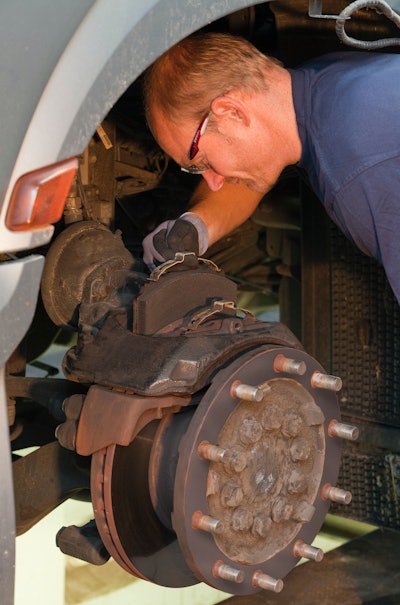
“Inspect shoe friction for irregular wear, cracks, etc.,” he said. “Measure shoe friction and drum ID (inside dimension). Inspect the drum for cracks and martensite (or ‘leopard spotting’). Make sure brakes are greased by adding grease at each of the grease fittings on the brake cam tubes and slack adjusters. This not only gets new grease into the system but helps remove contaminants and moisture that may have gotten in.”
Kevin Rose, regional sales manager for Wabco, said take the time to test drum brakes.
“Check each wheel end (using an applied stroke test) to determine if brakes exceed the adjustment limit,” Rose said. “Inspect brake adjusters, and ensure all greasable points are greased properly. Check for proper operation of stability and anti-lock braking (ABS) systems. Ensure the ABS light comes on after turning the key to the ‘on’ position, and the light should turn off after a few seconds. If available, run diagnostics software, such as Wabco Toolbox, to accurately and quickly diagnose critical systems.”
Rose also recommended occasionally running parked trucks to help keep them in top shape.
“Taking the time now to ensure proper maintenance is performed on your equipment will save on costly repairs, road calls and production loss,” he said. “Perform a battery test, and if trucks are sitting idle for a long period of time, have someone crank the units at least twice a week. Let them run long enough to allow the lubricants to flow through the engine to ensure no drying out of seals or dead batteries from heat. Ensure all external items are turned off, such as unattended refrigerators, radios, CBs and auxiliary items.”