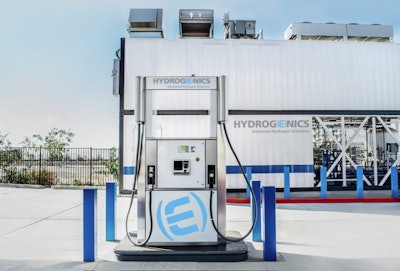
This is the second part in a multi-part series exploring the costs and viability of fuel cell technology as an alternative to diesel-powered Class 8 trucks. See the rest of series at this link.
A fuel cell truck runs a hybrid-powertrain that uses hydrogen to generate the electricity that powers the truck’s motors and can concurrently charge the truck’s powertrain battery.
To create electric power, fuel cells introduce hydrogen and oxygen to a catalyst usually comprised of platinum which causes an electro-chemical reaction that produces electricity, water and heat. That electricity then powers the components that turn the wheels of the truck.
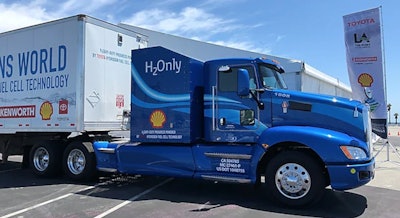
Platinum is the catalyst of choice, which at roughly $900 per ounce, drives up the cost. Still, costs can come down as demand increases. With California – the nation’s most populated and truck-active state – requiring OEMs to offer zero-emission trucks and vans starting in 2024, demand for fuel cells is expected to increase.
Being the most prolific element in the universe, one of hydrogen’s core benefits is that it can be produced from a variety of sources like water, fossil fuels, ethanol and renewable natural gas.
Likewise, proponents say another draw is that, from the perspective of an end user like a fleet or driver, fuel cells have a fueling mechanism similar to diesel. Hydrogen fueling is fairly simple — stick a nozzle in a tank and fill it up, often in as little as 10 minutes.
However, fueling is also a key roadblock to adoption: A map posted to Department of Energy’s (DOE) Alternative Fuels Data Center website shows 46 hydrogen stations in the United States — 43 of which are located in California and only two are capable of fueling trucks.
Fuel providers like Shell are working to expand that network.
Kenworth recently announced that it would be rolling out 10 additional T680 fuel cell trucks in partnership with Toyota for use at the Port of Los Angeles. As with Kenworth’s other fuel cell test mules, Shell will provide the hydrogen. Still, it’s the high cost of building stations for a very nascent and small market that keeps other major fuel suppliers sitting on the sidelines. An increase in demand for fuel cell trucks could change that.
“The cost really lies in the compression, dispensing and cooling,” said Nico Bouwkamp, technical manager of the private-public California Fuel Cell Partnership. “Because there are not a lot stations there is not a lot of demand for that kind of equipment yet so the cost right now is going to be high. Even though the volumes are higher because they’re trucks, and because there are a good number of trucks on the road that immediately creates a much higher and predictable demand than it does cars, there are still so few stations.”
Ninety-five percent of the 10 million metric tons of hydrogen currently produced in the U.S. is sourced from natural gas through a steam-filled process called reforming. The DOE reports that it’s the “cheapest, most efficient, and most common” means of hydrogen production.
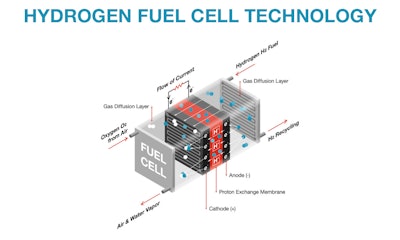
Since natural gas is a fossil fuel with a carbon index (CI) score near diesel (both of which hover around 100, according to the California Air Resources Board) there’s been a shift among producers — particularly in the transportation sector — to obtain hydrogen from renewable sources like water and renewable natural gas.
Though renewable natural gas has the lowest CI score of all fuels at -410 (it’s sourced from methane, which the U.S. Environmental Protection Agency and CARB consider 21 more times destructive to ozone than carbon dioxide), obtaining the fuel from methane and then further processing it into hydrogen requires additional infrastructure and cost. Nonetheless, renewable gas producer Amp Americas CEO Grant Zimmerman said that process costs less than electrolysis which is used to obtain hydrogen from water.
“RNG to hydrogen is more economical and provides superior greenhouse gas impact versus electrolysis,” Zimmerman said. “Small scale hydrogen production from electrolysis will likely become more important over time as the technology improves and costs come down. For now, electrolysis is very expensive, limiting its deployment. With very low carbon intensity RNG, the climate benefits are actually greater than using zero carbon power in an electrolysis operation.”
Still, proponents for electrolysis say RNG’s supply line is somewhat limited with dairies, sewage treatment plants and landfills being among the top sources for the gas. Plus, incentives tied to RNG use has dramatically increased its demand among fleets using natural gas engines.
Enter water and the growing trend to use electrolyzers powered by renewable energy sources like solar and wind to obtain hydrogen from water through electrolysis. Nikola Motors Founder and Executive Chairman Trevor Milton said the key is to employ electrolysis on a large scale, which for Nikola has dramatically reduced the cost of hydrogen to the point that it’s now undercutting diesel.
“I think that’s where Nikola’s main success really is, to be honest with you,” Milton said. “When we started this, hydrogen was $16 a kilogram. We’re now down way below $4. We’re pushing $2.50 almost. That’s our goal, $2.50 now. So, we’re way below $4 and now we’re cheaper than diesel to operate.
“The key to that was massive production of hydrogen,” Milton continued. “Everyone was doing these little tiny stations that were very expensive to capitalize and service. When you go to large scale, like each one of our stations will do over 8,000 kilograms a day — that’s bigger than any station in the world. Your cost to produce anything is incredibly cheaper, much cheaper when you go that route.”
Cummins, which has been involved in fuel cell and hydrogen fueling efforts for the past 20 years, is also pursuing electrolysis. Its acquisition of Hydrogenics in late 2019 opened the door to additional electrolysis and fuel cell R&D.
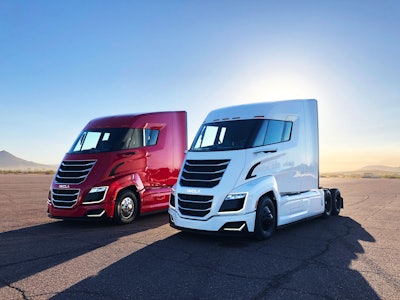
Cummins CEO Tom Linebarger said there has never been a better time for Cummins, other OEMs and governments around the world to invest in hydrogen infrastructure. “As a result of the COVID pandemic, our economies are all significantly impacted, many damaged for years potentially,” he said. “In order to restart these economies and build up again we need to make investments, and why not make investments in those parts of the economy that will last us for the next 100 years, that will build foundations for how we want to provide energy and transportation in the future?”
The U.S. Department of Energy Assistant Secretary for the Office of Energy Efficiency and Renewable Energy, Daniel Simmons, announced earlier this year that the DOE would set aside $100 million for the construction of an industry-ready Class 8 fuel cell truck and funding for electrolyzer R&D to improve and increase H2 production through electrolysis.
“Collectively, we’ve made tremendous progress on fuel cells, electrolyzers and fundamental materials,” Simmons said. “But hydrogen infrastructure – the cost, the durability and widespread distribution – remains a critical barrier.”
Milton agrees.
“I think the key now is getting the network out,” he said.“That’s a big one. The network is probably the biggest problem right now in hydrogen. We’re building 700 stations in America. For the next five years, we’ll have a lot of coverage throughout the country with hydrogen. In Europe, we have multiple stations going up, too. In the next five to 10 years you’ll have complete coverage everywhere you want to go with hydrogen.”
Previously in this series: With zero-emissions truck mandates coming, OEs promise ‘cheaper than diesel’ hydrogen fuel cells — but key hurdles remain
Next in this series: ‘You can’t just fill a battery’: Proponents say hydrogen power is trucking’s best path forward, critics argue otherwise